Sink marks in injection moulding represent a common yet critical defect that can significantly impact the aesthetics and quality of the final product. These depressions occur on the surface of a molded part when the shrinkage of the inner material is not compensated during the cooling process, leading to uneven surfaces and potential structural weaknesses. Understanding the causes of sink marks is essential for manufacturers who aim to maintain the integrity and appearance of their plastic products. By minimizing these defects, businesses can enhance product appeal and reliability, ultimately bolstering market competitiveness. In this document, we will delve into the causes of sink marks, their impact on product quality, and effective strategies for their prevention, thereby guiding industry leaders in optimizing their manufacturing processes.
Understanding Sink Marks
What is Sink Mark in Plastic?
Sink marks in plastic are surface depressions that occur in molded parts. These imperfections manifest as slightly recessed areas on the surface, where the internal material has shrunk more than the surrounding areas during cooling. This phenomenon typically arises due to improper material flow or insufficient cooling time. When the outer layer of the plastic part cools and solidifies faster than the internal material, the latter tends to pull inward, creating these undesirable indentations. These sink marks can compromise not only the aesthetic appeal of the product but also its structural integrity. Recognizing the presence and implications of sink mark defects is crucial for manufacturers to address them promptly. By understanding the dynamics of material shrinkage and cooling, businesses can take informed steps to refine their injection moulding processes, thus ensuring higher quality and more visually appealing plastic products.
Sink Mark Causes and Effects
Sink marks in injection moulding are primarily caused by uneven cooling and inadequate packing pressure during the moulding process. When the outer layers of a molded part cool and solidify faster than the interior, the internal material contracts, leading to surface depressions. Insufficient packing pressure, which should counteract this shrinkage, often exacerbates the problem. Additionally, the design of the part, including wall thickness variations and sharp corners, can further contribute to the formation of these defects.
The effects of sink marks extend beyond aesthetics. While they compromise the visual appeal of a product, making it appear flawed, they can also indicate potential weaknesses in the part’s structure. Such defects may reduce the product’s durability and longevity, impacting consumer satisfaction and increasing the likelihood of returns or complaints. Therefore, understanding sink mark causes is vital for manufacturers seeking to improve both the quality and performance of their molded products.
Sink Mark in Injection Moulding Process
The injection moulding process is prone to the formation of sink marks due to its inherent characteristics. During this process, molten plastic is injected into a mould cavity, where it is allowed to cool and solidify. The cooling phase is critical, as it determines the final shape and surface quality of the molded part. If the cooling is uneven, with some areas solidifying faster than others, the material’s shrinkage can lead to sink mark defects.
To mitigate sink marks in injection moulding, precise control over processing parameters is essential. This includes managing the temperature, pressure, and cooling time effectively. Moreover, the design of the mould and the part itself should accommodate uniform thickness and gradual transitions to minimize stress points. By implementing these strategies, manufacturers can significantly reduce the prevalence of sink marks, resulting in higher quality products that meet both aesthetic and functional standards.
Impact on Product Aesthetics
How Sink Marks Affect Appearance
Sink marks can drastically affect the visual appeal of plastic products, making them less attractive to consumers. These defects manifest as small depressions on the surface, disrupting the smooth, uniform look that is often desired in finished goods. In consumer products, such imperfections can convey a perception of poor quality or flawed manufacturing processes, leading to diminished brand reputation and reduced customer confidence.
In industries where aesthetics play a crucial role, such as consumer electronics, automotive interiors, and household goods, the presence of sink marks can be particularly detrimental. Customers in these markets often associate a polished, flawless finish with higher quality and value. Therefore, manufacturers must prioritize addressing sink mark issues to ensure their products meet consumer expectations. By doing so, they can enhance the overall attractiveness of their offerings, fostering a positive brand image and encouraging customer loyalty.
Importance of Minimizing Sink Marks
Minimizing sink marks is crucial not only for aesthetic reasons but also for maintaining the functional integrity of plastic products. When sink marks are present, they often indicate uneven material distribution and internal stress, which can lead to weakened structural properties. This is particularly important in industries where product durability and reliability are paramount, such as automotive or aerospace.
From a market perspective, products free of visible defects like sink marks are more likely to meet consumer expectations and regulatory standards. This can enhance brand reputation and customer satisfaction, providing a competitive edge in a crowded marketplace. Furthermore, reducing the occurrence of sink marks can lead to cost savings by minimizing rework, reducing scrap rates, and ensuring faster time-to-market for new products. Therefore, manufacturers are encouraged to invest in process improvements and quality control measures that help eliminate these defects, ensuring both aesthetic and structural excellence in their offerings.
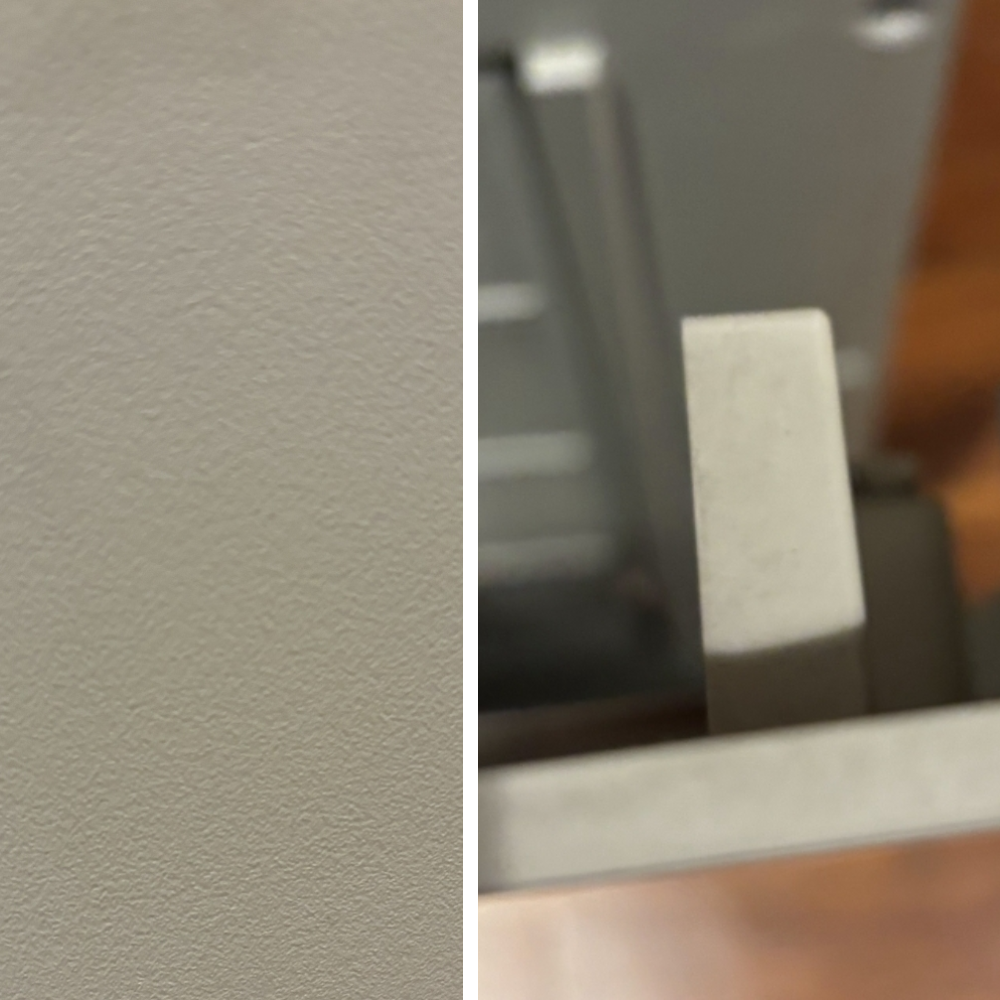
Solutions and Prevention Strategies
How to Avoid Sink Marks in Injection Molding
To avoid sink marks in injection molding, manufacturers should focus on optimizing the molding process and part design. Key strategies include:
- Uniform Wall Thickness: Designing parts with consistent wall thickness reduces the likelihood of uneven cooling and shrinkage, thereby minimizing sink mark defects.
- Optimized Cooling: Implementing a well-designed cooling system ensures even temperature distribution throughout the mold, which can prevent premature solidification and internal stress.
- Proper Packing Pressure: Applying adequate packing pressure during the molding process helps compensate for material shrinkage, reducing the formation of depressions on the surface.
- Material Selection: Choosing materials with lower shrinkage rates can inherently reduce the risk of sink marks.
- Mold Design Adjustments: Incorporating features like ribs or gussets can support thicker sections, preventing excessive shrinkage in those areas.
By adopting these practices, manufacturers can significantly enhance the quality and appearance of their molded products, ensuring they meet both consumer and industry standards.
Techniques to Reduce Sink Mark Defects
To effectively reduce sink mark defects, manufacturers can implement several advanced techniques throughout the injection molding process.
- Process Optimization: Adjusting parameters such as injection speed, pressure, and temperature can help achieve a more uniform filling and cooling cycle, reducing the chances of sink marks.
- Gate Design: Utilizing multiple or strategically placed gates can ensure balanced material flow and consistent filling, which mitigates the risk of surface depressions.
- Cooling System Enhancements: Incorporating conformal cooling channels that match the shape of the mold cavity can provide more efficient and uniform cooling, preventing localized shrinkage.
- Use of Fillers: Adding fillers to the plastic material can decrease shrinkage rates, reducing the tendency for sink marks to occur.
- Simulation Software: Employing computer-aided engineering (CAE) tools allows for predictive analysis and optimization of the molding process, enabling early detection and correction of potential issues.
By embracing these techniques, producers can systematically diminish sink mark occurrences, improving both product quality and production efficiency.
Talk to us about improving your injection moulding!