In der schnelllebigen Welt des Produktdesigns und der Produktentwicklung hat die Integration der 3D-Drucktechnologie die Herangehensweise von Unternehmen an Rapid Prototyping und Produktentwicklung revolutioniert. Diese hochmoderne additive Fertigungstechnik bietet unzählige Vorteile und ermöglicht Ingenieuren und Designern, schnell zu iterieren, Kosten zu senken und die Markteinführungszeit zu verkürzen. Durch die Nutzung der Leistungsfähigkeit des 3D-Drucks können Unternehmen in ihren Prototyping-Prozessen ein beispielloses Maß an Präzision, Anpassung und Innovation erreichen. In diesem Artikel werden wir uns mit den vielfältigen Vorteilen des 3D-Drucks für Rapid Prototyping und Produktentwicklung befassen und untersuchen, wie diese transformative Technologie Branchen umgestaltet und Wettbewerbsvorteile schafft.
Einführung in den 3D-Druck
Entwicklung der additiven Fertigung
Die additive Fertigung, allgemein bekannt als 3D-Druck, hat seit ihrer Einführung in den 1980er Jahren eine bedeutende Entwicklung durchgemacht. Ursprünglich wurde sie hauptsächlich zur Herstellung einfacher Kunststoffprototypen verwendet. Doch technologische Fortschritte haben ihre Möglichkeiten und Anwendungen erweitert. Frühe Methoden wie Stereolithografie (SLA) und selektives Lasersintern (SLS) ebneten den Weg für anspruchsvollere Techniken wie Fused Deposition Modeling (FDM) und Digital Light Processing (DLP). Heute umfasst der 3D-Druck eine Vielzahl von Materialien, darunter Metalle, Keramik und Biomaterialien, was ein breiteres Anwendungsspektrum ermöglicht. Diese Fortschritte haben den 3D-Druck von einem Nischenwerkzeug für das Prototyping zu einer Mainstream-Methode für die Entwicklung umfassender Produkte und sogar die Endverbraucherfertigung gemacht. Die kontinuierliche Innovation bei additiven Fertigungstechnologien unterstreicht ihre transformative Wirkung auf Branchen von der Gesundheitsversorgung bis zur Luft- und Raumfahrt und macht sie zu einem unverzichtbaren Werkzeug für moderne Ingenieure und Designer.
Schlüsseltechnologien im 3D-Druck
Mehrere Schlüsseltechnologien bilden die Grundlage für die Leistungsfähigkeit des modernen 3D-Drucks. Fused Deposition Modeling (FDM) ist eine der am weitesten verbreiteten Methoden und ideal für die Herstellung langlebiger und funktionaler Teile aus thermoplastischen Materialien. Bei der Stereolithografie (SLA) wird flüssiges Harz mithilfe eines Lasers zu festen Teilen ausgehärtet, wodurch hochpräzise und glatte Oberflächen entstehen. Beim selektiven Lasersintern (SLS) wird pulverförmiges Material mithilfe eines Lasers verschmolzen, wodurch die Herstellung komplexer Geometrien ohne Stützstrukturen möglich wird. Digital Light Processing (DLP) ähnelt SLA, verwendet jedoch einen digitalen Lichtprojektor zum Aushärten des Harzes, wodurch schnellere Druckzeiten möglich sind. Darüber hinaus haben Fortschritte im 3D-Druck von Metallen, wie beispielsweise das direkte Metall-Lasersintern (DMLS) und das Elektronenstrahlschmelzen (EBM), neue Möglichkeiten in Branchen eröffnet, die hochfeste Komponenten benötigen. Jede Technologie bietet unterschiedliche Vorteile, wodurch der 3D-Druck zu einem vielseitigen Werkzeug für verschiedene Anwendungen im Bereich Rapid Prototyping und Produktentwicklung wird.
Markteinfluss und Trends
Die Auswirkungen des 3D-Drucks auf den Markt sind tiefgreifend und nehmen weiter zu. Ursprünglich hauptsächlich für Rapid Prototyping eingesetzt, hat sich der 3D-Druck auf die Serienproduktion und Endverbrauchsteile ausgeweitet und Branchen wie die Luft- und Raumfahrt, die Automobilindustrie, das Gesundheitswesen und die Konsumgüterindustrie revolutioniert. Die Möglichkeit, komplexe Geometrien und kundenspezifische Produkte auf Anfrage herzustellen, hat zu einer deutlichen Reduzierung der Vorlaufzeiten und Herstellungskosten geführt. Darüber hinaus verändert der Aufstieg verteilter Fertigungsmodelle, bei denen die Produktion lokalisiert und nach Bedarf skaliert werden kann, die Dynamik der Lieferkette. Zu den neuen Trends im 3D-Druck gehören die Entwicklung neuer Materialien wie biokompatibler und hochtemperaturbeständiger Polymere sowie Fortschritte im Mehrmaterialdruck. Die Integration künstlicher Intelligenz und maschinellen Lernens zur Optimierung von Druckprozessen und Verbesserung der Qualitätskontrolle steht ebenfalls bevor. Diese Trends unterstreichen die fortlaufende Entwicklung und zunehmende Bedeutung des 3D-Drucks in der modernen Fertigung und Produktentwicklung.
Vorteile des 3D-Drucks
Kostengünstige Prototyping-Lösungen
Einer der größten Vorteile des 3D-Drucks ist seine Kosteneffizienz bei der Prototypenerstellung. Herkömmliche Fertigungsmethoden erfordern häufig teure Formen und Werkzeuge, die für kleine Auflagen oder iterative Designprozesse unerschwinglich sein können. Im Gegensatz dazu entfallen beim 3D-Druck diese Vorlaufkosten, sodass Designer und Ingenieure Prototypen direkt aus digitalen Modellen erstellen können. Dies reduziert nicht nur den Materialabfall, sondern senkt auch die Produktionskosten erheblich. Darüber hinaus ermöglicht der 3D-Druck eine schnelle Iteration, d. h. Prototypen können in einem Bruchteil der Zeit hergestellt, getestet und verfeinert werden, die mit herkömmlichen Methoden erforderlich wäre. Dieser beschleunigte Prozess hilft Unternehmen, Produkte schneller auf den Markt zu bringen und gleichzeitig die Entwicklungskosten unter Kontrolle zu halten. Die Möglichkeit, Prototypen auf Anfrage herzustellen, bedeutet auch, dass Unternehmen schneller auf Marktfeedback und sich entwickelnde Kundenbedürfnisse reagieren können, was ihren Wettbewerbsvorteil steigert.
Beschleunigen Sie die Produktentwicklungszeitpläne
3D-Druck beschleunigt die Produktentwicklungszeit deutlich und bietet einen erheblichen Vorteil in wettbewerbsintensiven Märkten. Herkömmliche Fertigungsprozesse können zeitaufwändig sein und erfordern oft Wochen oder sogar Monate für die Werkzeugherstellung und Einrichtung. Im Gegensatz dazu ermöglicht 3D-Druck die direkte Erstellung von Teilen und Prototypen aus digitalen Designs, wodurch die Vorlaufzeiten drastisch verkürzt werden. Diese schnelle Bearbeitungszeit ermöglicht schnelleres Testen und Validieren von Designkonzepten, wodurch mehr Iterationen in kürzerer Zeit möglich sind. Folglich können Unternehmen schnell vom ersten Konzept zum Endprodukt gelangen und so die Markteinführungszeit verkürzen. Darüber hinaus bedeutet die Möglichkeit, schnell funktionsfähige Prototypen herzustellen, dass Designfehler frühzeitig im Entwicklungszyklus erkannt und behoben werden können, was den Prozess weiter rationalisiert. Durch den Einsatz von 3D-Druck können Unternehmen nicht nur ihre Innovationsfähigkeit verbessern, sondern auch flexibler auf Marktanforderungen und -änderungen reagieren und so einen Wettbewerbsvorteil in ihren jeweiligen Branchen aufrechterhalten.
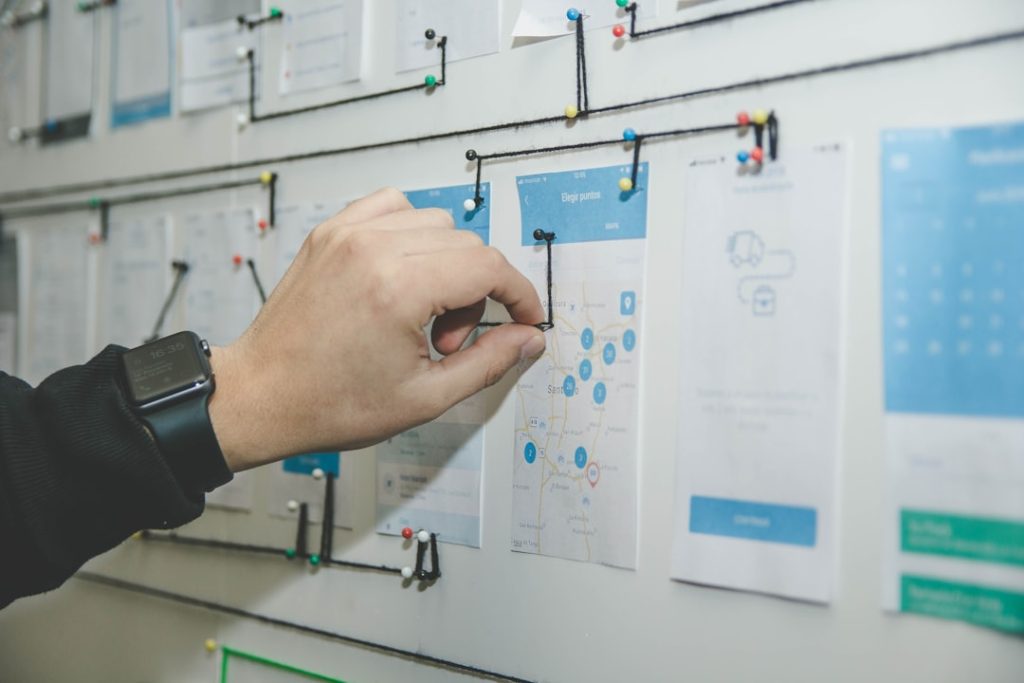
Anpassung und Flexibilität im Design
Der 3D-Druck bietet beispiellose Anpassungsmöglichkeiten und Flexibilität im Design und ist damit ein unverzichtbares Werkzeug für die moderne Produktentwicklung. Herkömmliche Fertigungsmethoden schränken die Komplexität und Anpassung des Designs aufgrund der Einschränkungen bei Formen und Werkzeugen häufig ein. Im Gegensatz dazu ermöglicht der 3D-Druck die Erstellung hochkomplexer und personalisierter Designs direkt aus digitalen Dateien. Diese Fähigkeit ist besonders in Branchen von Vorteil, die maßgeschneiderte Lösungen erfordern, wie z. B. bei medizinischen Geräten, wo patientenspezifische Modelle mit Präzision hergestellt werden können. Darüber hinaus ermöglicht der 3D-Druck einfache Änderungen an vorhandenen Designs ohne erhebliche Kosten- oder Zeitauswirkungen, was schnelle Iterationen und Anpassungen ermöglicht. Die Flexibilität, auf kostengünstige Weise mit verschiedenen Geometrien, Materialien und Strukturen zu experimentieren, fördert Innovation und Kreativität bei Designern und Ingenieuren. Dadurch können Unternehmen ihren Kunden maßgeschneiderte Produkte anbieten, die Benutzererfahrung und -zufriedenheit verbessern und sich gleichzeitig auf dem Markt differenzieren.
Rapid Prototyping mit 3D-Druck
Verkürzung des Designzyklus
Der 3D-Druck spielt eine entscheidende Rolle bei der Verkürzung des Designzyklus, einem wichtigen Vorteil des Rapid Prototyping. Herkömmliche Prototyping-Methoden können langwierig sein und umfassen oft mehrere Phasen des Designs, der Herstellung und des Testens, die jeweils mit den damit verbundenen Verzögerungen verbunden sind. Im Gegensatz dazu ermöglicht der 3D-Druck die schnelle Herstellung von Prototypen direkt aus digitalen Modellen, wodurch die für jede Iteration erforderliche Zeit erheblich reduziert wird. Diese unmittelbare Feedbackschleife ermöglicht es Designern und Ingenieuren, ihre Konzepte schnell zu testen und zu verfeinern, was zu schnelleren Entscheidungen und weniger Entwicklungsengpässen führt. Darüber hinaus bedeutet die Möglichkeit, funktionsfähige Prototypen herzustellen, dass Tests in der realen Welt früher im Designprozess durchgeführt werden können, wodurch potenzielle Probleme identifiziert werden können, bevor sie zu kostspieligen Problemen werden. Dieser beschleunigte Zyklus verkürzt nicht nur die Entwicklungszeitpläne, sondern verbessert auch die Gesamtqualität des Endprodukts. Durch die Integration des 3D-Drucks in ihre Prototyping-Prozesse können Unternehmen eine effizientere und effektivere Produktentwicklung erreichen und so in wettbewerbsintensiven Märkten die Nase vorn behalten.
Verkürzung der Markteinführungszeit
3D-Druck verkürzt die Markteinführungszeit erheblich, ein entscheidender Erfolgsfaktor in den heutigen schnelllebigen Branchen. Herkömmliche Fertigungsmethoden umfassen langwierige Prozesse wie Werkzeugbau, Formenbau und Einrichtung von Fließbändern, was die Produkteinführung verzögern kann. Im Gegensatz dazu entfallen beim 3D-Druck diese zeitaufwändigen Schritte, sodass Produkte in einem Bruchteil der Zeit entworfen, als Prototyp erstellt und produziert werden können. Diese schnelle Abwicklung bedeutet, dass Unternehmen schneller auf Marktanforderungen und -chancen reagieren und neue Produkte schneller auf den Markt bringen können als ihre Konkurrenten. Darüber hinaus stellt die Möglichkeit, Prototypen schnell herzustellen und zu testen, sicher, dass etwaige Konstruktionsfehler frühzeitig erkannt und korrigiert werden, wodurch kostspielige Verzögerungen später im Produktionszyklus vermieden werden. Durch die Integration des 3D-Drucks in ihre Entwicklungsprozesse können Unternehmen ihre Arbeitsabläufe optimieren, Vorlaufzeiten verkürzen und ihre Agilität steigern. Diese Fähigkeit verbessert nicht nur die Betriebseffizienz, sondern versetzt Unternehmen auch in die Lage, Markttrends und Verbraucherpräferenzen effektiver zu nutzen.
Verbesserung iterativer Tests und Feedback
3D-Druck verbessert iterative Tests und Feedback erheblich, ein wesentlicher Bestandteil einer erfolgreichen Produktentwicklung. Herkömmliche Prototyping-Methoden können langsam und teuer sein und die Anzahl der Iterationen, die ein Design durchlaufen kann, begrenzen. Mit 3D-Druck können Prototypen schnell und kostengünstig hergestellt werden, sodass Designer und Ingenieure mehrere Varianten in kurzer Zeit testen können. Dieser schnelle Iterationsprozess ermöglicht sofortiges Feedback und ermöglicht schnellere Entscheidungen und Verfeinerungen von Designs. Funktionale Prototypen, die durch 3D-Druck erstellt wurden, können unter realen Bedingungen getestet werden und liefern wertvolle Einblicke in Leistung und Benutzerfreundlichkeit. Diese praktische Bewertung hilft dabei, potenzielle Probleme frühzeitig zu erkennen und sicherzustellen, dass nur die optimiertesten und zuverlässigsten Versionen in die letzten Entwicklungsphasen gelangen. Darüber hinaus stellt die Möglichkeit, Feedback schnell in neue Iterationen einzubeziehen, sicher, dass das Endprodukt die Erwartungen der Benutzer erfüllt oder übertrifft. Durch die Nutzung des 3D-Drucks für iterative Tests können Unternehmen ihre Produktqualität, Innovation und allgemeine Marktreife verbessern.
3D-Druck in der Produktentwicklung
Rationalisierung des F&E-Prozesses
3D-Druck rationalisiert den Forschungs- und Entwicklungsprozess (F&E) und macht ihn effizienter und kostengünstiger. Traditionelle F&E umfasst oft mehrere Phasen des Designs, der Prototypisierung und des Testens, die jeweils viel Zeit und Ressourcen erfordern. 3D-Druck vereinfacht diesen Zyklus, indem er die direkte Herstellung von Prototypen aus digitalen Modellen ermöglicht und so die Notwendigkeit komplexer Werkzeug- und Formenherstellung umgeht. Diese Fähigkeit ermöglicht es F&E-Teams, neue Designs schnell zu testen und zu iterieren, was die Entdeckung und Verfeinerung innovativer Lösungen beschleunigt. Darüber hinaus bedeutet die Flexibilität des 3D-Drucks, dass eine breite Palette von Materialien und Geometrien ohne umfangreiche Umrüstungen untersucht werden kann, was mehr Experimentierfreude und Kreativität fördert. Rapid Prototyping erleichtert auch die Echtzeit-Zusammenarbeit zwischen funktionsübergreifenden Teams, da Änderungen im Handumdrehen implementiert und getestet werden können. Durch die Integration des 3D-Drucks in den F&E-Prozess können Unternehmen die Entwicklungszeit verkürzen, die Kosten senken und ihre Innovationsfähigkeit steigern, was letztendlich zu erfolgreicheren Produktergebnissen führt.
Verbesserung der Produktqualität und -leistung
Der 3D-Druck spielt eine entscheidende Rolle bei der Verbesserung der Produktqualität und -leistung während der Entwicklungsphase. Herkömmliche Fertigungsmethoden können die Komplexität und Präzision von Designs aufgrund von Werkzeugbeschränkungen manchmal einschränken. Im Gegensatz dazu ermöglicht der 3D-Druck die Erstellung komplexer und hochdetaillierter Prototypen, wodurch Produktfunktionen genauer getestet und validiert werden können. Dieses hohe Maß an Präzision stellt sicher, dass Designfehler frühzeitig im Entwicklungsprozess erkannt und korrigiert werden, was zu qualitativ hochwertigeren Endprodukten führt. Darüber hinaus erleichtert der 3D-Druck die Verwendung fortschrittlicher Materialien und innovativer Strukturen, die die Leistung und Haltbarkeit des Endprodukts verbessern können. Die Möglichkeit, diese Variationen schnell zu erstellen und zu testen, stellt sicher, dass nur die effektivsten Designs weiterkommen. Durch gründliche Tests und Verfeinerungen hilft der 3D-Druck Unternehmen dabei, eine überlegene Produktleistung, Zuverlässigkeit und Kundenzufriedenheit zu erzielen, was letztendlich zu Wettbewerbsvorteilen auf dem Markt führt.
Fallstudien und Erfolgsgeschichten
Zahlreiche Fallstudien und Erfolgsgeschichten unterstreichen die transformative Wirkung des 3D-Drucks in der Produktentwicklung. Automobilunternehmen wie Ford haben beispielsweise den 3D-Druck genutzt, um kundenspezifische Werkzeuge und Komponenten herzustellen und so die Produktionskosten und -zeit erheblich zu senken. Im Gesundheitssektor hat der 3D-Druck die Entwicklung patientenspezifischer Implantate und Prothesen ermöglicht, was zu besseren Patientenergebnissen und einer verbesserten Lebensqualität geführt hat. Luft- und Raumfahrtgiganten wie Boeing und Airbus nutzen den 3D-Druck, um leichte und dennoch robuste Teile herzustellen und so die Leistung und Treibstoffeffizienz von Flugzeugen zu verbessern. Unternehmen der Unterhaltungselektronik haben den 3D-Druck ebenfalls eingeführt, um die Prototypenentwicklung und das Testen neuer Geräte zu beschleunigen und so eine schnellere Markteinführung zu gewährleisten. Diese Beispiele aus der Praxis zeigen, wie der 3D-Druck Innovation, Effizienz und Wettbewerbsvorteile in verschiedenen Branchen vorantreiben kann. Durch den Einsatz von 3D-Drucktechnologien können Unternehmen bemerkenswerte Verbesserungen in der Produktentwicklung erzielen, vom ersten Entwurf bis zur endgültigen Produktion, und ihren Kunden letztendlich überlegene Produkte liefern.
Zukunft der additiven Fertigung
Neue Technologien und Innovationen
Die Zukunft der additiven Fertigung steckt voller neuer Technologien und Innovationen, die das Feld weiter revolutionieren werden. Ein bemerkenswerter Fortschritt ist die Entwicklung des Multimaterial-3D-Drucks, der die gleichzeitige Verwendung verschiedener Materialien in einem einzigen Druck ermöglicht. Dies eröffnet neue Möglichkeiten für die Herstellung komplexer, funktionaler Produkte mit unterschiedlichen Eigenschaften. Eine weitere spannende Innovation ist die Integration von künstlicher Intelligenz und maschinellen Lernalgorithmen zur Optimierung von Druckprozessen, Verbesserung der Qualitätskontrolle und Vorhersage des Wartungsbedarfs. Darüber hinaus erweitert die Forschung an neuen druckbaren Materialien wie leitfähigen Tinten für elektronische Komponenten und Biotinten für die Gewebezüchtung die Anwendungsmöglichkeiten des 3D-Drucks. Es werden auch Hochgeschwindigkeits-3D-Drucktechnologien entwickelt, die die Produktionszeiten erheblich verkürzen und die additive Fertigung für die Massenproduktion rentabler machen. Diese neuen Technologien und Innovationen unterstreichen die fortlaufende Entwicklung und das Potenzial des 3D-Drucks und positionieren ihn als Eckpfeiler zukünftiger Fertigungs- und Produktentwicklungsstrategien.
Branchenanwendungen und Chancen
Die Zukunft der additiven Fertigung bietet in zahlreichen Branchen enorme Chancen und fördert Innovation und Effizienz. Im Gesundheitswesen wird der 3D-Druck die personalisierte Medizin durch die Herstellung maßgeschneiderter Prothesen, Implantate und sogar biogedruckter Organe revolutionieren. Die Luft- und Raumfahrtindustrie wird von leichten, hochfesten Komponenten profitieren, die Kraftstoffeffizienz und Leistung verbessern. Automobilhersteller erkunden den 3D-Druck, um kundenspezifische Teile herzustellen und Montagezeiten zu verkürzen, wodurch die Produktionsprozesse optimiert werden. Im Konsumgütersektor nutzen Unternehmen den 3D-Druck, um maßgeschneiderte Produkte anzubieten, die auf individuelle Vorlieben zugeschnitten sind und so die Kundenzufriedenheit steigern. Darüber hinaus beginnt die Bauindustrie, großformatigen 3D-Druck einzusetzen, um komplexe Strukturen schneller und kostengünstiger zu bauen. Diese Anwendungen zeigen den großen Umfang und das Potenzial des 3D-Drucks, traditionelle Fertigungsparadigmen zu verändern. Mit dem technologischen Fortschritt werden sich weiterhin neue Möglichkeiten ergeben, die die additive Fertigung als entscheidendes Instrument für zukünftige industrielle Innovation und Wachstum festigen.
Vorbereitung auf die nächste Welle von Fortschritten
Da sich der Bereich der additiven Fertigung ständig weiterentwickelt, müssen sich Unternehmen auf die nächste Welle von Fortschritten vorbereiten, um wettbewerbsfähig zu bleiben. Investitionen in die neuesten 3D-Drucktechnologien und -materialien sind entscheidend, um Innovation und Effizienz voranzutreiben. Unternehmen sollten sich auch auf die Weiterbildung ihrer Belegschaft konzentrieren und Schulungen in neuen Techniken und Werkzeugen anbieten, um die Möglichkeiten des fortschrittlichen 3D-Drucks voll auszuschöpfen. Die Zusammenarbeit mit Forschungseinrichtungen und Industriepartnern kann den Wissensaustausch fördern und die Einführung modernster Entwicklungen beschleunigen. Darüber hinaus kann die Integration von Strategien zur digitalen Transformation, wie der Einsatz von KI und maschinellem Lernen zur Prozessoptimierung, die Produktivität und Qualität weiter steigern. Wenn Unternehmen über neue Trends und regulatorische Änderungen auf dem Laufenden bleiben, können sie sich anpassen und neue Chancen nutzen. Indem sie diese Fortschritte proaktiv nutzen, können sich Unternehmen an die Spitze der Revolution der additiven Fertigung stellen und sicherstellen, dass sie in ihren jeweiligen Branchen führend bleiben.