Understanding the intricacies of a 100K cleanroom is essential for engineers and manufacturers seeking to optimize their production processes in industries such as medical devices which requires cleanroom manufacturing. A 100K clean room, defined under ISO standards as a controlled environment, meticulously regulates contamination levels to maintain air purity and ensure product integrity.
This article will delve into the nuances of cleanroom construction and design, highlighting the latest advancements in cleanroom technology. By exploring various types of clean rooms and their applications, industry professionals can gain valuable insights into how these specialized spaces can enhance operational efficiency and compliance.
Introduction to 100K Cleanrooms
What Defines a 100K Cleanroom?
A 100K clean room, also known as a Class 100,000 clean room, is a controlled environment where the concentration of airborne particles is maintained at a specific level. According to ISO standards, this type of clean room allows no more than 100,000 particles larger than 0.5 microns per cubic foot of air. Such precision in air purity is critical for industries like medical devices manufacturing, where even minuscule contaminants can compromise product quality.
The construction of a 100K clean room involves advanced cleanroom technology, including sophisticated HVAC systems and HEPA filters, to regulate airflow and filter out particulate matter. Cleanroom design also plays a crucial role, with materials chosen for their durability and non-corrosive properties, ensuring both longevity and a contamination-free environment. Understanding these specifics is vital for engineers and manufacturers aiming to optimize their cleanroom operations.
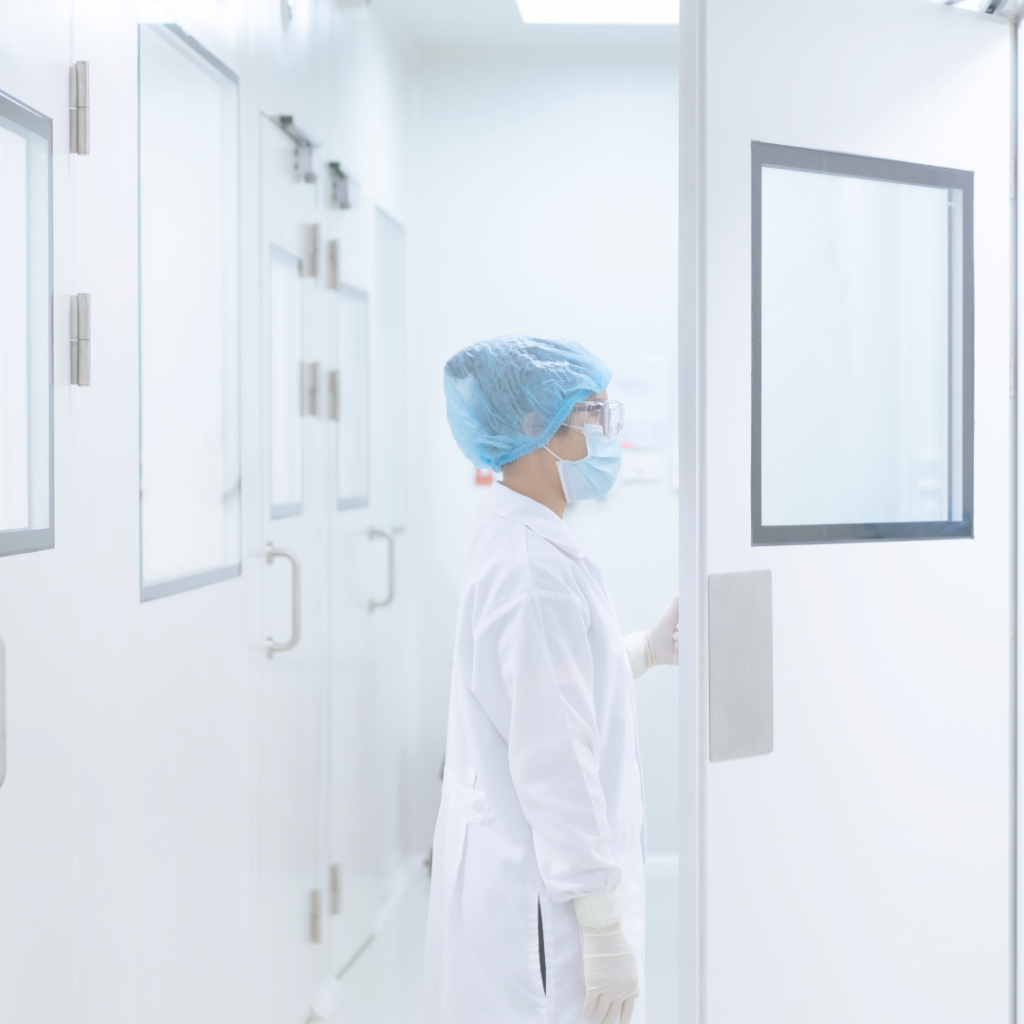
Importance of Cleanroom Technology for Manufacturing
Cleanroom technology is pivotal in maintaining the stringent contamination controls required in a 100K clean room. This technology ensures the stability of the controlled environment by regulating air quality, pressure, temperature, and humidity. High-efficiency particulate air (HEPA) filters are integral to this system, capturing microscopic particles and preventing them from compromising the cleanroom standard. The importance of such technology extends beyond contamination control; it also enhances operational efficiency by minimizing downtime caused by potential contamination-related failures.
Moreover, advanced monitoring systems are employed to provide real-time data on environmental conditions, allowing for immediate corrective actions if deviations occur. This ensures compliance with ISO standards and supports the production of high-quality products. For engineers and manufacturers, investing in cutting-edge cleanroom technology is not just a compliance measure but a strategic enhancement to their production capabilities, safeguarding product integrity and fostering trust with stakeholders.
Cleanroom Construction and Design
Key Elements of Cleanroom Construction
Cleanroom construction requires meticulous attention to detail to achieve the desired level of environmental control. Key elements include the use of corrosion-free materials, such as extruded aluminum, which offer structural integrity and durability. This choice of materials ensures longevity and aesthetics with an attractive finish. The cleanroom’s walls, ceilings, and floors are constructed with smooth, non-porous surfaces to prevent particle accumulation and facilitate easy cleaning. Additionally, HVAC systems are engineered to maintain precise temperature, humidity, and pressure conditions, essential for minimizing particulate intrusion. The layout is designed for flexibility, allowing for modifications with minimal disruption to operations.
Assembly is straightforward, enabling quick installation and reconfiguration. Furthermore, cleanroom doors, which are critical for maintaining the controlled environment, are selected based on stringent specifications to prevent contamination breaches. These elements combine to create a cleanroom that meets ISO standards, ensuring a safe and efficient production space for sensitive manufacturing processes.
Advanced Cleanroom Design Techniques
Advanced cleanroom design techniques are critical for achieving superior contamination control and operational efficiency. One such technique involves modular cleanroom systems, which provide flexibility in layout and are easily reconfigurable to adapt to changing needs. These systems support scalability and reduce downtime during modifications. Additionally, using seamless and flush surfaces in ceilings and walls minimizes particle traps, ensuring easier cleaning and maintenance. Integrated lighting systems, like LED fixtures, are employed not only for energy efficiency but also to minimize heat generation, thus aiding in maintaining temperature stability. Furthermore, optimizing airflow patterns, such as using laminar airflow systems, ensures a unidirectional flow that effectively sweeps particles away from critical areas.
The incorporation of real-time environmental monitoring systems enables continuous oversight of conditions like particle count, temperature, and humidity. These advanced techniques, when combined, enhance the cleanroom’s capability to meet and exceed ISO standards, supporting high-quality production environments in industries requiring stringent contamination controls.
Industry Applications and Standards
Role of ISO Standards in Cleanrooms
ISO standards play a crucial role in the design and operation of cleanrooms, establishing the criteria for air cleanliness by specifying allowable particle concentrations. These standards, such as ISO 14644, provide a uniform framework for classifying clean environments, ensuring consistency across global industries. By adhering to ISO standards, engineers and manufacturers can guarantee that their cleanrooms meet the necessary air purity levels required for their specific applications. This adherence not only aids in compliance but also enhances product safety and quality, which is especially critical in sectors like pharmaceuticals and semiconductor manufacturing.
Furthermore, ISO standards guide the construction and maintenance of cleanrooms, recommending best practices for filtration, airflow management, and environmental monitoring. Implementing these standards facilitates easier validation and certification processes while fostering trust among clients and partners. Ultimately, ISO standards serve as the foundation for achieving and maintaining the high levels of cleanliness indispensable for modern manufacturing and research environments.
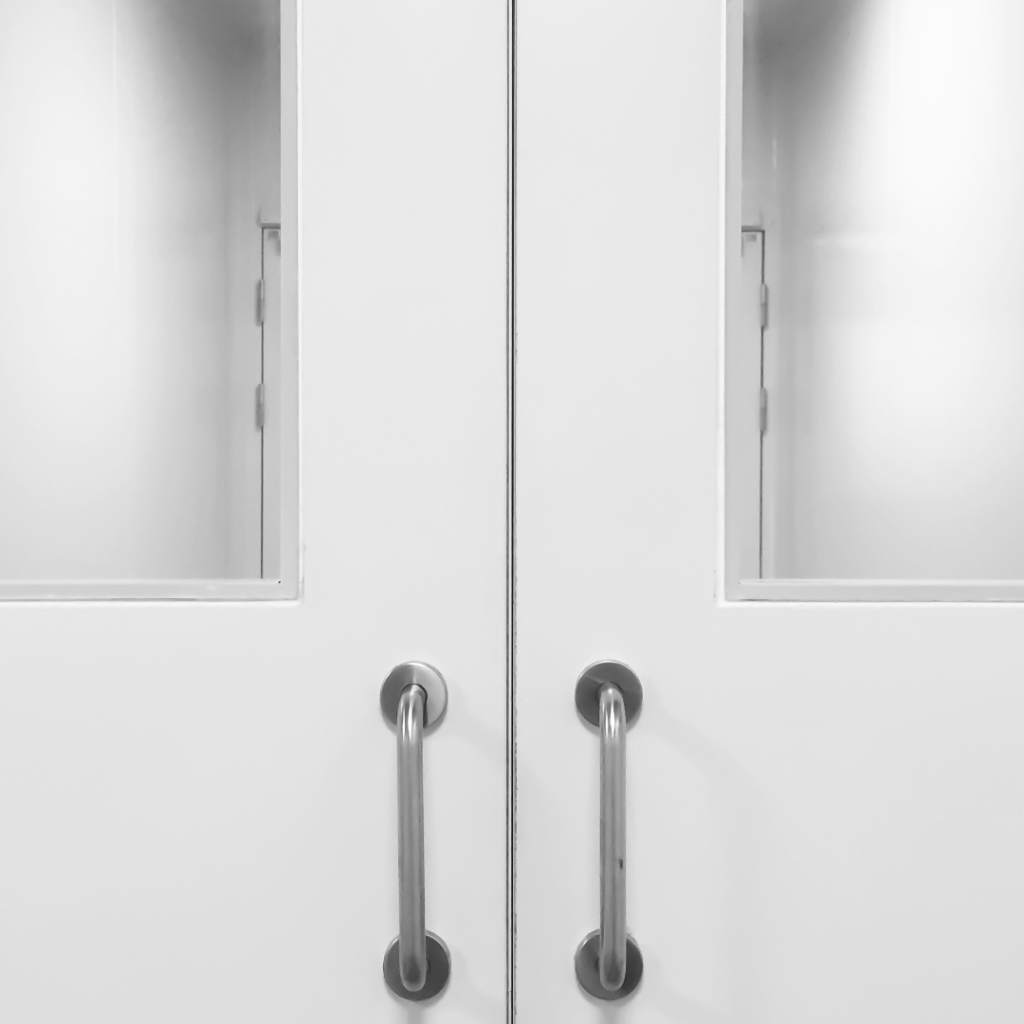
Applications in Controlled Environments: Cleanroom Manufacturing
Controlled environments like 100K clean rooms are indispensable across various industries, ensuring product integrity and safety. In the pharmaceutical sector, these cleanrooms prevent contamination during drug manufacturing, safeguarding product purity and efficacy. Similarly, in semiconductor manufacturing, controlled environments are essential for producing defect-free microchips, as even the tiniest particle can cause significant defects. The medical device industry relies on cleanroom technology to maintain sterile conditions during the assembly of implants and diagnostic equipment, ensuring compliance with stringent health standards.
Additionally, cleanrooms are critical in the medical sectors, where precision and reliability are paramount. By maintaining a controlled environment, manufacturers can mitigate risks associated with contamination, thereby enhancing product quality and performance. The adaptability of cleanroom design allows these controlled environments to be tailored for specific industrial needs, offering versatile solutions that support innovation and operational excellence in high-stakes manufacturing processes.