In der heutigen schnelllebigen Welt der Fertigung und des Produktdesigns war die Nachfrage nach innovativen und effizienten Montagetechniken noch nie so hoch. Da Unternehmen nach Schweißalternativen für Kunststoffe und die Abhängigkeit von traditionellen Befestigungsmethoden reduzieren möchten, stellt sich das Schnappverschluss-Design als vielversprechende Lösung heraus. Diese Technik, bei der Kunststoffteile ohne Schrauben oder Klebstoffe ineinandergreifen, bietet zahlreiche Vorteile, darunter Kosteneffizienz, einfache Montage und Flexibilität im Design. Durch die Nutzung der Vorteile der Schnappverschluss-Montage können Hersteller und Ingenieure ihre Produktionsprozesse verbessern und überlegene Produkte liefern. In dieser Untersuchung werden wir uns mit den Feinheiten der Schnappverschluss-Methoden befassen, ihre Rolle als führende Alternative zur Kunststoffmontage hervorheben und erklären, warum sie von zukunftsorientierten Fachleuten in Betracht gezogen werden sollten.
Grundlegendes zur Schnappmontage
Was ist Snap-Fit-Design?
Das Schnappverschluss-Design ist eine innovative Technik, die bei der Montage von Kunststoffteilen verwendet wird und die es ermöglicht, diese ohne zusätzliche Befestigungsvorrichtungen wie Schrauben oder Klebstoffe ineinander zu greifen. Bei dieser Methode werden komplementäre Merkmale an Teilen geschaffen, die sich biegen und dann durch eine Schnappwirkung einrasten. Das Design umfasst Ausleger, ringförmige Schnappverschlüsse oder Torsionsschnappverschlüsse, die für die erforderliche Flexibilität sorgen. Ein wesentlicher Vorteil des Schnappverschluss-Designs ist die einfache Montage und Demontage, was die Produktionszeit und -kosten erheblich reduziert. Darüber hinaus bieten Schnappverschlussmethoden Designflexibilität, sodass komplexe Formen und Merkmale integriert werden können, ohne die strukturelle Integrität zu beeinträchtigen. Dies macht es zu einer attraktiven Option für Hersteller, die nach Alternativen für die Kunststoffmontage suchen. Insgesamt fördert das Schnappverschluss-Design effiziente Herstellungsprozesse und Produktinnovationen und ist damit ein unverzichtbares Werkzeug für Ingenieure und Designer, die die Produktfunktionalität verbessern und die Montagekomplexität reduzieren möchten.
Beliebte Snap-Fit-Methoden
Schnappverbindungen zeichnen sich durch verschiedene Methoden aus, die jeweils auf bestimmte Anforderungen und Anwendungen zugeschnitten sind. Zu den beliebtesten gehören freitragende Schnappverbindungen, die aufgrund ihrer Einfachheit und Wirksamkeit weit verbreitet sind. Dabei handelt es sich um einen hervorstehenden Balken, der sich während der Montage biegt und in eine entsprechende Aussparung einrastet. Ringförmige Schnappverbindungen, eine weitere gängige Methode, sind ideal für kreisförmige Komponenten und bestehen aus einem ringförmigen Vorsprung, der in eine Nut einrastet. U-förmige Schnappverbindungen sind eine weitere Variante der freitragenden Schnappverbindung, mit der die Balkenlänge verlängert werden kann, wenn nicht genügend Platz vorhanden ist. Torsionsschnappverbindungen nutzen Drehbewegungen, um Teile zu sichern, und bieten eine Alternative für Baugruppen mit Rotationselementen. Jede Methode bietet je nach Anwendung unterschiedliche Vorteile, wie z. B. einfache Montage, Festigkeit und die Fähigkeit, wiederholter Demontage standzuhalten. Die Auswahl einer geeigneten Schnappverbindungsmethode hängt von Faktoren wie Materialeigenschaften, Montagekräften und Endnutzungsanforderungen ab. Durch das Verständnis dieser Methoden können Hersteller ihre Designs für effiziente, schraubenlose Montagetechniken optimieren und so robuste Schweißalternativen für Kunststoffe bereitstellen.
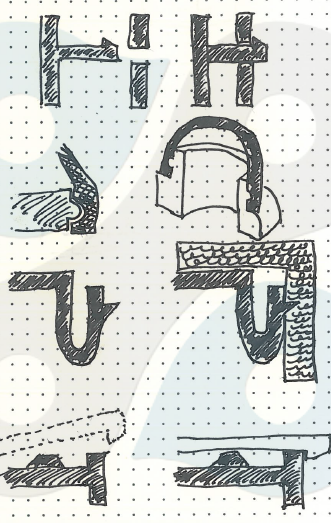
Vorteile der Schnappmontage
Die Schnappverbindung bietet mehrere überzeugende Vorteile, die sie zu einer attraktiven Wahl für modernes Produktdesign machen. Erstens steigert sie die Kosteneffizienz, da keine zusätzlichen Befestigungsmaterialien wie Schrauben und Klebstoffe erforderlich sind. Diese Materialeinsparung vereinfacht die Bestandsverwaltung und senkt die Montagekosten. Zweitens ermöglichen Schnappverbindungen schnellere Montageprozesse, da die Teile einfach zusammengesteckt werden, was den Arbeitsaufwand reduziert und die Produktionseffizienz erhöht. Darüber hinaus bietet diese Technik eine bemerkenswerte Designflexibilität, sodass Designer komplexe Geometrien erstellen können, ohne die strukturelle Integrität zu beeinträchtigen. Die einfache Montage und Demontage unterstützt auch die Produktwartung und das Recycling und steht im Einklang mit nachhaltigen Herstellungspraktiken. Darüber hinaus sorgt das inhärente Design von Schnappverbindungen für einen sicheren Halt und sorgt so für eine dauerhafte Produktzuverlässigkeit. Durch die Integration des Schnappverbindungsdesigns in ihre Arbeitsabläufe können Hersteller diese Vorteile nutzen, innovative Alternativen für die Kunststoffmontage anbieten und die Gesamtproduktleistung sowie die Marktwettbewerbsfähigkeit verbessern.
Vergleich von Montagetechniken
Alternativen zur Kunststoffmontage
Im Bereich der Kunststoffmontage suchen Hersteller zunehmend nach Alternativen zu herkömmlichen Schweiß- und Befestigungstechniken. Eine beliebte Alternative ist das Schnappverschluss-Design, das den Vorteil bietet, Kunststoffteile ohne zusätzliche Befestigungselemente zu verbinden. Diese Methode ist nicht nur kostengünstig, sondern vereinfacht auch den Montageprozess. Darüber hinaus stellt das Ultraschallschweißen eine praktikable Option dar, insbesondere für Anwendungen, die luftdichte Dichtungen erfordern. Bei dieser Methode werden Teile durch Hochfrequenzschwingungen miteinander verbunden, was Haltbarkeit und Festigkeit gewährleistet. Klebeverbindungen sind eine weitere Alternative, die Flexibilität und einfache Anwendung für eine Vielzahl von Kunststoffmaterialien bietet. Allerdings sind sie möglicherweise nicht so schnell und effizient wie andere Methoden. Mechanische Befestigungen sind zwar traditionell, bleiben aber eine zuverlässige Wahl für die Montage, insbesondere wenn eine Demontage erforderlich ist. Jede dieser Montagetechniken hat ihre eigenen Vorteile und Einschränkungen, sodass es für Hersteller entscheidend ist, sie anhand spezifischer Projektanforderungen, Materialeigenschaften und Endanwendungen zu bewerten.
Schweißalternativen für Kunststoffe
Bei der Suche nach Schweißalternativen für Kunststoffe stechen mehrere Methoden aufgrund ihrer Wirksamkeit und Effizienz hervor. Die Schnappverbindung ist eine der führenden Techniken, bei der zum Verbinden von Teilen keine Hitze oder zusätzliche Materialien erforderlich sind. Diese Methode reduziert nicht nur den Energieverbrauch, sondern vereinfacht auch den Herstellungsprozess. Eine weitere Option ist das Kleben, das Vielseitigkeit beim Verbinden verschiedener Kunststoffarten bietet. Dieser Ansatz ermöglicht Flexibilität beim Design, kann jedoch längere Aushärtezeiten erfordern. Das Ultraschallschweißen hingegen bietet eine robuste Lösung zum Erstellen starker, dauerhafter Verbindungen. Dabei werden hochfrequente Vibrationen verwendet, um Hitze zu erzeugen und Teile zu verbinden, wodurch es sich für Anwendungen eignet, die hohe Festigkeit und Präzision erfordern. Die mechanische Befestigung bleibt eine klassische Wahl, da sie eine einfache Demontage und Wartung ermöglicht. Durch die Bewertung dieser Alternativen können Hersteller anhand von Faktoren wie Produktanforderungen, Materialverträglichkeit und Skalierbarkeit der Produktion die am besten geeignete Methode auswählen und so letztendlich ihre Kunststoffmontageprozesse optimieren.
Implementierung von Snap Fit im Produktdesign
Entwerfen für den Snap-Fit-Erfolg
Bei der Entwicklung von Schnappverbindungen müssen mehrere wichtige Faktoren sorgfältig berücksichtigt werden, um eine funktionale und effiziente Montage zu gewährleisten. Zunächst ist die Materialauswahl von größter Bedeutung. Ingenieure müssen Kunststoffe mit der entsprechenden Flexibilität und Festigkeit auswählen, wie etwa Polypropylen oder Nylon, die wiederholter Montage und Demontage standhalten. Als nächstes ist die Liebe zum Detail bei der geometrischen Gestaltung von entscheidender Bedeutung. Merkmale wie Kragträger, Torsionsschnappverschlüsse und Ringringe müssen präzise konstruiert sein, um die erforderliche Haltekraft bereitzustellen, ohne Materialermüdung oder -versagen zu verursachen. Darüber hinaus spielen Toleranzen bei der Konstruktion von Schnappverbindungen eine wichtige Rolle, da sie die Montagefreundlichkeit und die Haltbarkeit der Verbindung beeinflussen. Die ordnungsgemäße Berücksichtigung von Umgebungsbedingungen wie Temperaturschwankungen und Kontakt mit Chemikalien gewährleistet die Langlebigkeit der Baugruppe. Indem Hersteller sich auf diese Designaspekte konzentrieren, können sie die Schnappverbindungsmontage optimieren, was zu zuverlässigen, effizienten und kostengünstigen Kunststoffmontagealternativen führt, die die Produktleistung und -lebensdauer verbessern.
Herausforderungen und Lösungen im Snap-Fit-Design
Das Schnappverschlussdesign ist zwar vorteilhaft, bringt aber mehrere Herausforderungen mit sich, die Designer bewältigen müssen, um erfolgreich zu sein. Eine der Hauptherausforderungen besteht darin, das richtige Gleichgewicht zwischen Steifigkeit und Flexibilität zu erreichen. Teile müssen flexibel genug sein, um einzurasten, aber starr genug, um die strukturelle Integrität aufrechtzuerhalten. Dies erfordert eine sorgfältige Materialauswahl und ein präzises Design von Geometrien wie Balken und Haken. Eine weitere Herausforderung besteht darin, Spannungskonzentrationen zu bewältigen, die zu Materialermüdung und Teileversagen führen können. Designer können dies abmildern, indem sie Rundungen einbauen und die Schnappgeometrie optimieren, um die Spannung gleichmäßig zu verteilen. Darüber hinaus ist das Erreichen enger Toleranzen entscheidend, um eine ordnungsgemäße Passform und Funktionalität sicherzustellen, was durch fortschrittliche Fertigungstechniken und gründliches Prototyping erreicht werden kann. Umweltfaktoren wie Temperaturschwankungen und chemische Belastung können sich ebenfalls auf die Leistung des Schnappverschlusses auswirken. Um diesen entgegenzuwirken, sollten Designer strenge Tests durchführen und Materialien mit geeigneten Widerstandseigenschaften auswählen. Indem sie diese Herausforderungen angehen, können Hersteller das Schnappverschlussdesign effektiv nutzen und so die Produktzuverlässigkeit und -lebensdauer verbessern.