In the competitive world of plastic manufacturing, the cooling process in injection moulding stands as a pivotal factor influencing both the quality and speed of production. By optimizing this phase, manufacturers can achieve significant improvements in manufacturing efficiency and dimensional accuracy, ultimately leading to superior molded parts quality. Properly managed cooling reduces production speed and cost, while minimizing plastic molding defects such as warpage and sink marks. This document will delve into how strategic cooling process enhancements can unlock excellence, transforming injection moulding operations into models of innovation and reliability.
Enhancing Manufacturing Efficiency
The Role of Cooling Process
The cooling process in injection moulding is crucial for enhancing manufacturing efficiency. By precisely managing this phase, manufacturers can significantly cut down cycle times, allowing plastic to solidify swiftly. This efficiency reduces the overall production time and costs. Additionally, a well-optimized cooling process ensures that molded parts achieve the necessary dimensional accuracy, which is vital for maintaining consistent quality across production runs. Achieving this accuracy not only improves the efficiency of the manufacturing process but also minimizes the occurrence of plastic molding defects. Defects such as warpage and sink marks are often the result of uneven or improper cooling, leading to waste and increased production costs. Therefore, refining the cooling process is essential for manufacturers aiming to enhance their operational efficiency, reduce waste, and deliver high-quality parts consistently. In turn, this optimization supports faster production speeds and cost reduction, strengthening the overall competitiveness in the market.
Boosting Production Speed
Optimizing the cooling process directly impacts production speed in injection moulding. By reducing cooling times, manufacturers can significantly increase the number of cycles completed within a given period, thus enhancing throughput. Faster cooling not only accelerates the solidification of the plastic but also allows for quicker ejection of molded parts from the molds. This efficiency ensures that production lines operate at maximum capacity without unnecessary delays. Moreover, maintaining consistent cooling conditions prevents thermal stresses and inconsistencies that could slow down subsequent operations. The result is a streamlined production process that not only boosts production speed but also maintains the quality of the molded parts. Such improvements in speed translate to greater cost-efficiency and the ability to meet market demands more swiftly. In an industry where time is a critical factor, optimizing cooling processes to boost production speed offers manufacturers a substantial competitive advantage.
Cost Reduction Strategies
Cost reduction in injection moulding heavily relies on optimizing the cooling process. By minimizing cycle times through efficient cooling, manufacturers can lower energy consumption and reduce labor costs, leading to substantial savings. Implementing advanced cooling techniques such as conformal cooling channels can further enhance heat dissipation, reducing the time required for each cycle. Additionally, these strategies help in maintaining consistent quality, thereby decreasing the incidence of defects and the need for rework or scrap. Investing in high-quality mold materials and design can also ensure better thermal conductivity, which contributes to faster cooling and prolonged mold life, ultimately reducing maintenance costs. Furthermore, leveraging automation in monitoring and controlling the cooling process can optimize resource allocation and minimize human errors. Collectively, these strategies not only reduce costs but also enhance production efficiency and quality, allowing manufacturers to deliver cost-effective solutions without compromising on performance or reliability.
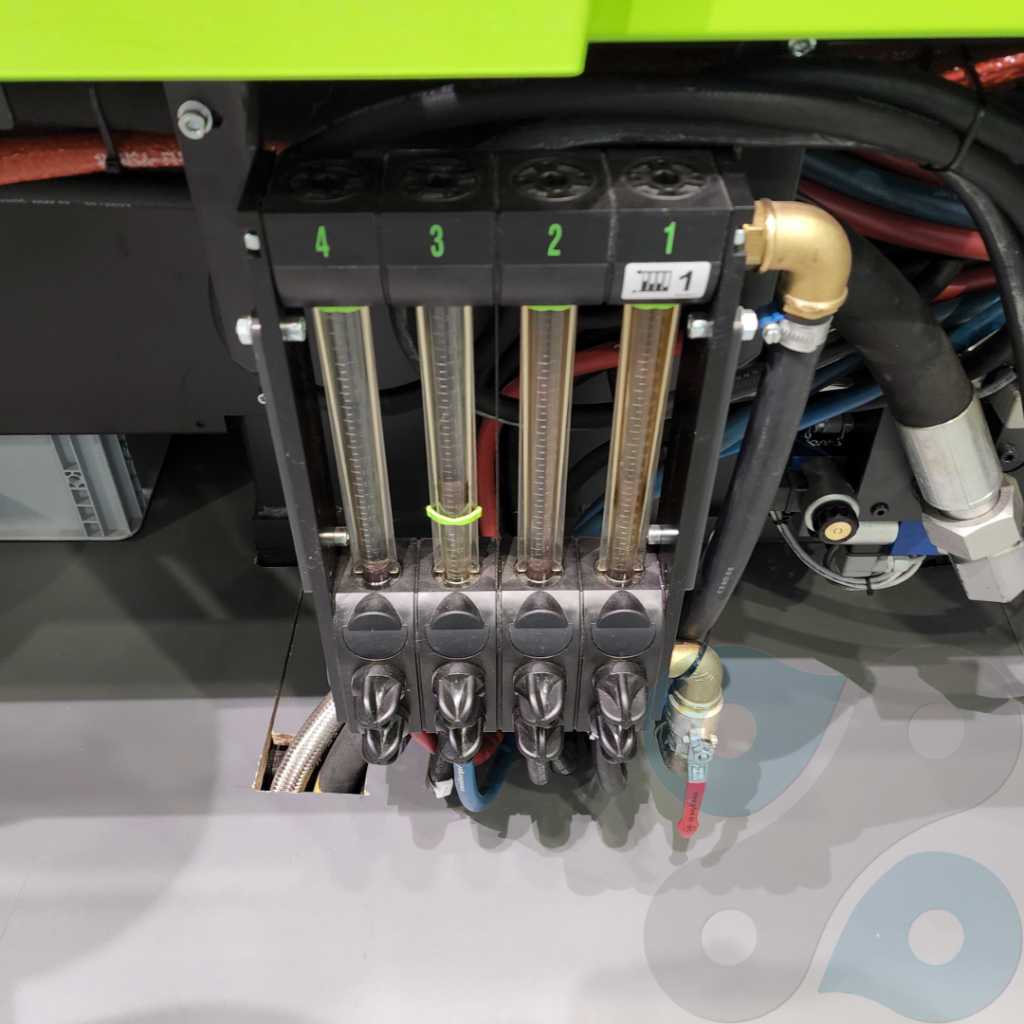
Achieving Dimensional Accuracy
Preventing Plastic Molding Defects
Preventing plastic molding defects is essential for achieving dimensional accuracy in injection moulding. Consistent, controlled cooling is key to avoiding common defects such as warpage and sink marks. These issues often arise from uneven cooling, which leads to differential shrinkage in different areas of the molded part. By implementing precise cooling strategies, manufacturers can ensure uniform shrinkage, thereby maintaining the part’s intended dimensions. Utilizing advanced simulation tools during the design phase can predict potential defect areas and allow for preemptive adjustments in the cooling process. Additionally, optimizing mold design with uniform wall thickness and strategically placed cooling channels can further mitigate the risk of defects. Regular monitoring and maintenance of equipment ensure that cooling systems function optimally, reducing the likelihood of defects. These proactive measures not only enhance dimensional accuracy but also improve overall part quality, reducing the need for costly rework and increasing customer satisfaction.
Ensuring Molded Parts Quality
Ensuring the quality of molded parts is intrinsically tied to achieving dimensional accuracy in injection moulding. High-quality molded parts require precise adherence to design specifications, which can be compromised by variations in the cooling process. By maintaining a uniform cooling rate, manufacturers can prevent inconsistencies in material properties that often lead to defects and dimension discrepancies. Investing in advanced mold temperature control systems allows for fine-tuning of cooling rates, ensuring each part meets its exact specifications. Additionally, using real-time monitoring technology can help detect and address potential cooling issues before they affect part quality. Consistent quality control checks throughout the production process further safeguard against deviations from the desired outcomes. By focusing on these aspects, manufacturers not only enhance the dimensional accuracy of their products but also boost overall customer satisfaction by delivering reliable, high-quality parts that meet stringent industry standards. Such diligence reinforces trust and positions manufacturers as leaders in quality assurance.
Optimizing the Cooling Phase
Innovative Cooling Techniques
Incorporating innovative cooling techniques is crucial for optimizing the cooling phase in injection moulding. One such technique is the use of conformal cooling channels, which are designed to follow the contours of the mold. This allows for more efficient heat removal and shorter cycle times compared to traditional straight-line channels. Another approach is the application of advanced materials with superior thermal conductivity for molds, which enhances heat dissipation and cooling efficiency. Additionally, using high-pressure water or gas-assisted cooling can reduce cooling times significantly, increasing overall production speed. Implementing real-time monitoring and adaptive control systems can further optimize the cooling process by adjusting parameters dynamically based on sensor feedback. These innovations not only improve cooling efficiency but also contribute to better dimensional accuracy and reduced risk of defects in molded parts. By embracing these cutting-edge techniques, manufacturers can enhance the overall performance and reliability of their injection moulding processes.
Success Stories in Injection Moulding
Success stories in injection moulding often highlight the transformative impact of optimized cooling phases. For instance, a prominent automotive parts manufacturer implemented conformal cooling channels, resulting in a 30% reduction in cycle times and a significant decrease in defects. This optimization not only enhanced production speed but also improved the dimensional accuracy of parts, leading to increased customer satisfaction and repeat business. Another success story involves a consumer electronics company that adopted advanced cooling materials and real-time monitoring systems. This approach allowed them to detect and correct cooling inconsistencies on the fly, reducing waste and ensuring superior molded parts quality. These companies demonstrate that by embracing innovative cooling strategies, significant improvements in manufacturing efficiency and product quality are achievable. Such examples serve as powerful testimonials, inspiring others in the industry to invest in optimizing their cooling processes, thereby unlocking new levels of excellence and competitiveness in their operations.