Surface Mount Technology (SMT) has revolutionized electronics manufacturing by enhancing efficiency, enabling miniaturization, and boosting performance, making it an indispensable methodology in the industry. As the demand for high-performance printed circuit boards (PCBs) continues to grow, understanding the nuances of SMT design, assembly processes, and testing methodologies becomes crucial for electronics engineers and manufacturing professionals. This article will delve into the best practices for PCB design for SMT, detailing the assembly techniques that ensure precision and reliability, and exploring the comprehensive testing methodologies that guarantee product quality before market introduction. By mastering these components, industry professionals can confidently navigate the complexities of modern electronics manufacturing, ensuring robust solutions that meet the rigorous standards of contemporary markets.
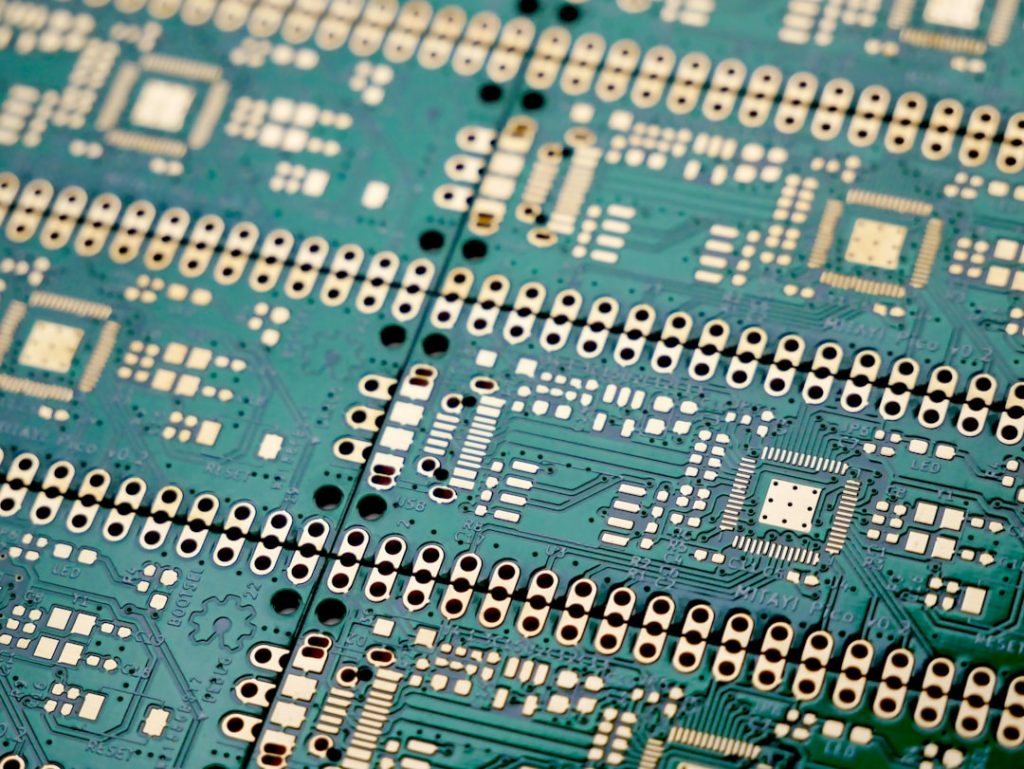
SMT Design Essentials
Key Principles of SMT Design
In the realm of electronics manufacturing, successful Surface Mount Technology (SMT) design hinges on several foundational principles. Firstly, component placement dictates the efficiency and reliability of the final product. Engineers must strategically position components to minimize signal path lengths, reducing potential signal loss and interference. Secondly, pad design is crucial; it must accommodate component leads while ensuring optimal solder joint formation. This requires precise calculation of pad dimensions and spacing. Thirdly, the choice of substrate material can significantly impact thermal management and overall performance. Materials like FR-4 are commonly used, but for high-performance applications, alternatives such as polyimide might be preferred due to their superior thermal properties. Lastly, ensuring manufacturability entails designing with assembly processes in mind, taking into account factors such as the solder paste application and reflow soldering profiles. By adhering to these principles, engineers can optimize PCB design for SMT, achieving enhanced efficiency and reliability in electronics manufacturing.
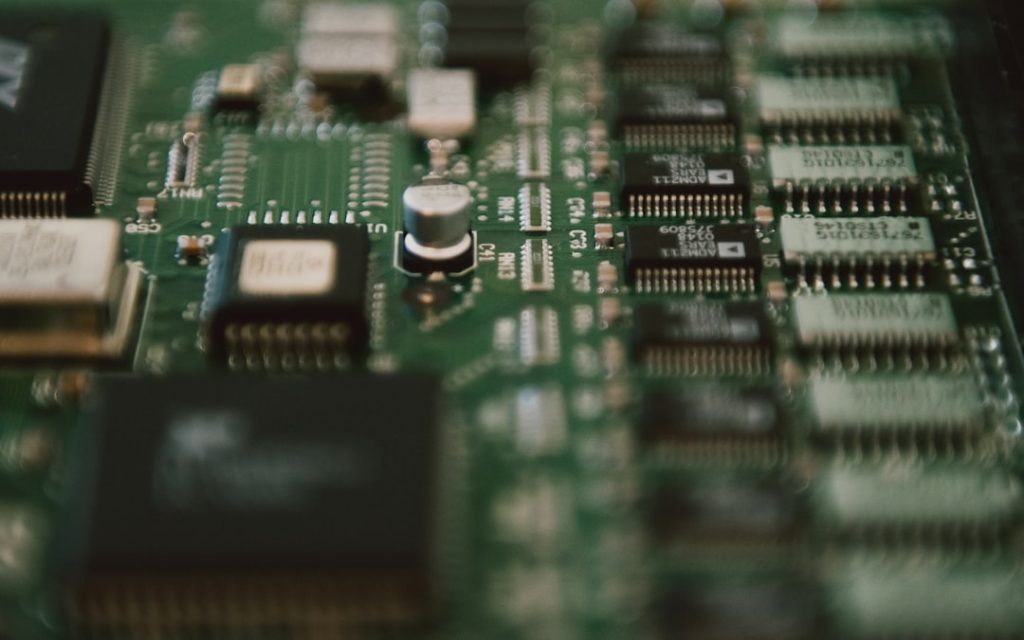
Optimizing PCB Design for SMT
Optimizing PCB design for Surface Mount Technology involves a meticulous approach to layout and component selection. The foremost consideration is minimizing trace lengths, which reduces electrical resistance and improves signal integrity. This practice is especially critical in high-speed applications where even slight delays can affect performance. Additionally, utilizing a grid system for component placement can streamline the assembly process, ensuring consistency and reducing errors. Designers must also pay attention to thermal management; incorporating thermal vias and heat sinks can effectively dissipate heat, preventing damage to sensitive components. Furthermore, design for manufacturability (DFM) principles should guide the selection of components and materials. This includes choosing common package sizes and footprints that align with standard assembly equipment capabilities. Lastly, maintaining clearances and tolerances is essential to prevent shorts and ensure proper functionality. By following these strategies, engineers can enhance the efficiency and reliability of SMT assembly, resulting in superior product quality.
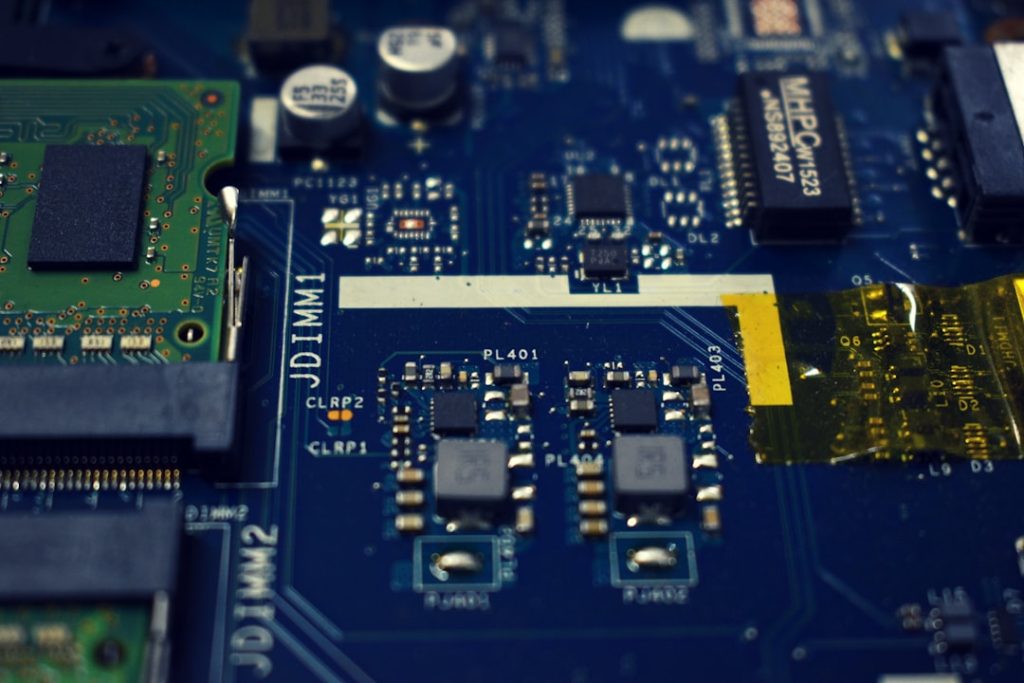
Miniaturization and Efficiency in Electronics
Miniaturization in electronics, driven by Surface Mount Technology, has been pivotal in advancing device capabilities while maintaining efficiency. As components shrink in size, engineers face the challenge of integrating more functionality into smaller footprints without sacrificing performance. This trend demands innovative design strategies, such as utilizing multi-layer PCBs, which offer more routing space and support complex circuitry. Furthermore, smaller components enable higher density designs, reducing the overall size of devices like smartphones and wearables. Efficiency is achieved not just through compact design but also through effective power management; low-power components and efficient power distribution networks are integral to minimizing energy consumption. Additionally, miniaturization fosters enhanced thermal management techniques, essential for dissipating heat in confined spaces. These advancements contribute to the creation of lightweight, portable electronics that meet consumer demands for functionality and convenience. By leveraging the principles of miniaturization and efficiency, electronics manufacturing continues to evolve, delivering cutting-edge solutions.
Best Practices in SMT Assembly
Streamlining the Assembly Process
Streamlining the assembly process in Surface Mount Technology is crucial for improving efficiency and reducing production costs. One effective approach is the implementation of automated assembly lines, which enhance precision and speed. Automated pick-and-place machines can accurately position components on PCBs, significantly minimizing human error. Additionally, integrating optical inspection systems ensures defects are identified and corrected early in the assembly process, reducing rework and scrap rates. Another key practice is optimizing the solder paste application. Consistent and precise deposition of solder paste is vital for forming reliable solder joints, which is achievable through well-maintained stencil printing processes. Moreover, standardizing component packages and sizes across product lines can lead to more efficient assembly by minimizing the need for frequent machine recalibrations. Collaborating closely with suppliers to ensure part quality and availability further supports a smooth assembly process. By adopting these strategies, manufacturers can achieve greater consistency, reliability, and cost-effectiveness in SMT assembly.
Ensuring Accuracy and Reliability
Ensuring accuracy and reliability in SMT assembly is paramount to achieving high-quality electronics. Precision in component placement is a critical factor, as even slight misalignments can lead to circuit malfunctions. Automated optical inspection (AOI) systems are essential tools that verify component positioning and detect solder bridge defects, ensuring only flawless assemblies proceed to the next stage. Additionally, the use of controlled reflow soldering processes helps maintain consistent solder joint quality. By carefully monitoring temperature profiles, manufacturers can prevent common issues such as overheating or cold solder joints, which compromise reliability. Another aspect is maintaining stringent quality control protocols. Regular calibration of assembly equipment and adherence to industry standards like IPC-A-610 can significantly enhance product consistency. Lastly, fostering a culture of continuous improvement through employee training and feedback loops ensures teams remain adept at identifying and resolving assembly issues promptly. These practices collectively contribute to the production of durable, high-performance electronic products.
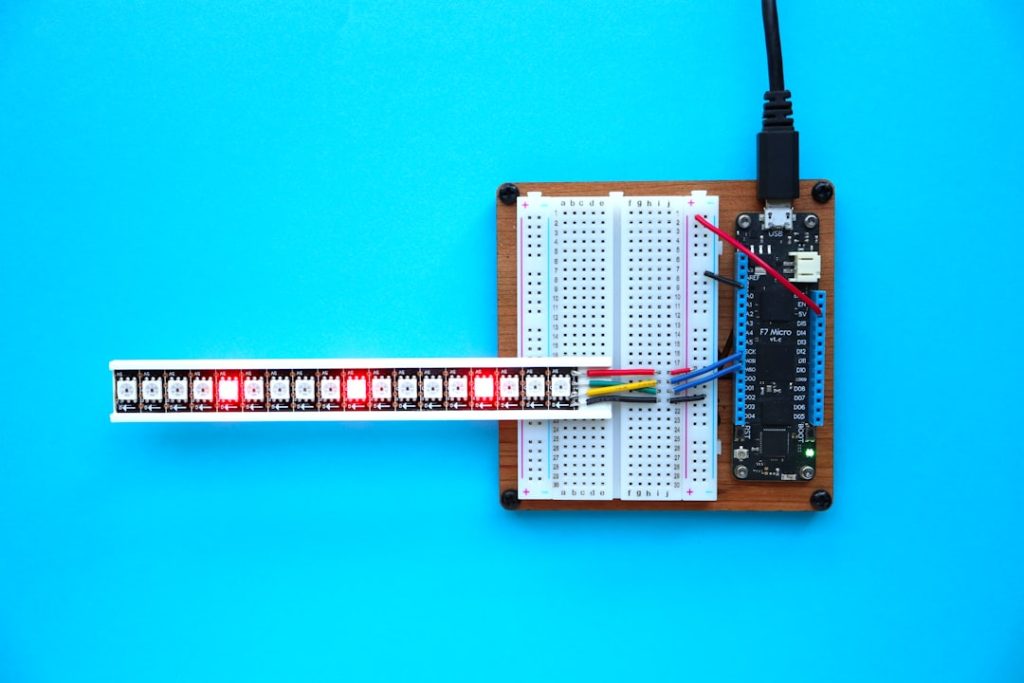
Critical SMT Testing Methodologies
Testing for Product Quality and Functionality
Testing for product quality and functionality is a critical phase in electronics manufacturing, ensuring that only the best products reach the market. Various testing methodologies are employed to validate both the performance and reliability of SMT assemblies. Functional testing is one such methodology where the finished product is evaluated under real-world conditions to verify its operation and performance. This includes checking for correct electrical characteristics and ensuring that all features work as intended. In-circuit testing (ICT) is another vital technique, focusing on individual components and connections on the PCB. ICT detects issues like open circuits and short circuits, which can prevent functional failures. Moreover, environmental testing exposes products to extreme conditions such as temperature and humidity, assessing their durability and operational reliability. By incorporating these rigorous testing strategies, manufacturers can identify and rectify potential issues before product release, ensuring high standards of product quality and customer satisfaction.
Advanced Testing Techniques and Tools
Advanced testing techniques and tools are pivotal in enhancing the accuracy and efficiency of SMT testing methodologies. One such approach is the use of automated X-ray inspection (AXI), which provides a non-invasive way to evaluate hidden solder joints and detect defects in complex assemblies. AXI is particularly useful for assessing connections beneath components like ball grid arrays (BGAs), where traditional optical inspection falls short. Additionally, boundary scan testing offers a powerful method for diagnosing faults in digital circuits. By leveraging special test protocols, boundary scan enables thorough testing of interconnects and integrated circuits without the need for physical probing, thereby reducing test complexity and time. Another innovative tool is the use of machine learning algorithms in defect detection, which can analyze large data sets to predict failure patterns and improve test accuracy. By integrating these advanced techniques, manufacturers can significantly enhance the quality assurance process, ensuring robust and reliable electronic products.