In the 1990s, the Sony Walkman was more than just a portable cassette player; it was a cultural phenomenon that revolutionized personal music consumption. Introduced in 1979, the Walkman allowed individuals to carry their favorite tunes wherever they went, fostering a sense of personal space in public environments. Its sleek design and superior sound quality set it apart from other devices, making it a must-have accessory for music enthusiasts worldwide.
What made the Sony Walkman a technological marvel was its ability to combine compactness, functionality, and durability in an era when portable audio devices were bulky and inefficient. Its engineering represented a masterclass in miniaturization, as Sony managed to fit a full tape deck, motorized mechanism, and amplification system into a pocket-sized device. The Walkman also featured innovative noise-reduction technologies, such as Dolby NR, which significantly enhanced audio clarity. Advanced mechanical engineering ensured that tapes played smoothly, even during movement, making it ideal for active lifestyles. The integration of high-quality headphones further elevated the listening experience, distinguishing it from competitors. These innovations, combined with Sony’s emphasis on design aesthetics, solidified the Walkman as the benchmark for portable music players in the 1990s.
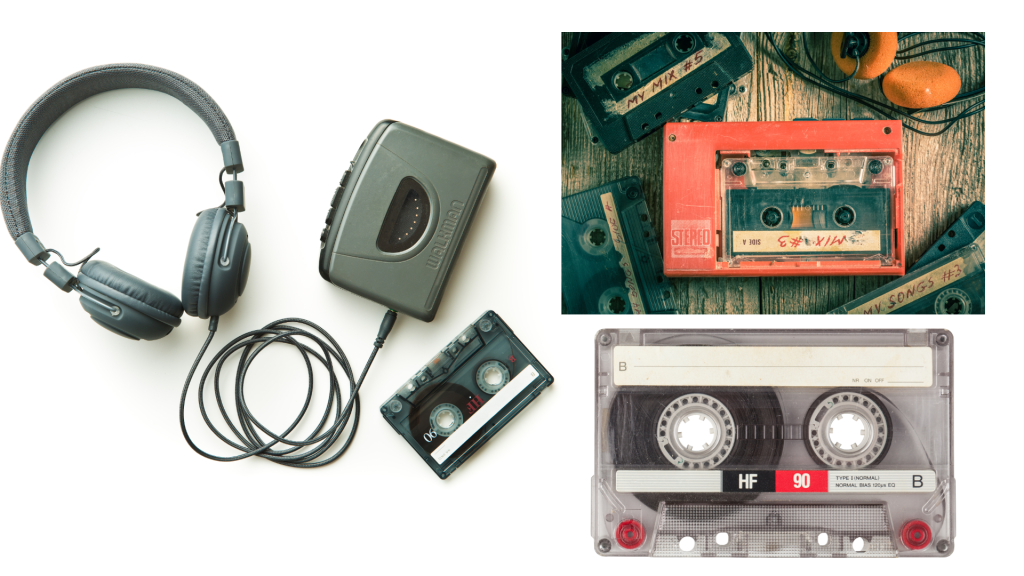
Breaking Down the Sony Walkman: A Technological Marvel
Key Components of the Sony Walkman
The Sony Walkman was a marvel of engineering, meticulously designed to deliver high-quality audio in a compact form factor. A typical Walkman comprised several key components:
- Cassette Mechanism: This included the tape head for reading magnetic signals, capstans, pinch rollers, and a motor to drive the tape.
- Amplifier Circuitry: Responsible for boosting the audio signal from the tape head to a level suitable for headphones.
- Power Supply: Typically powered by AA or AAA batteries, providing portability and convenience.
- Control Buttons: Physical buttons for play, stop, rewind, fast forward, and sometimes additional features like radio tuning.
- Headphone Jack: A standard 3.5mm jack to connect headphones, facilitating private listening.
Processes Involved in Manufacturing Walkman Components
The production of Sony Walkman components required a blend of sophisticated manufacturing techniques tailored to each part. Plastic injection molding was a critical process used to create the durable and lightweight casing that housed the device. This involved melting plastic granules and injecting them into precision-engineered molds to achieve the Walkman’s sleek and ergonomic design. Printed circuit board assembly (PCBA), another key process, required the intricate placement of electronic components onto a board using automated Surface Mount Technology (SMT). The tape mechanism assembly demanded precise manufacturing of mechanical parts like capstans and pinch rollers, often achieved through die-casting and micro-machining. Additionally, metal stamping was employed for smaller internal components, such as brackets and connectors. Each of these processes required stringent quality control to ensure the final product met Sony’s high standards for durability and performance. These sophisticated techniques exemplify the advanced manufacturing capabilities developed in the field of EMS manufacturing in Malaysia.
A Peek Inside: Walkman Teardowns
For those interested in the intricate details of the Walkman’s construction, teardowns provide a fascinating glimpse into its internal architecture. For example, disassembling a Sony Walkman WM-FX10 reveals the careful arrangement of components that contributed to its renowned durability and performance.
Malaysia: A High-Tech Manufacturing Hub
Sony’s Manufacturing Legacy in Malaysia
During the 1990s, Sony expanded its operations to Malaysia, capitalizing on the country’s burgeoning status as a high-tech manufacturing hub. The Penang facility, established in the early 1990s, played a pivotal role in producing various Sony products, including the iconic Walkman. This strategic move streamlined Sony’s production processes and underscored Malaysia’s growing importance in global electronics manufacturing.
The Rise of EMS Manufacturing in Malaysia
Malaysia’s ascent as a leader in electronics manufacturing services (EMS) can be traced back to the 1970s when multinational corporations began setting up operations in the country. By the 1990s, Malaysia had firmly established itself as a key player in the EMS sector, attracting top-tier companies seeking efficient production solutions. This includes many companies focusing on EMS manufacturing in Malaysia.
A Symbiotic Relationship Between MNCs and Local Manufacturers
The presence of industry giants like Sony profoundly impacted local manufacturers. Collaborations and partnerships with these global entities facilitated knowledge transfer, exposing Malaysian firms to cutting-edge technologies and best practices in manufacturing. This relationship enhanced the competencies of local manufacturers, enabling them to meet international standards and compete globally.
Economic Growth and Industrial Diversification
The influx of foreign direct investment, spurred by companies like Sony, significantly contributed to Malaysia’s economic development. It led to job creation, infrastructure development, and the establishment of a robust supply chain network. Over time, Malaysia’s EMS sector diversified, encompassing a wide range of electronic products and components, further solidifying the country’s reputation as a high-tech manufacturing hub.
The Walkman Legacy and Malaysia’s Manufacturing Frontier
The legacy of the Sony Walkman extends beyond its role as a revolutionary personal audio device. Its production in Malaysia symbolizes a transformative period in the country’s industrial history, marking the nation’s emergence as a pivotal player in the global electronics manufacturing arena.
The collaborative efforts between multinational corporations and local manufacturers during this era laid the foundation for Malaysia’s current status as a leader in high-tech and EMS manufacturing in Malaysia.