在竞争激烈的塑料制造领域,注塑成型中的冷却过程是影响生产质量和速度的关键因素。通过优化此阶段,制造商可以显著提高制造效率和尺寸精度,最终获得卓越的模制部件质量。正确管理冷却可降低生产速度和成本,同时最大限度地减少塑料成型缺陷,例如翘曲和凹痕。本文将深入探讨战略性冷却工艺增强如何实现卓越,将注塑成型操作转变为创新和可靠的典范。
提高制造效率
冷却过程的作用
注塑成型中的冷却过程对于提高制造效率至关重要。通过精确管理此阶段,制造商可以显著缩短循环时间,使塑料快速凝固。这种效率减少了总体生产时间和成本。此外,经过优化的冷却过程可确保成型部件达到必要的尺寸精度,这对于在整个生产过程中保持一致的质量至关重要。实现这种精度不仅可以提高制造过程的效率,还可以最大限度地减少塑料成型缺陷的发生。翘曲和凹痕等缺陷通常是由于冷却不均匀或不当造成的,从而导致浪费和生产成本增加。因此,对于旨在提高运营效率、减少浪费和持续提供高质量零件的制造商来说,改进冷却过程至关重要。反过来,这种优化支持更快的生产速度和降低成本,增强市场的整体竞争力。
提高生产速度
优化冷却过程直接影响注塑成型的生产速度。通过减少冷却时间,制造商可以显著增加给定时间内完成的循环次数,从而提高产量。更快的冷却不仅可以加速塑料的凝固,还可以更快地将成型部件从模具中顶出。这种效率确保生产线以最大容量运行,不会出现不必要的延误。此外,保持一致的冷却条件可防止热应力和不一致,从而减慢后续操作的速度。结果是生产过程得到简化,不仅可以提高生产速度,还可以保持成型部件的质量。速度的提高意味着更高的成本效益和更快满足市场需求的能力。在时间至关重要的行业中,优化冷却过程以提高生产速度可为制造商带来巨大的竞争优势。
降低成本的策略
注塑成型的成本降低在很大程度上依赖于优化冷却过程。通过高效冷却将循环时间最小化,制造商可以降低能耗并减少人工成本,从而大幅节省成本。实施先进的冷却技术(如随形冷却通道)可以进一步增强散热效果,减少每个循环所需的时间。此外,这些策略有助于保持一致的质量,从而减少缺陷发生率以及返工或报废的需要。投资高质量的模具材料和设计还可以确保更好的导热性,从而有助于加快冷却速度并延长模具寿命,最终降低维护成本。此外,利用自动化监控和控制冷却过程可以优化资源配置并最大限度地减少人为错误。总的来说,这些策略不仅可以降低成本,还可以提高生产效率和质量,使制造商能够在不影响性能或可靠性的情况下提供具有成本效益的解决方案。
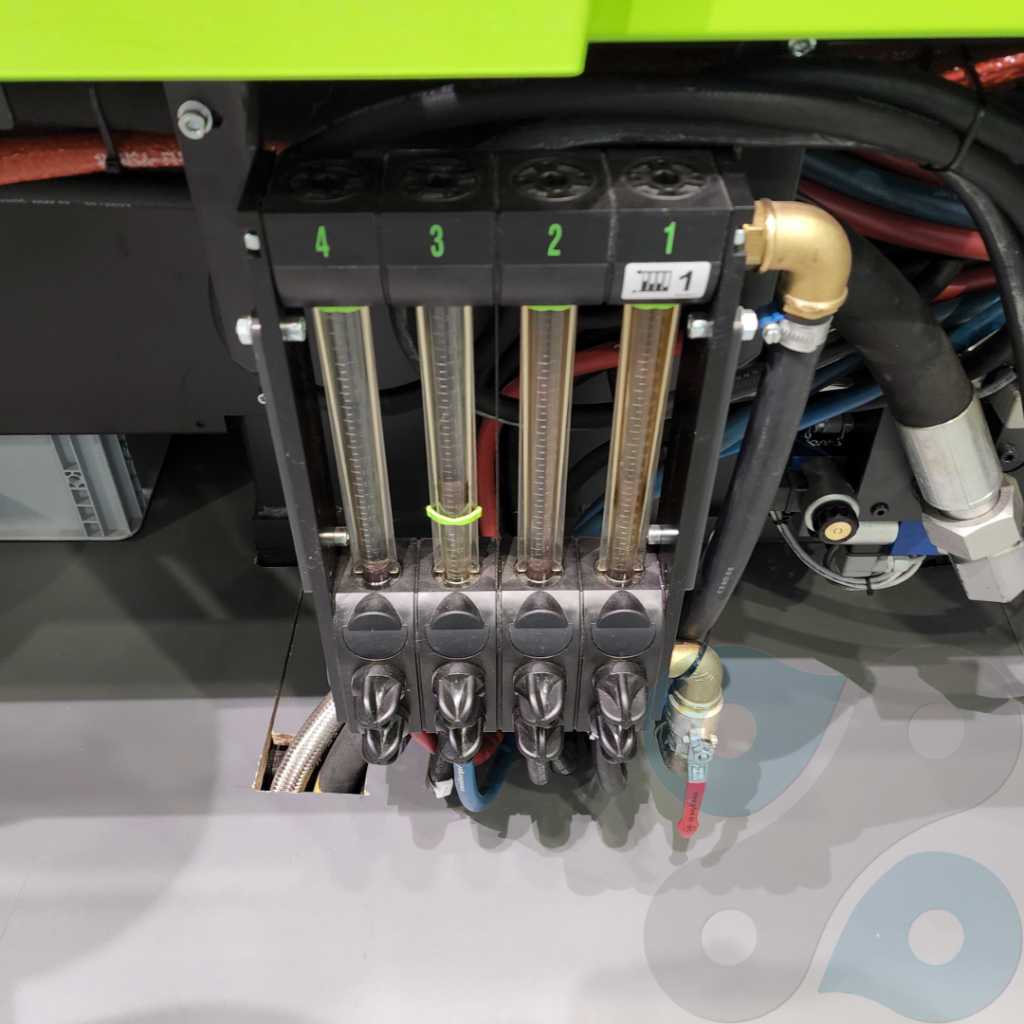
实现尺寸精度
预防塑料成型缺陷
防止塑料成型缺陷对于实现注塑成型的尺寸精度至关重要。一致、受控的冷却是避免翘曲和凹痕等常见缺陷的关键。这些问题通常源于不均匀的冷却,这会导致成型部件不同区域的收缩差异。通过实施精确的冷却策略,制造商可以确保均匀收缩,从而保持部件的预期尺寸。在设计阶段使用先进的模拟工具可以预测潜在的缺陷区域,并允许在冷却过程中进行预先调整。此外,优化模具设计,使壁厚均匀,并策略性地放置冷却通道,可以进一步降低缺陷风险。定期监控和维护设备可确保冷却系统以最佳方式运行,从而降低出现缺陷的可能性。这些主动措施不仅可以提高尺寸精度,还可以提高整体零件质量,减少昂贵的返工需求并提高客户满意度。
确保成型件质量
确保模塑部件的质量与实现注塑成型的尺寸精度有着内在联系。高质量的模塑部件需要精确遵守设计规格,而冷却过程的变化可能会影响设计规格。通过保持均匀的冷却速度,制造商可以避免材料特性不一致,而不一致往往会导致缺陷和尺寸差异。投资先进的模具温度控制系统可以对冷却速度进行微调,确保每个部件都符合其精确的规格。此外,使用实时监控技术可以帮助检测和解决潜在的冷却问题,防止它们影响部件质量。在整个生产过程中进行一致的质量控制检查,可以进一步防止偏离预期结果。通过关注这些方面,制造商不仅可以提高产品的尺寸精度,还可以通过提供符合严格行业标准的可靠、高质量部件来提高整体客户满意度。这种勤勉可以增强信任,并使制造商成为质量保证领域的领导者。
优化冷却阶段
创新冷却技术
采用创新冷却技术对于优化注塑成型中的冷却阶段至关重要。其中一种技术是使用随形冷却通道,这种通道设计为遵循模具轮廓。与传统的直线通道相比,它可以更有效地散热并缩短循环时间。另一种方法是在模具中使用具有优异导热性的先进材料,从而增强散热和冷却效率。此外,使用高压水或气体辅助冷却可以大大缩短冷却时间,从而提高整体生产速度。实施实时监控和自适应控制系统可以通过根据传感器反馈动态调整参数来进一步优化冷却过程。这些创新不仅可以提高冷却效率,还可以提高尺寸精度并降低模制件出现缺陷的风险。通过采用这些尖端技术,制造商可以提高其注塑成型工艺的整体性能和可靠性。
注塑成型的成功案例
注塑成型的成功案例往往凸显了优化冷却阶段带来的变革性影响。例如,一家知名汽车零部件制造商实施了随形冷却通道,缩短了 30% 周期时间,并显著减少了缺陷。这种优化不仅提高了生产速度,还提高了零件的尺寸精度,从而提高了客户满意度和回头客。另一个成功案例是一家采用先进冷却材料和实时监控系统的消费电子公司。这种方法使他们能够实时检测和纠正冷却不一致问题,减少浪费并确保卓越的成型部件质量。这些公司表明,通过采用创新的冷却策略,可以显著提高制造效率和产品质量。这些例子是强有力的证明,激励业内其他公司投资优化冷却工艺,从而在运营中开启新的卓越水平和竞争力。