在不断发展的制造业中,注塑成型中模流分析的精度对于寻求改进生产工艺的行业创新者来说是一个改变游戏规则的因素。模流分析是面向制造设计工艺的一个关键组成部分,它使工程师能够预测熔化的塑料在模腔中的表现,从而确保最佳质量和效率。这种复杂的模拟技术对于识别潜在缺陷、最大限度地减少材料浪费和缩短上市时间至关重要。通过利用先进的模流分析服务,企业可以提高产品性能并获得竞争优势。在这次探索中,我们将深入探讨模流分析的复杂性,强调其重要性及其对制造业的深远影响。
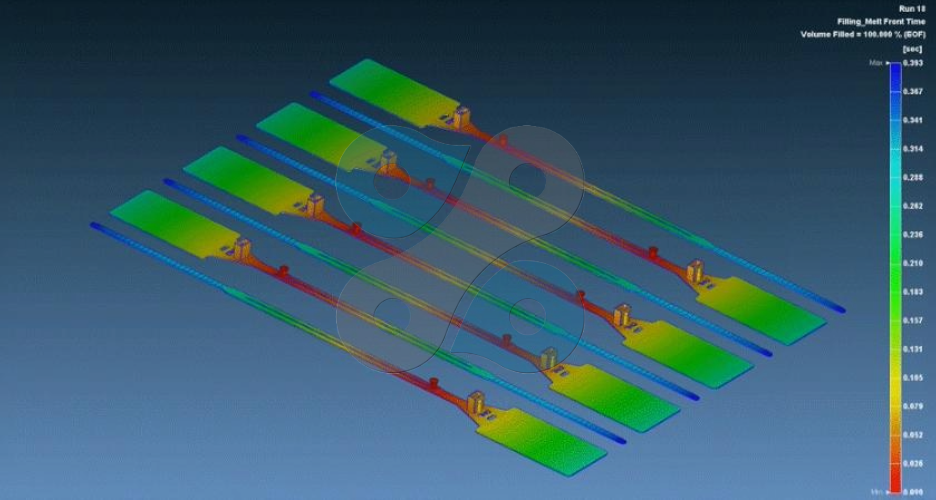
了解 Moldflow 分析
什么是 Moldflow 分析?
Moldflow 分析是一种复杂的模拟过程,用于注塑成型,以预测模具型腔内熔融塑料的行为。该技术利用先进的计算工具来模拟注塑成型过程中塑料材料的流动、冷却和凝固。通过模拟这些动态,工程师可以在实际生产开始之前很久就预测到潜在的问题,例如气穴、焊缝或过度收缩。这种预测能力对于优化模具设计、确保产品质量和提高制造效率至关重要。从模流分析中收集的结果可以指导设计阶段的关键决策,从而进行调整以缩短周期时间、最大限度地减少缺陷并减少材料浪费。利用模流分析服务的企业可以获得洞察力,从而提高产品性能并降低成本,使其成为制造业不可或缺的工具。
注塑成型的重要性
通过提高精度和效率,模流分析在注塑成型过程中起着至关重要的作用。它使制造商能够在生产前直观地看到潜在问题并改进设计,从而减少代价高昂的错误。通过及早发现填充不完整、翘曲或凹痕等问题,公司可以对模具设计或加工条件进行必要的调整。这种预见性不仅有助于提高产品质量,而且可以显著加快产品上市时间。此外,模流分析有助于优化材料使用,从而节省大量成本。在竞争激烈的制造业环境中,这些优势至关重要。利用模流分析服务可确保企业保持高质量标准并保持对市场需求的敏捷响应。因此,对于追求注塑成型创新和卓越的公司来说,模流分析是必不可少的。
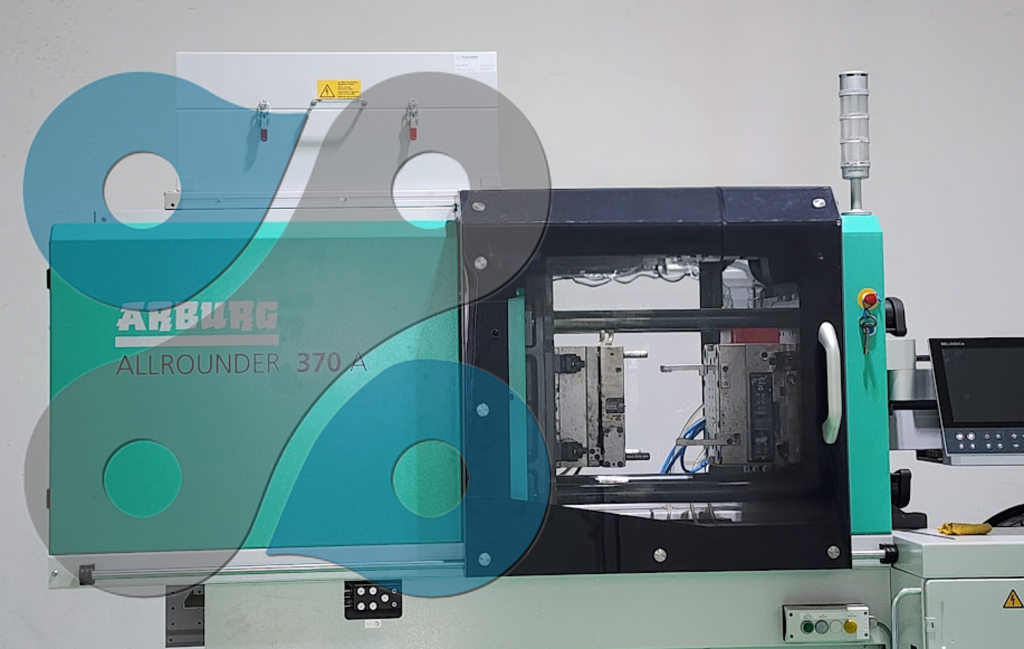
制造商的主要优势
Moldflow 分析为制造商提供了许多好处,可以大大改善他们的生产流程。主要优势之一是能够在潜在缺陷(例如气穴、焊缝和翘曲)发生之前预测和缓解这些缺陷。这种主动方法可以提高产品质量并减少生产延误。此外,模流分析有助于优化模具设计和加工参数,从而缩短周期时间并提高生产效率。
另一个显著的好处是减少材料浪费。通过准确预测熔融塑料的流动和凝固方式,制造商可以微调所用的材料量,从而大幅节省成本。此外,模流分析服务通过简化开发流程和减少对物理原型多次迭代的需求,缩短了产品上市时间。这些好处共同为制造商提供了竞争优势,确保他们能够迅速有效地满足市场需求。
Moldflow 分析的准确性
影响精度的因素
模流分析的精度受多种因素影响,这些因素对于实现注塑成型的准确预测至关重要。其中一个关键因素是输入数据的质量。准确的材料特性(例如粘度、热导率和比热)对于可靠的模拟结果至关重要。此外,模具的几何复杂性和模拟中使用的网格的保真度也会影响精度。更精细的网格通常会提供更详细的结果,但需要更多的计算资源。
另一个重要的考虑因素是工艺参数的完整性。应精确定义注射速度、压力和温度曲线等因素,以反映真实情况。此外,软件功能和进行分析的工程师的专业知识也发挥着重要作用。先进的模流分析服务通常采用尖端软件和熟练的分析师来提高精度。通过仔细管理这些因素,制造商可以确保模流分析提供有价值的见解和改进。
比较 Moldflow 分析服务
在评估模流分析服务时,应考虑几个因素以确保获得最佳结果。首先,评估服务提供商使用的软件工具。支持高级模拟功能的前沿软件通常能产生更准确、更可靠的结果。此外,还要考虑提供商的专业知识和经验,因为熟练的工程师可以通过他们的洞察力和对细节的关注显著提高分析质量。
服务定制是另一个关键方面。不同的项目可能需要根据特定的材料、几何形状或生产目标量身定制的解决方案。提供灵活分析选项的供应商可以更好地满足独特的项目需求。此外,在快节奏的制造环境中,及时交付结果至关重要,因此评估供应商的周转时间至关重要。
最后,考虑整个过程中提供的支持和沟通水平。清晰一致的沟通可以促进更好的协作并确保分析符合您的目标。比较这些方面将有助于选择最符合您的制造需求的服务。
案例研究和真实案例
模流分析在现实场景中的影响是深远的,各行各业的大量案例研究都证明了这一点。例如,一家汽车制造商利用模流分析重新设计了一个容易翘曲的部件。通过模拟不同的模具设计和工艺条件,他们找到了一种解决方案,将缺陷率降低了 30%,显著提高了部件的可靠性和性能。
在消费电子领域,一家公司面临着复杂外壳单元填充不完整的挑战。通过详细的模流分析,他们优化了浇口位置并调整了注射速度,从而缩短了 20% 的生产时间并节省了大量材料。
同样,一家医疗设备制造商使用模流分析服务来改进一个小而复杂的部件。通过分析,他们能够预测潜在的焊接线并相应地调整模具设计,从而增强部件的结构完整性。这些示例突出了模流分析如何在不同的制造环境中推动创新和效率。
在设计过程中集成 Moldflow
增强制造设计
将模流分析集成到面向制造设计 (DFM) 流程中,可以预先解决潜在的生产问题,从而显著提高产品开发效率。通过在设计阶段早期纳入此分析,工程师可以做出明智的决策,从而提高可制造性和产品质量。从模流模拟中获得的见解可用于优化模具设计,例如调整壁厚、修改浇口位置和优化材料流路。
其中一个主要优势是减少昂贵的设计修改。通过在物理原型制作之前识别和解决问题,制造商可以避免耗时且昂贵的调整。此外,模流分析可以探索各种设计替代方案,帮助确定最有效和最具成本效益的解决方案。
这种积极主动的方法不仅缩短了开发周期,而且确保最终产品符合性能和质量标准。因此,在 DFM 流程中集成模流分析可使制造商以更快的速度和更低的成本提供优质产品。
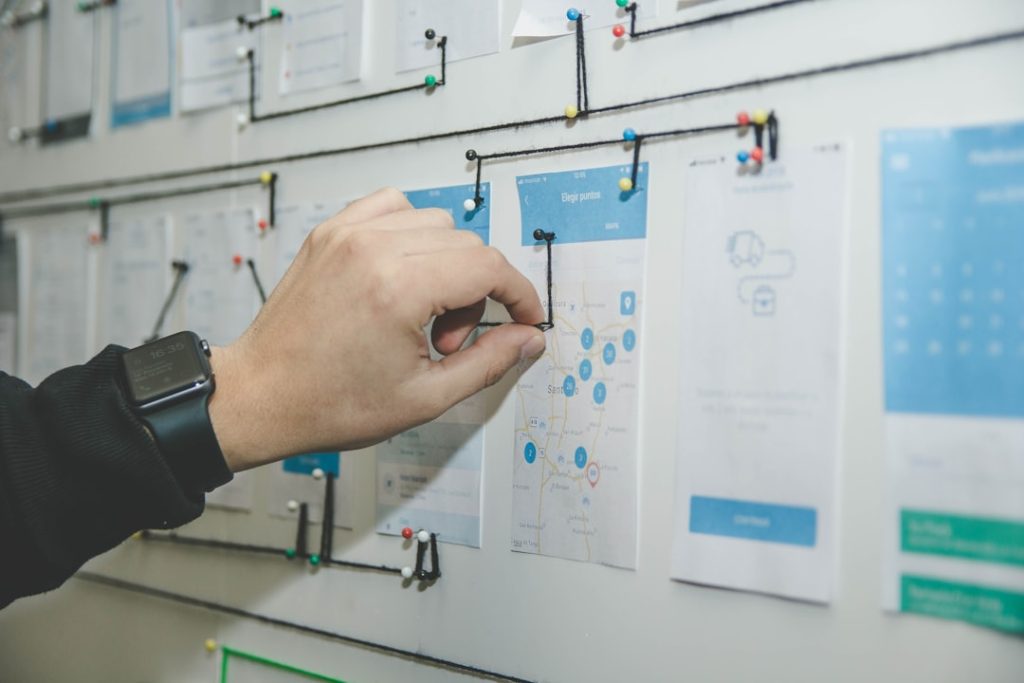