In the ever-evolving landscape of manufacturing and design, selecting the right prototype techniques for plastic parts is crucial for product owners, engineers, designers, and manufacturers. With a myriad of options available, including 3D printing, CNC machining, prototype tooling for injection moulding, and vacuum casting, it becomes essential to weigh the pros and cons of each method to make informed decisions. This comprehensive guide aims to shed light on the unique advantages and potential drawbacks of these prototyping methods, empowering professionals to choose the most suitable approach for their specific needs. By exploring key aspects such as 3D printing benefits, CNC machining advantages, vacuum casting pros, and the efficiency of injection moulding prototypes, we aim to provide a well-rounded understanding that can drive innovation and success in the industry.
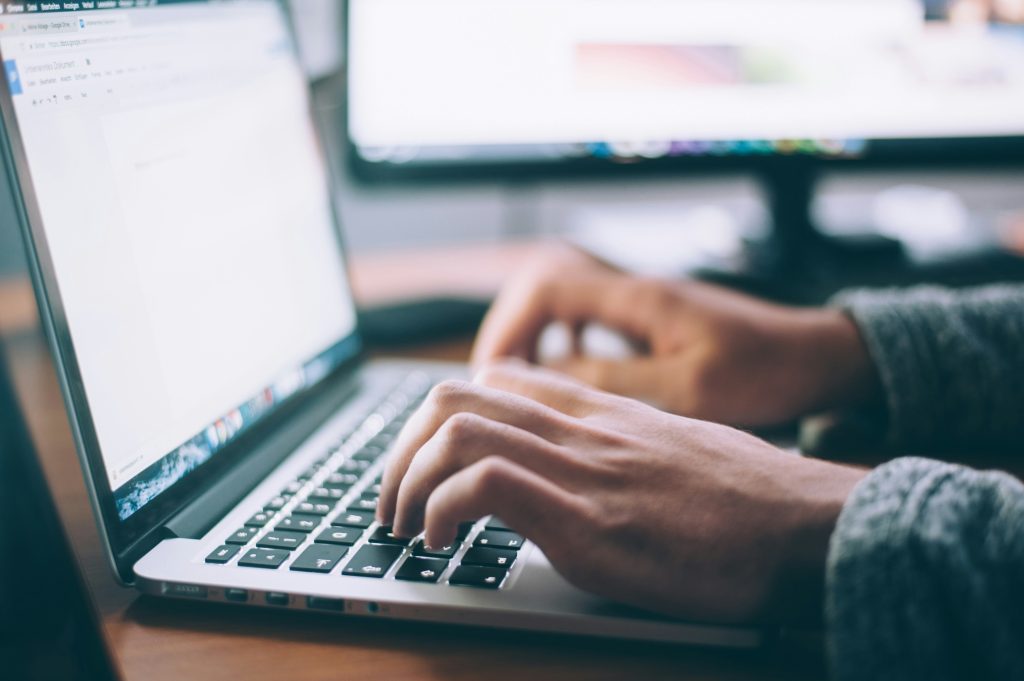
Exploring Prototype Techniques
Understanding 3D Printing Benefits
3D printing, also known as additive manufacturing, offers several benefits that make it a popular choice for prototyping plastic parts. One of the key advantages is its ability to produce complex geometries that traditional manufacturing methods might struggle to achieve. This flexibility allows for rapid iteration and testing of designs, which can significantly speed up the development process. Additionally, 3D printing reduces waste by using only the material necessary to create the part, aligning with sustainable manufacturing practices. The technology also enables on-demand production, minimizing the need for large inventories and reducing lead times. Furthermore, 3D printing enables customization, allowing designers to tailor parts to specific requirements without the need for costly tooling changes. These benefits make 3D printing an attractive option for businesses looking to innovate while keeping costs and environmental impact in check.
Delving Into CNC Machining Advantages
CNC machining stands out as a prototyping technique due to its precision and versatility in producing plastic parts. One of its primary advantages is the ability to achieve tight tolerances and high surface finish quality, which is crucial for applications demanding exact specifications. CNC machining is compatible with a wide range of plastic materials, allowing for the selection of the most suitable material based on the part’s intended use. This method also excels in replicating the look and feel of the final product, providing valuable insights into the design’s functionality and aesthetics. Moreover, CNC machining is highly scalable, making it feasible for both low-volume prototyping and higher-volume production runs. Its speed and efficiency in material removal can significantly shorten lead times. These advantages make CNC machining a reliable choice for industries where precision and material performance are paramount.
Examining Vacuum Casting Pros
Vacuum casting is a prototyping method known for its ability to produce high-quality, detailed plastic parts. One of the major advantages of vacuum casting is its cost-effectiveness, particularly for low to medium volume production. This technique is ideal for creating functional prototypes and small batches of parts with a high level of accuracy and surface finish. It also allows for the use of a variety of materials, including elastomers and rigid plastics, providing flexibility in meeting specific application requirements. Additionally, vacuum casting can replicate fine details and complex geometries from the master model, making it suitable for parts that need to closely mimic the final product. The process is relatively quick, with shorter lead times compared to traditional moulding techniques. These pros make vacuum casting a valuable option for businesses looking to produce high-fidelity prototypes efficiently and economically.
Injection Moulding Prototype Insights
Injection moulding is a widely used technique for creating plastic prototypes, particularly when the end goal is mass production. One of its main advantages is the ability to produce parts with consistent quality and precision. This is vital for ensuring that the prototype closely represents the final product in terms of dimensions and functionality. The process also supports a wide range of plastic materials, allowing engineers to test different material properties before finalizing the production design. Despite its higher initial setup costs due to tooling, injection moulding becomes more cost-effective as production volumes increase. This scalability makes it an attractive option for manufacturers planning to transition from prototyping to full-scale production. Additionally, injection moulding can produce complex shapes with intricate details, providing design flexibility. These insights highlight why injection moulding remains a critical technique in the prototyping phase for many industries aiming for high-quality, replicable plastic parts.
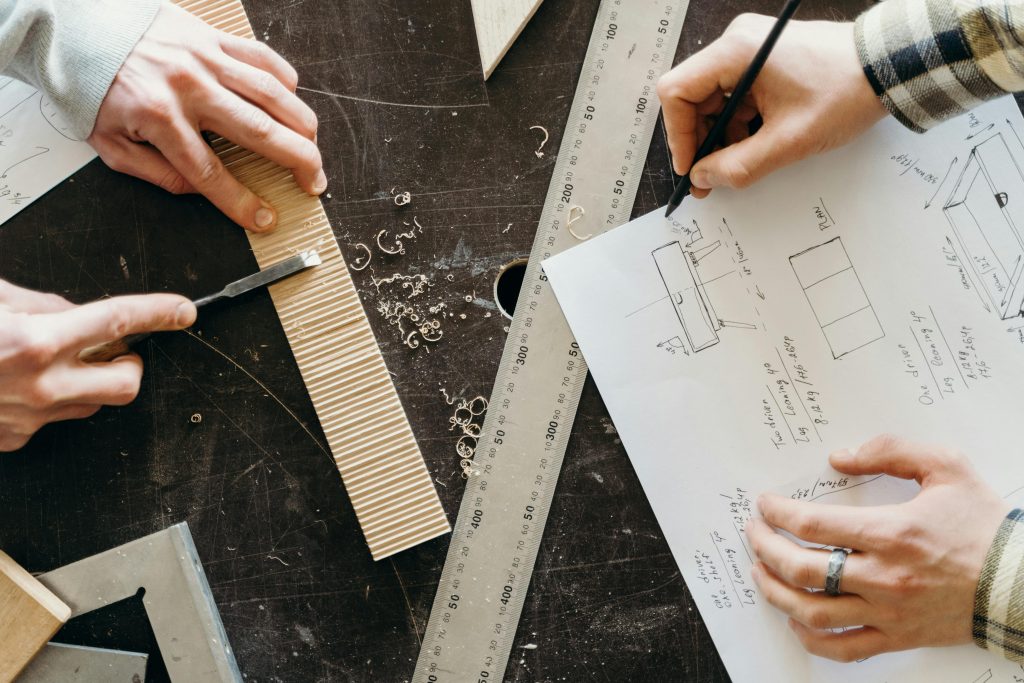
Choosing the Right Technique
Factors to Consider for Product Owners
When selecting the appropriate prototype technique for plastic parts, product owners must evaluate several critical factors. First, the intended production volume plays a significant role. For low-volume needs, techniques like vacuum casting or 3D printing might be more cost-effective, while injection moulding is ideal for high-volume production. Material selection is another crucial consideration, as different techniques offer varying compatibility with plastics, impacting the prototype’s performance and durability. The complexity of the design is also essential; methods like 3D printing excel in producing intricate geometries, whereas CNC machining is suited for parts requiring high precision. Budget constraints and project timelines should influence the choice as well, with some techniques offering faster turnaround times but at a higher cost. By carefully weighing these factors, product owners can make informed decisions that align with their project goals, ensuring the chosen prototyping method supports both innovation and practicality.
Comparing Injection Moulding and Other Techniques
Injection moulding is often compared with other prototyping techniques such as 3D printing, CNC machining, and vacuum casting due to its distinct characteristics. One of the key differences lies in production scalability—while injection moulding is more economical for large-scale production, 3D printing and vacuum casting are more suitable for limited runs due to lower setup costs. CNC machining, on the other hand, offers unparalleled material precision and surface finish, making it ideal for prototypes needing exact specifications. In terms of material versatility, injection moulding supports a wide range of thermoplastics, whereas 3D printing may be limited to specific types. Each method has unique lead times; 3D printing and CNC machining typically offer quicker turnarounds compared to the initial setup time required for injection moulding. By understanding these distinctions, product owners can better align their prototyping strategies with project demands, balancing factors like volume, material, complexity, and cost.
Tailoring Techniques to Project Needs
Selecting the right prototyping technique is critical to aligning with specific project requirements. Tailoring the approach involves assessing several project-specific factors. First, consider the design complexity and the required precision. Techniques like CNC machining are best suited for high-precision needs, while 3D printing excels in creating complex geometries. Next, evaluate the material characteristics required, as different methods support various types of plastics, impacting durability and functionality. The production timeline is another crucial aspect; for rapid prototyping, 3D printing might be more effective, whereas injection moulding is optimal for projects transitioning to mass production. Cost constraints also play a significant role; understanding the budget can help prioritize techniques that offer the best value for the desired outcome. By analyzing these elements, product owners and engineers can effectively tailor their prototyping strategies, ensuring the chosen technique not only meets the technical demands but also supports the overall project goals efficiently.