In the ever-evolving landscape of product development, achieving perfection is not just an aspiration but a necessity for maintaining competitive advantage. The advent of scientific molding has revolutionized the way manufacturers optimize their molding techniques, leading to enhanced product quality and efficiency in manufacturing processes. By employing precise data-driven methodologies, scientific molding allows for meticulous control over injection molding parameters, ensuring consistency and reducing defects. This approach not only bolsters quality control in manufacturing but also empowers product engineers and business owners to innovate with confidence. As we delve deeper into the intricacies of scientific molding, we will uncover how these advanced techniques can elevate your product development endeavors and solidify your position as an industry leader.
Introduction to Scientific Molding
Defining Scientific Molding
Scientific molding is a disciplined and methodical approach to the injection molding process. Unlike traditional techniques, which may rely on trial and error, scientific molding utilizes detailed data analysis and process control to optimize every aspect of production. This technique involves collecting precise data on variables such as temperature, pressure, and time during the molding process. By analyzing this data, manufacturers can identify the optimal conditions for producing high-quality parts. The key advantage of scientific molding lies in its ability to ensure repeatability and consistency, thereby reducing the likelihood of defects. This makes scientific molding particularly valuable in industries where precision is critical, such as medical devices and automotive components. Ultimately, this approach provides manufacturers with the tools needed to enhance product quality, improve efficiency, and reduce costs, all while maintaining stringent quality control in manufacturing.
Historical Context and Evolution
The roots of scientific molding can be traced back to the mid-20th century when the manufacturing sector began recognizing the limitations of conventional molding techniques. Initially, manufacturers relied heavily on operator skill and subjective judgments to produce molded parts, leading to inconsistent product quality and high defect rates. However, as industries demanded higher precision and reliability, a shift towards a more systematic approach became necessary. By the late 1980s and early 1990s, advancements in technology and a growing emphasis on quality control in manufacturing catalyzed the development of scientific molding. This period marked the integration of statistical analysis and process control into molding techniques, laying the groundwork for the modern practices we see today. Over the decades, scientific molding has evolved with technological advancements, incorporating sophisticated software and instrumentation to further refine the injection molding process. This evolution has enabled manufacturers to consistently achieve enhanced product quality and efficiency in their manufacturing processes.
Importance in Modern Manufacturing
In today’s competitive manufacturing landscape, scientific molding has become indispensable. Its importance is underscored by the demand for products that meet the highest standards of quality and precision. By adopting scientific molding techniques, manufacturers can significantly enhance product quality, ensuring that each part meets exact specifications and customer expectations. This precision reduces waste and rework, translating to cost savings and increased efficiency. Furthermore, scientific molding plays a crucial role in quality control in manufacturing by providing a framework for detecting and addressing potential defects early in the production cycle. It empowers product engineers to innovate confidently, knowing that their designs will be executed with accuracy. As industries such as healthcare and automotive continue to demand higher standards, the role of scientific molding in ensuring reliable and consistent manufacturing processes will only grow. Embracing these techniques allows businesses to maintain a competitive edge and respond effectively to the evolving needs of the market.
Benefits of Advanced Molding Techniques
Enhanced Product Quality
Advanced molding techniques, particularly scientific molding, are pivotal in achieving enhanced product quality. By leveraging precise data collection and analysis, these techniques allow manufacturers to fine-tune the injection molding process with exceptional accuracy. This ensures that every product meets the highest standards of quality and consistency. One of the primary benefits is the reduction of defects and variability in production, leading to parts that consistently conform to exact specifications. This is especially crucial in industries where precision is non-negotiable, such as medical devices and aerospace. Furthermore, the enhanced control over variables such as temperature and pressure during molding results in stronger and more reliable products. By adopting advanced molding techniques, businesses can not only improve their product quality but also bolster their reputation for reliability and innovation. This competitive advantage is essential for manufacturers aiming to lead in their respective markets and cater to increasingly demanding customer requirements.
Quality Control in Manufacturing
Quality control in manufacturing is significantly strengthened by the adoption of advanced molding techniques like scientific molding. These techniques provide a systematic approach to monitoring and controlling the molding process, ensuring that every step is optimized for consistency and precision. By utilizing real-time data and statistical analysis, manufacturers can identify and rectify potential issues before they result in defects. This preemptive capability not only minimizes waste and rework but also enhances the overall reliability of the production line. Additionally, scientific molding allows for the creation of detailed process documentation, which is invaluable for maintaining quality standards and meeting regulatory requirements. This comprehensive quality control framework ensures that products consistently meet customer expectations and industry benchmarks. As a result, businesses can achieve greater operational efficiency, reduce costs associated with poor quality, and enhance their reputation for delivering top-notch products. Ultimately, robust quality control through advanced molding techniques is a key driver of success in modern manufacturing.
Impact on Product Development
Advanced molding techniques, such as scientific molding, have a profound impact on product development. By enabling precise control over the molding process, these techniques allow product engineers to push the boundaries of innovation and design. This precision in manufacturing ensures that complex and intricate designs are feasible, opening up new possibilities in product development. Moreover, the data-driven approach of scientific molding reduces the time and cost associated with prototyping and testing, as it provides accurate predictions of how a design will perform once manufactured. This accelerates the development cycle, allowing products to reach the market faster without compromising on quality. Additionally, advanced molding techniques ensure that product modifications and iterations can be implemented seamlessly, facilitating a more agile response to market demands and customer feedback. Ultimately, the integration of advanced molding techniques into the product development process enhances creativity, reduces risks, and ensures that innovative ideas are realized efficiently and effectively.
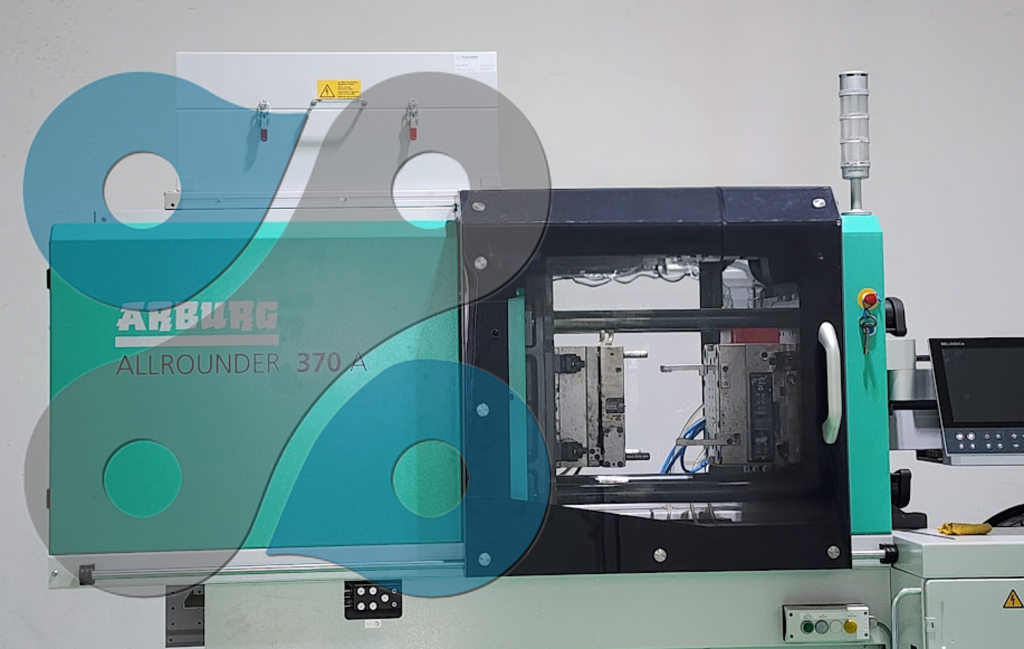
Implementing Scientific Molding in Manufacturing Processes
Steps to Integrate Scientific Molding
Integrating scientific molding into existing manufacturing processes involves several key steps. First, it’s essential to conduct a comprehensive assessment of current production capabilities and identify areas where scientific molding can provide improvements. This may involve analyzing defect rates, cycle times, and material usage. Next, invest in the necessary technology and software that enable precise data collection and process monitoring. Training personnel in these new techniques is also critical, ensuring that staff can effectively operate and interpret the data-driven systems. Collaboration between product engineers, quality control specialists, and machine operators will facilitate a smooth transition. Establishing a pilot project to test and refine the scientific molding process can help address potential challenges and optimize the approach before full-scale implementation. Finally, continuously review and adjust the process based on feedback and results to ensure it meets the desired objectives for enhanced quality and efficiency. By following these steps, manufacturers can successfully integrate scientific molding to elevate their production capabilities.
Best Practices for Injection Molding
Implementing best practices for injection molding is crucial for maximizing the benefits of scientific molding techniques. Start by selecting the right material for your product, considering factors like thermal stability, strength, and compatibility with the molding process. Use detailed mold flow analysis to predict how the material will behave during injection, identifying potential issues before production begins. Optimize mold design to ensure efficient cooling and even pressure distribution, which are critical for reducing cycle times and improving part quality. Establish precise control over processing parameters such as temperature, pressure, and injection speed, using real-time monitoring to adjust them as needed. Regular maintenance of equipment and molds is essential to prevent defects and ensure consistent performance. Additionally, document every step of the process to create a comprehensive knowledge base that can be used for continuous improvement. By adhering to these best practices, manufacturers can enhance product quality, reduce waste, and increase overall production efficiency.
Case Studies and Success Stories
Numerous case studies and success stories illustrate the transformative impact of scientific molding in manufacturing processes. For instance, a leading medical device manufacturer adopted scientific molding to refine its production of precision components. By implementing data-driven controls and optimizing their injection molding parameters, the company significantly reduced its defect rate, resulting in improved product reliability. Another example is an automotive parts supplier that faced challenges with inconsistent part quality. Through scientific molding techniques, the supplier enhanced its quality control in manufacturing, achieving more consistent production outcomes and reducing scrap rates by nearly 30%. Additionally, a consumer electronics company leveraged scientific molding to expedite its product development cycle. By accurately predicting the performance of its designs in the molding process, the company brought new products to market faster while maintaining high standards of quality. These success stories underscore the value of scientific molding in enhancing product quality and efficiency across diverse industries.