在竞争激烈的制造业中,实现塑料注塑成型工艺的稳健性是确保零件质量一致性和制造效率的关键因素。并行工程成为解决成型工艺固有复杂挑战的关键策略,促进设计、工程和生产团队之间的无缝协作。通过整合并行工程实践,公司可以增强质量保证、优化设计验证并简化操作以满足客户的严格标准。在本文中,我们将深入探讨影响零件质量一致性的五个关键因素,并探讨如何采用并行工程来实现稳健高效的成型工艺,从而使公司成为行业领导者。
工艺稳健性的重要性
影响零件质量的因素
在塑料注塑成型中,零件质量的一致性受多种关键因素的影响。材料选择至关重要,因为它会影响最终产品的强度、耐用性和光洁度。正确的材料选择可确保零件符合所需规格并在其使用寿命内可靠运行。此外,模具设计也起着至关重要的作用。必须仔细关注型腔设计、冷却通道和顶出机制,以防止出现翘曲或填充不完整等缺陷。必须严格控制和监控温度、压力和注射速度等工艺参数,以保持零件生产的一致性。此外,设备维护对于避免任何可能影响零件质量的意外停机或故障至关重要。通过了解和优化这些因素,制造商可以显著提高工艺稳健性和零件质量一致性,从而提高寻求高性能塑料部件的客户的满意度。
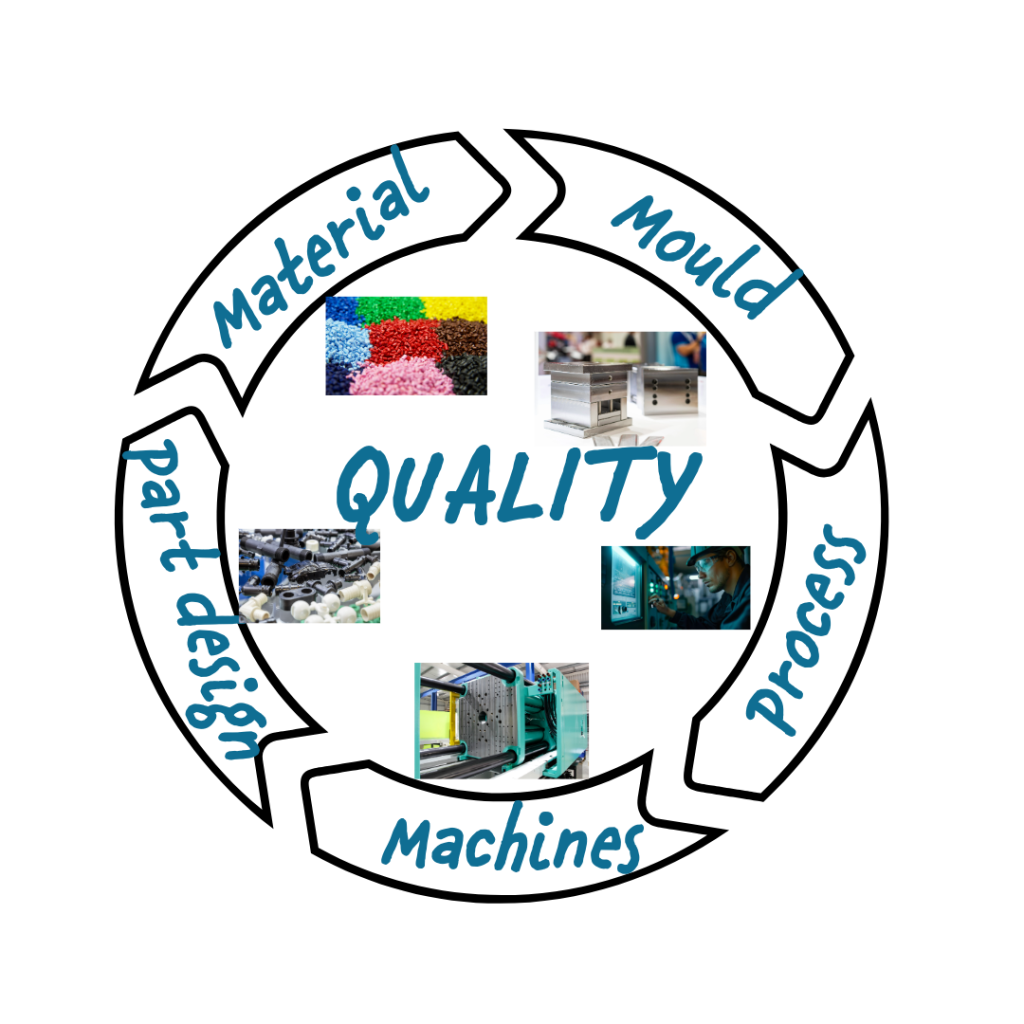
实现一致的成型工艺
实现一致的成型工艺对于保持塑料注塑成型中零件质量的一致性和制造效率至关重要。这种一致性取决于设计、材料和工艺参数的协调。通过采用并行工程,团队可以从一开始就协同工作,确保设计考虑与材料能力和工艺约束保持一致。在整个生产过程中实施强大的质量保证协议至关重要。这包括定期检查和测试,以迅速发现和纠正任何偏差。此外,利用预测分析和实时监控系统等先进技术可以提高工艺稳定性。这些工具使制造商能够在问题升级之前发现潜在问题,从而确保无缝操作。对员工的持续培训和技能发展也发挥着至关重要的作用,使他们能够有效地管理和调整流程。这些策略共同增强了成型工艺的整体稳健性,有助于持续交付高质量的塑料零件。
并行工程的作用
提高制造效率
并行工程通过促进集成工作流程和缩短产品上市时间,显著提高了塑料注塑成型的制造效率。通过在产品开发阶段早期让跨职能团队参与进来,公司可以主动解决潜在的设计和流程问题。这种协作方法可以最大限度地减少昂贵的重新设计,并确保生产的各个方面从一开始就保持一致。并行工程还有助于更好地管理资源。通过跨部门同步活动,制造商可以优化调度、缩短交货时间并提高产量。此外,该策略通过营造一个可以快速共享和采纳反馈的环境来支持持续改进。利用并行工程实践,企业可以快速适应需求或规格的变化,而不会牺牲质量。通过这种方法实现的效率提升不仅可以节省成本,还可以提高公司的可靠性和创新声誉,最终吸引更多对高质量、精密设计的塑料零件感兴趣的客户。
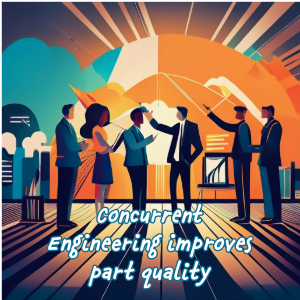
确保质量保证
将并行工程纳入塑料注塑成型工艺对于确保可靠的质量保证至关重要。这种方法可以尽早发现和解决潜在的质量问题,从而降低最终产品出现缺陷的可能性。通过同时参与设计、工程和质量保证团队的工作,公司可以制定更全面的质量控制措施,以解决生产的每个阶段。这种协作可确保始终符合所有产品规格和标准。并行工程还支持集成先进的质量保证工具,例如统计过程控制和自动检查系统,从而提高质量评估的准确性和可靠性。此外,定期的跨部门审查有助于持续监控和改进质量协议。通过在并行工程框架内优先考虑质量保证,制造商不仅可以实现更高的零件质量一致性,还可以建立客户信任,最终在竞争激烈的制造业领域成为精度和可靠性方面的领导者。
设计验证策略
提高零件质量的一致性
通过设计验证提高零件质量一致性对于塑料注塑行业至关重要。有效的设计验证可确保零件不仅功能齐全,而且可靠耐用。通过实施并行工程,团队可以在生产开始之前协作评估和改进设计,识别可能影响质量的潜在缺陷。这种主动方法可以尽早进行调整,最大限度地降低缺陷风险并确保最终产品符合所有规格。先进的仿真工具在此过程中发挥着至关重要的作用,使工程师能够在各种条件下测试和验证设计,而无需物理原型。这些工具有助于预测材料在成型过程中的表现,从而优化设计参数。此外,跨职能团队参与的迭代测试和反馈循环可确保持续改进。通过专注于设计验证,制造商可以实现卓越的零件质量一致性,满足客户的苛刻期望并加强其市场地位。
塑料注塑成型的创新
塑料注塑成型的创新正在彻底改变制造商处理设计验证和工艺稳健性的方式。一项重大进步是使用 3D 打印技术快速创建详细原型,从而可以在投入全面生产之前快速进行设计迭代和验证。这加快了开发周期并降低了与传统原型制作方法相关的成本。此外,智能制造技术(例如支持物联网的传感器和机器学习算法)的集成实现了对成型过程的实时监控和分析。这些技术提供了对工艺参数的宝贵见解,有助于立即进行调整以提高零件质量的一致性。此外,开发具有增强性能的新型聚合物材料为设计和应用提供了更大的灵活性,扩大了产品开发创新的可能性。通过利用这些创新,制造商不仅可以改进其设计验证策略,还可以提高塑料注塑成型操作的效率和质量。