In the intricate world of manufacturing, particularly in injection moulding, the presence of sink marks can significantly impact both the aesthetic and functional quality of a product. A sink mark, often perceived as a cosmetic defect, occurs when the surface of the plastic part shows sunken areas due to uneven cooling or insufficient packing pressure during the moulding process. These sink mark defects not only detract from the visual appeal of the final product but can also compromise its structural integrity, leading to potential issues in performance. Therefore, understanding what causes sink marks in plastic and how to avoid sink marks in injection molding is crucial for manufacturers aiming to deliver high-quality, durable products. This piece will delve into the importance of minimizing sink marks, highlighting innovative strategies and techniques to enhance both the appearance and durability of your products.
Understanding Sink Marks in Injection Moulding
What is Sink Mark in Plastic?
A sink mark in plastic is a subtle depression or dimple that appears on the surface of an injection moulded part. It typically manifests due to the varying shrinkage rates of plastic materials as they cool and solidify inside the mould. These sink mark defects are often the result of insufficient packing pressure, uneven cooling, or thick wall sections that prevent uniform hardening. The defect not only detracts from the aesthetic appeal but may also suggest underlying issues with the moulding process itself.
This can lead to reduced part strength and compromised performance. Recognizing the presence and implications of sink marks is vital for manufacturers who strive to uphold the quality and durability of their products. By understanding the sink mark causes, businesses can take proactive measures to refine their injection moulding techniques, ensuring each product meets the highest standards of excellence.
Sink Mark Causes and Effects
Sink mark causes in injection moulding primarily stem from three factors: inadequate packing pressure, uneven cooling rates, and non-uniform wall thickness. Inadequate packing pressure during the moulding process can lead to insufficient material filling, resulting in sunken areas on the part surface. Uneven cooling often occurs when parts have varying thicknesses, causing some sections to solidify faster than others. Non-uniform wall thicknesses exacerbate this issue by creating differential shrinkage as plastic cools.
The effects of sink mark defects extend beyond aesthetics, potentially compromising the structural integrity of the part. This can lead to reduced strength and durability, making the product prone to failure under stress. Understanding these causes not only helps in identifying potential weaknesses in the manufacturing process but also aids in implementing corrective measures. By addressing these root causes, manufacturers can enhance product quality and ensure consistent performance.
Impact on Product Appearance
Sink mark defects significantly impact the visual appeal of injection moulded products. These imperfections create noticeable dimples or depressions on the surface, detracting from the smooth, polished finish that is often desired. This can be particularly detrimental for consumer-facing products where aesthetics play a crucial role in purchasing decisions. Poor appearance due to sink marks may lead customers to perceive the product as lower quality, affecting brand reputation and customer satisfaction.
Furthermore, products with visible sink marks may struggle to meet industry standards for aesthetic quality, leading to increased rejection rates and costs associated with rework or scrap. In competitive markets, maintaining a flawless appearance is essential to differentiate products and uphold brand value. By understanding how to avoid sink marks in injection molding, manufacturers can ensure their products not only function effectively but also maintain an appealing appearance that meets customer expectations.
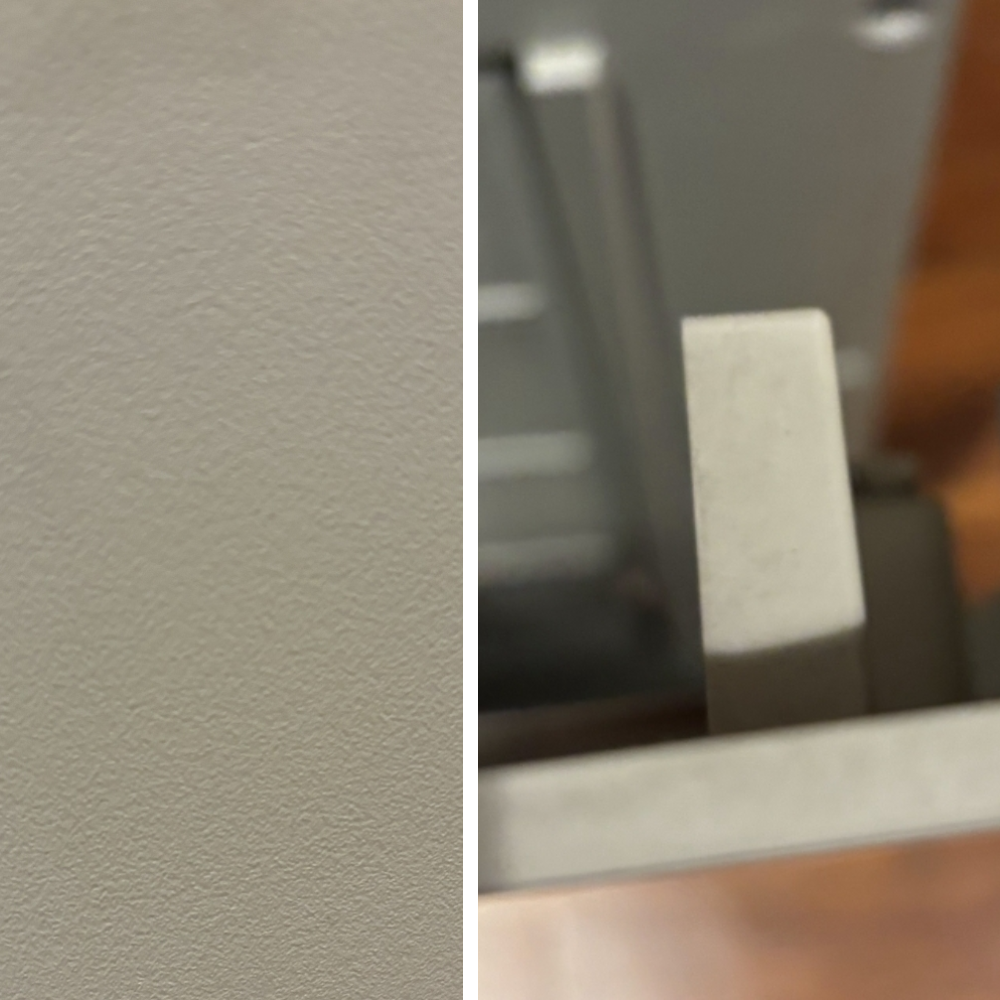
Strategies to Avoid Sink Marks
Optimizing Injection Moulding Parameters
To avoid sink marks in injection molding, it is essential to optimize key moulding parameters. One critical factor is the packing pressure; ensuring adequate pressure during the packing phase can help fill out the mould cavity completely, reducing the likelihood of sink marks. Adjusting the cooling time is another vital strategy. By allowing sufficient time for even cooling, manufacturers can minimize differential shrinkage that leads to sink marks.
Additionally, temperature control is crucial. Maintaining a consistent mould temperature helps achieve uniform solidification and can prevent surface defects. Another consideration is the injection speed; a slower injection speed can reduce turbulence and ensure a more uniform material distribution within the mould. By carefully analyzing and adjusting these parameters, manufacturers can significantly reduce the occurrence of sink mark defects. This approach not only enhances the visual quality of the product but also reinforces its structural integrity, ensuring a high standard of performance.
Material Selection and Design Considerations
Material selection plays a pivotal role in minimizing sink marks in plastic products. Choosing materials with lower shrinkage rates can significantly reduce the formation of sink marks. Thermoplastics with consistent shrinkage properties ensure a more uniform cooling process, thereby mitigating the chances of surface imperfections. Additionally, design considerations are crucial.
Uniform wall thicknesses should be prioritized to avoid differential cooling, which is a common sink mark cause. Incorporating ribbing or structural supports can also help maintain dimensional stability and reduce the thickness of thicker sections without compromising strength. Moreover, employing computer-aided design (CAD) tools allows for precise modeling of mould flow and cooling patterns, helping to predict and address potential sink mark issues before production begins.
By focusing on these material and design strategies, manufacturers can effectively reduce sink mark defects, thereby enhancing both the aesthetic and functional quality of their injection moulded products.
Advanced Techniques to Minimize Sink Mark Defects
Implementing advanced techniques can further mitigate the risk of sink mark defects in injection moulded products. One such technique involves using gas-assisted injection moulding, which helps in maintaining uniform pressure and reducing areas of thick material that are prone to sink marks.
Another approach is the application of sequential valve gating, which allows for the control of material flow into different sections of the mould, ensuring even filling and minimizing sink marks in complex designs. Additionally, employing conformal cooling channels within the mould can drastically improve cooling efficiency, leading to more uniform solidification of the plastic and reducing the risk of sink marks.
Utilizing simulation software can also provide insights into potential sink mark areas, allowing for preemptive design adjustments. By leveraging these advanced methods, manufacturers can enhance precision in moulding processes, thus ensuring their products meet high quality and aesthetic standards without the common pitfalls associated with sink marks.
Importance of Minimizing Sink Marks
Enhancing Visual Appeal and Marketability
Minimizing sink marks is crucial for enhancing the visual appeal and marketability of injection moulded products. A flawless surface finish significantly contributes to the perceived value of a product, making it more attractive to consumers in competitive markets. Products that exhibit a high-quality appearance without visible defects like sink marks are more likely to capture consumer attention and build brand trust. This perceived quality can directly influence purchasing decisions, especially in industries where aesthetics are integral, such as consumer electronics, automotive, and home goods.
Additionally, products with superior visual appeal often command higher price points, improving profitability. By focusing on reducing sink mark defects, manufacturers not only improve the aesthetic quality of their products but also enhance their market competitiveness. This focus on quality helps establish a strong brand reputation, fostering customer loyalty and expanding market reach. Ultimately, minimizing sink marks supports long-term business success by aligning product offerings with consumer expectations.
Ensuring Product Durability and Quality
Minimizing sink mark defects is integral to ensuring the durability and quality of injection moulded products. Sink marks, while often perceived as cosmetic, can indicate deeper issues related to material distribution and structural integrity. These defects may lead to weak points within the product, making it more susceptible to stress and wear over time. This vulnerability can result in premature failure, compromising the product’s lifespan and performance. By addressing sink mark causes, manufacturers can enhance the material consistency and structural robustness of their products.
This improvement not only ensures that products meet rigorous quality standards but also reduces the likelihood of returns and warranty claims. Furthermore, producing durable products helps maintain brand credibility, reinforcing customer trust and satisfaction. By prioritizing strategies that prevent sink marks, manufacturers can deliver high-quality, reliable products that meet consumer expectations and withstand the test of time, thereby safeguarding their brand reputation and market position.
Building Customer Trust and Brand Reputation
Minimizing sink marks is essential for building customer trust and enhancing brand reputation. In today’s competitive marketplace, consumers expect high-quality products that not only function well but also look impeccable. Visible defects such as sink marks can erode consumer confidence, as they may perceive these imperfections as indicators of a lack of attention to detail or inferior production processes. By consistently delivering products free of sink mark defects, manufacturers demonstrate their commitment to quality and precision, fostering trust among their customer base.
This trust translates into brand loyalty, as satisfied customers are more likely to return for future purchases and recommend the brand to others. Furthermore, a reputation for producing high-quality, defect-free products can differentiate a brand from its competitors, opening doors to new markets and opportunities. Ultimately, minimizing sink marks contributes to a positive brand image, supporting long-term success and growth in the industry.