Injection Moulding — Overview
Injection moulding, here in Malaysia. Our mechanical engineering expertise takes your idea from concept to reality. We offer industrial design, prototyping, design for manufacturing, design analysis and manufacturing to ensure that your products are aesthetically pleasing, durable and functional. Let us help you worry about the manufacturing.
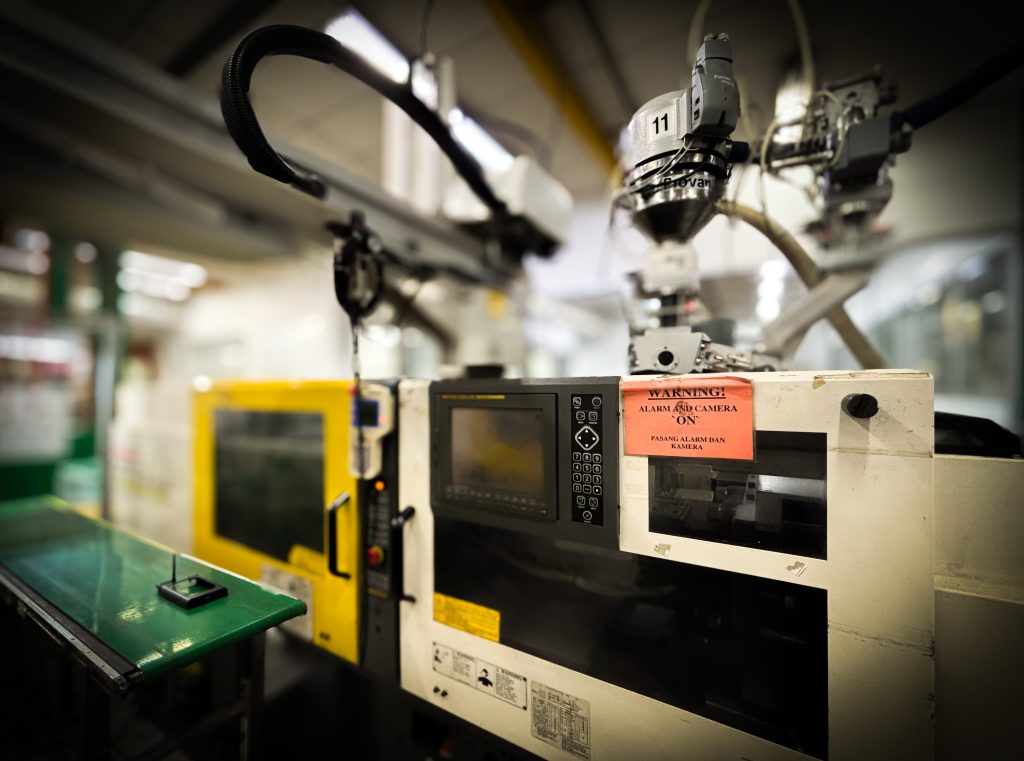
How a good injection moulding partner transforms your manufacturing experience
With meticulous attention to detail and a commitment to excellence, we help you with your injection moulding, simplifying your product development journey
We focus A LOT on the Design for Manufacturing (DFM) phase to ensure that come mass production, the result is as per expectations.
Why?
Because good moulding starts with good tool fabrication. And the results can be simulated with software. The entire moulding process: clamping, injection, cooling, ejection, is scientific in nature.
What do we help you achieve?
Quality. Cavity-to-cavity consistency, shot-to-shot consistency, and run-to-run consistency.
The five critical factors of injection moulding include:
- Part design
- Material selection
- Mould design and fabrication
- Moulding machine
- Moulding process
All the above factors contribute to a successful moulding operation, ensuring high-quality parts, efficiency in production and cost-effectiveness.
Scientific injection moulding is the process of achieving consistency in part quality via the application of the underlying scientific principles that control the parameters of the moulding process.
Key factors of injection moulding include the setup of systems, pressures, temperatures, and the specific timing during the injection cycle.
These elements play vital roles in the overall molding process, influencing factors such as mold design, holding pressure, and melt temperature. Each step in the injection molding journey, from material selection to final part ejection, significantly impacts the quality and efficiency of the molded parts.
Understanding the intricacies of the injection molding process is essential for minimizing defects and ensuring that the final products meet stringent quality standards. By optimizing each stage, manufacturers can enhance production efficiency and achieve maximum output.
Read more about injection moulding on our blog here!
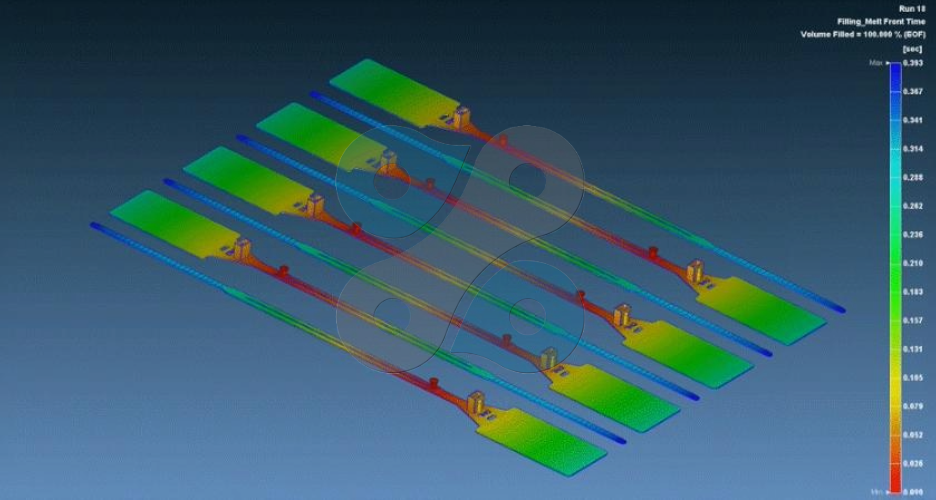
Our comprehensive suite of professional services caters to a diverse clientele, ranging from automotive, medical devices, electronics, new energy management, sporting equipment, internet of things, etc.
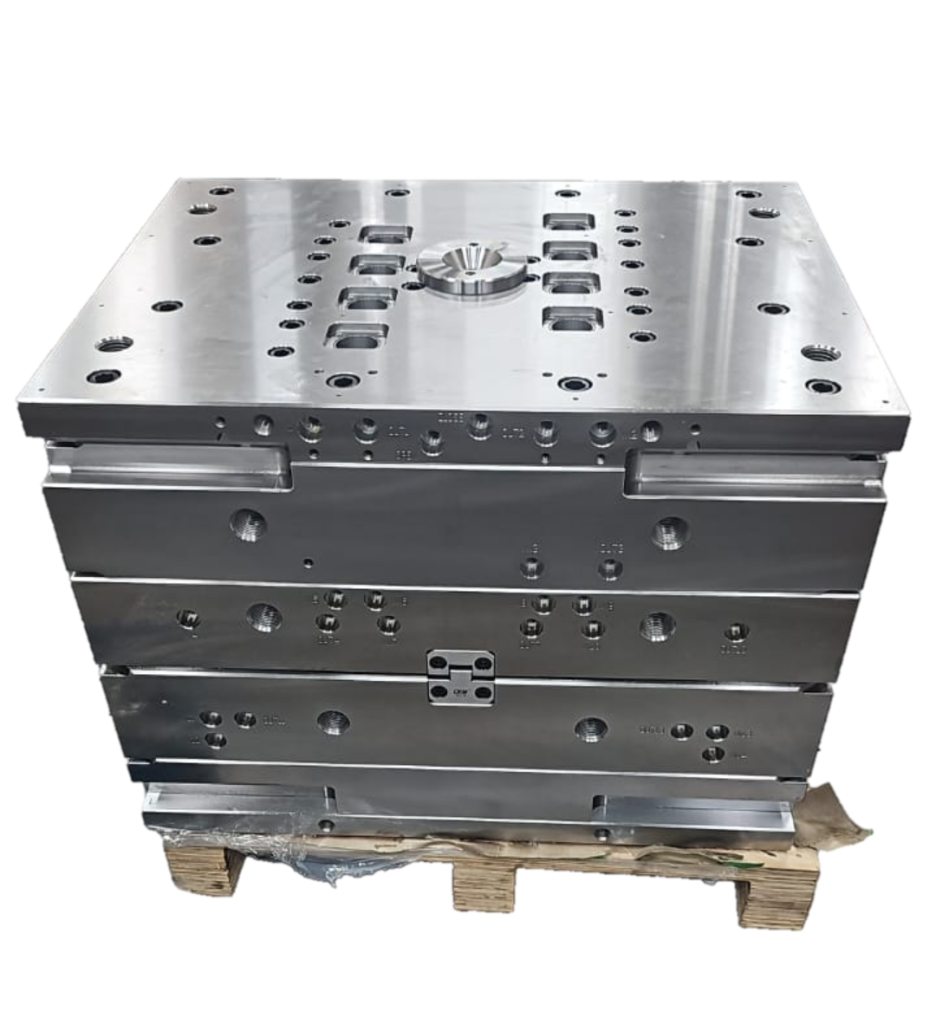