In the ever-evolving landscape of manufacturing, mold flow analysis has emerged as a pivotal tool for driving innovation and efficiency in the injection molding process.
As a sophisticated simulation technique, mold flow analysis allows manufacturers to predict and optimize the flow of molten material within a mold cavity, ensuring superior product quality and reduced manufacturing costs. By integrating mold flow analysis services into the design for manufacturing process, companies can anticipate potential issues, minimize waste, and enhance production efficiency.
We delve into the intricacies of mold flow analysis, exploring its critical role in modern manufacturing and highlighting its significance in achieving precision and excellence in injection molding.
Importance of Mold Flow Analysis
Enhancing Design for Manufacturing
Mold flow analysis plays a crucial role in enhancing the design for manufacturing (DFM) processes. By simulating the flow of molten material within a mold, manufacturers can identify potential design issues before physical molds are created. This proactive approach allows for adjustments in the design phase, reducing the risk of costly modifications later. Key benefits include:
- Material Optimization: By understanding flow patterns, designers can choose the best materials, minimizing waste and ensuring efficient use.
- Cycle Time Reduction: Predicting the cooling and solidification times can lead to faster production cycles.
- Defect Prevention: Identifying areas prone to defects, such as warping or air entrapment, ensures higher quality outputs.
Thus, integrating mold flow analysis services in DFM not only streamlines production but also bolsters product quality, ensuring competitiveness in the fast-paced manufacturing industry.
Boosting Innovation in Injection Moulding
Mold flow analysis significantly contributes to boosting innovation within the injection molding sector. By leveraging advanced simulation techniques, manufacturers can experiment with new designs and materials without the constraints of traditional trial-and-error methods. This flexibility encourages creativity and accelerates the development of innovative products. Through detailed insights into flow dynamics, mold flow analysis enables:
- Complex Design Exploration: Manufacturers can explore intricate geometries and thin-walled sections previously considered unfeasible.
- Material Experimentation: Testing different material combinations virtually allows for the discovery of novel applications.
- Rapid Prototyping: Shortening the design iteration cycle fosters quicker introduction of new products to market.
By integrating these capabilities, mold flow analysis services empower companies to remain at the forefront of technological advancements.
They can push boundaries, reduce time-to-market, and deliver cutting-edge solutions that meet the evolving demands of consumers and industries alike.
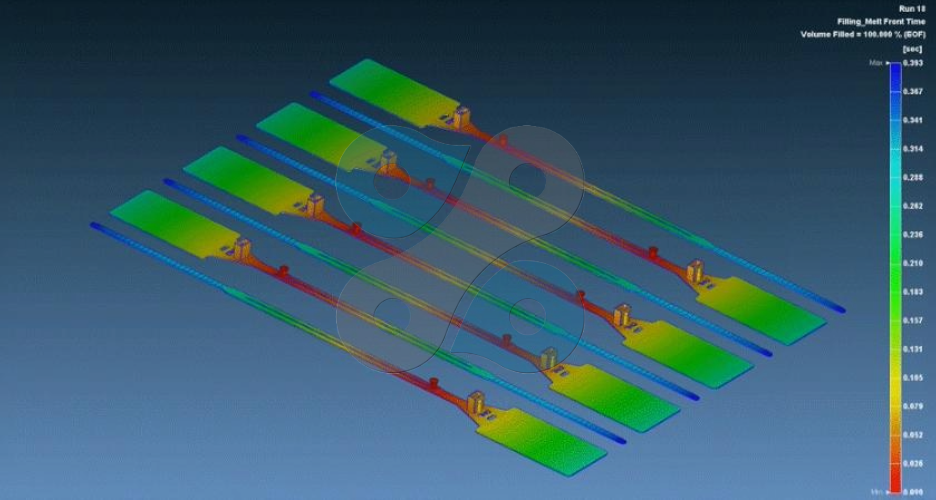
Accuracy of Mold Flow Analysis
Factors Influencing Precision
The precision of mold flow analysis is contingent upon several critical factors that can affect the accuracy of simulation results. Understanding these factors is essential for optimizing the analysis process and ensuring reliable outcomes:
- Material Properties: Accurate data on the material’s thermal and rheological properties is fundamental. Incomplete or incorrect data can lead to flawed predictions.
- Mesh Quality: The granularity and quality of the mesh used in simulations impact the detail and accuracy of the analysis. A finer mesh provides better resolution but at the cost of increased computational resources.
- Boundary Conditions: Setting realistic boundary conditions, such as mold temperature and injection speed, is crucial for obtaining relevant results.
- Software Capabilities: The choice of software, along with its algorithms and updates, also plays a role in the precision of the analysis.
By meticulously considering these factors, manufacturers can enhance the reliability of mold flow analysis, leading to better decision-making and optimized production processes.
Benefits of Accurate Predictions
Accurate predictions in mold flow analysis offer a multitude of benefits, directly impacting the efficiency and quality of the injection molding process. When simulations align closely with real-world outcomes, manufacturers can enjoy several advantages:
- Cost Reduction: Identifying and addressing potential defects and inefficiencies in the design phase minimizes costly rework and material wastage.
- Quality Assurance: Accurate predictions ensure that final products meet stringent quality standards, reducing the likelihood of defects and returns.
- Enhanced Productivity: By optimizing cycle times and mold designs, companies can increase their production volumes without sacrificing quality.
- Informed Decision-Making: Reliable data from precise simulations enable more informed decisions regarding materials, processes, and designs.
These benefits culminate in a more streamlined manufacturing process, fostering competitiveness and innovation. By prioritizing accuracy in mold flow analysis services, companies can achieve significant improvements in operational performance and customer satisfaction.
Mold Flow Analysis Services
Key Offerings and Capabilities
Mold flow analysis services encompass a range of offerings and capabilities designed to enhance the injection molding process. These services leverage advanced simulation software and expert insights to deliver comprehensive solutions for manufacturers:
- Design Optimization: Tailored analysis to refine mold designs, ensuring efficient material flow and minimizing defects.
- Material Selection: Assistance in choosing the most suitable materials based on flow characteristics, mechanical properties, and cost considerations.
- Process Simulation: Detailed simulation of the entire injection molding process, from filling to cooling, to identify potential bottlenecks and areas for improvement.
- Defect Analysis: In-depth examination of potential defect areas such as warpage, air entrapment, and sink marks, with recommendations for mitigation.
- Cycle Time Reduction: Strategies to optimize cycle times, enhancing productivity and reducing manufacturing costs.
These key offerings enable manufacturers to achieve superior product quality, reduced production costs, and accelerated time-to-market. By integrating mold flow analysis services, companies can unlock new levels of efficiency and innovation in their manufacturing processes.
Choosing the Right Service Provider
Selecting the right mold flow analysis service provider is crucial for maximizing the benefits of this advanced simulation technique. Here are key considerations to ensure you make an informed choice:
- Expertise and Experience: Look for providers with a proven track record in mold flow analysis, demonstrating expertise across various industries and projects.
- Software Proficiency: Ensure the provider uses state-of-the-art simulation software and stays updated with the latest technological advancements.
- Comprehensive Services: Opt for providers that offer a full spectrum of services, from design optimization and material selection to defect analysis and process simulation.
- Client References: Request client testimonials or case studies to gauge the provider’s ability to deliver quality results and customer satisfaction.
- Customization and Support: Choose a provider that offers tailored solutions and provides ongoing support to address any issues that arise during implementation.
By carefully evaluating these factors, you can partner with a service provider that not only meets your specific needs but also enhances your overall manufacturing efficiency and innovation capabilities.