In today’s fast-paced world of manufacturing and product design, the demand for innovative and efficient assembly techniques has never been higher. As companies seek welding alternatives for plastics and strive to reduce reliance on traditional fastening methods, snap fit design emerges as a promising solution. This technique, which involves the interlocking of plastic parts without the need for screws or adhesives, offers numerous advantages including cost-effectiveness, ease of assembly, and flexibility in design. By unlocking the benefits of snap fit assembly, manufacturers and engineers can enhance their production processes and deliver superior products. In this exploration, we will delve into the intricacies of snap fit methods, highlighting their role as a leading plastic assembly alternative and why they should be considered by forward-thinking professionals.
Understanding Snap Fit Assembly
What is Snap Fit Design?
Snap fit design is an innovative technique used in the assembly of plastic parts, allowing them to interlock without any auxiliary fastening devices like screws or adhesives. This method involves creating complementary features on parts, which flex and then lock into place with a snap action. The design includes cantilevers, annular snaps, or torsional snaps that accommodate the necessary flexibility. A key advantage of snap fit design is the simplicity of assembly and disassembly, which significantly reduces production time and cost. Additionally, snap fit methods offer design flexibility, enabling complex shapes and features to be integrated without compromising structural integrity. This makes it an appealing option for manufacturers seeking plastic assembly alternatives. Overall, snap fit design promotes efficient manufacturing processes and product innovation, making it an indispensable tool for engineers and designers aiming to improve product functionality and reduce assembly complexity.
Popular Snap Fit Methods
Snap fit assemblies are characterized by various methods, each tailored to specific requirements and applications. Among the most popular are cantilever snap fits, which are widely used due to their simplicity and effectiveness. These involve a protruding beam that flexes during assembly and snaps into a corresponding recess. Annular snap fits, another common method, are ideal for circular components and involve a ring-shaped protrusion that locks into a groove. U-shaped snap fit is another variation of the cantilever snap fit joint, which can be used to extend the beam length when there is insufficient space. Torsional snap fits utilize twisting motion to secure parts, offering an alternative for assemblies with rotational elements. Each method provides distinct advantages depending on the application, such as ease of assembly, strength, and the ability to withstand repeated disassembly. The selection of a suitable snap fit method depends on factors like material properties, assembly forces, and end-use requirements. By understanding these methods, manufacturers can optimize their designs for efficient, screwless assembly techniques, providing robust welding alternatives for plastics.
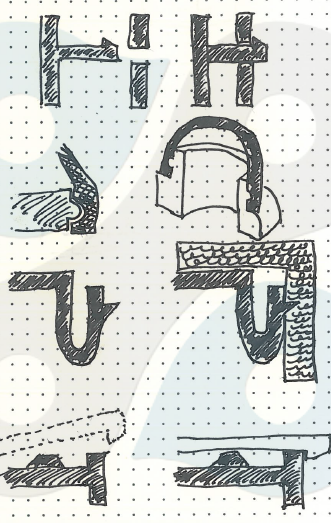
Benefits of Snap Fit Assembly
Snap fit assembly offers several compelling benefits that make it an attractive choice for modern product design. Firstly, it enhances cost-effectiveness by eliminating the need for additional fastening materials such as screws and adhesives. This reduction in material use simplifies inventory management and lowers assembly costs. Secondly, snap fit methods enable faster assembly processes, as parts are simply snapped together, reducing labor time and increasing production efficiency. Additionally, this technique provides remarkable design flexibility, allowing designers to create complex geometries without compromising structural integrity. The ease of assembly and disassembly also supports product maintenance and recycling, aligning with sustainable manufacturing practices. Moreover, the inherent design of snap fits ensures a secure hold, maintaining product reliability over time. By incorporating snap fit design into their workflows, manufacturers can take advantage of these benefits, offering innovative plastic assembly alternatives and improving overall product performance and market competitiveness.
Comparing Assembly Techniques
Plastic Assembly Alternatives
In the realm of plastic assembly, manufacturers are increasingly seeking alternatives to traditional welding and fastening techniques. One prominent alternative is snap fit design, which offers the advantage of joining plastic parts without additional fasteners. This method is not only cost-effective but also simplifies the assembly process. Additionally, ultrasonic welding presents a viable option, particularly for applications requiring airtight seals. This method uses high-frequency vibrations to fuse parts, ensuring durability and strength. Adhesive bonding is another alternative, providing flexibility and ease of application for a variety of plastic materials. However, it may lack the speed and efficiency of other methods. Mechanical fastening, while traditional, remains a reliable choice for assembly, especially when disassembly is a requirement. Each of these assembly techniques has its own set of advantages and limitations, making it crucial for manufacturers to evaluate them based on specific project needs, material properties, and end-use applications.
Welding Alternatives for Plastics
As manufacturers explore welding alternatives for plastics, several methods stand out for their effectiveness and efficiency. Snap fit assembly is a leading technique, eliminating the need for heat or additional materials to join parts. This method not only reduces energy consumption but also simplifies the manufacturing process. Adhesive bonding is another option, offering versatility in bonding different types of plastics. This approach allows for flexibility in design but may require longer curing times. Ultrasonic welding, on the other hand, provides a robust solution for creating strong, permanent bonds. It uses high-frequency vibrations to generate heat and join parts, making it suitable for applications demanding high strength and precision. Mechanical fastening remains a classic choice, allowing for easy disassembly and maintenance. By evaluating these alternatives, manufacturers can select the most appropriate method based on factors like product requirements, material compatibility, and production scalability, ultimately optimizing their plastic assembly processes.
Implementing Snap Fit in Product Design
Designing for Snap Fit Success
Designing for snap fit success requires careful consideration of several critical factors to ensure a functional and efficient assembly. First, material selection is paramount. Engineers must choose plastics with appropriate flexibility and strength, such as polypropylene or nylon, which can withstand repeated assembly and disassembly. Next, attention to detail in geometric design is crucial. Features such as cantilever beams, torsional snaps, and annular rings must be precisely engineered to provide the necessary retention force without causing material fatigue or failure. Additionally, tolerances play a significant role in snap fit design, as they affect the ease of assembly and the durability of the connection. Proper consideration of environmental conditions, like temperature fluctuations and exposure to chemicals, ensures the longevity of the assembly. By focusing on these design aspects, manufacturers can optimize snap fit assembly, resulting in reliable, efficient, and cost-effective plastic assembly alternatives that enhance product performance and lifespan.
Challenges and Solutions in Snap Fit Design
Snap fit design, while advantageous, presents several challenges that designers must address to ensure success. One primary challenge is achieving the right balance between rigidity and flexibility. Parts must be flexible enough to snap into place but rigid enough to maintain structural integrity. This requires careful material selection and precise design of geometries such as beams and hooks. Another challenge is managing stress concentrations, which can lead to material fatigue and part failure. Designers can mitigate this by incorporating fillets and optimizing snap geometry to distribute stress evenly. Additionally, achieving tight tolerances is critical to ensure proper fit and functionality, which can be addressed through advanced manufacturing techniques and thorough prototyping. Environmental factors, such as temperature variations and chemical exposure, can also impact snap fit performance. To counter these, designers should conduct rigorous testing and select materials with appropriate resistance properties. By addressing these challenges, manufacturers can leverage snap fit design effectively, enhancing product reliability and longevity.