In der sich ständig weiterentwickelnden Fertigungslandschaft ist die Präzision der Formflussanalyse beim Spritzgießen ein entscheidender Faktor für Brancheninnovatoren, die ihre Produktionsprozesse verfeinern möchten. Die Formflussanalyse ist ein entscheidender Bestandteil des Designs für den Fertigungsprozess, mit dem Ingenieure vorhersagen können, wie sich geschmolzener Kunststoff in einer Formhöhle verhält, um optimale Qualität und Effizienz sicherzustellen. Diese anspruchsvolle Simulationstechnik ist entscheidend, um potenzielle Defekte zu identifizieren, Materialabfälle zu minimieren und die Markteinführungszeit zu verkürzen. Durch die Nutzung fortschrittlicher Formflussanalysedienste können Unternehmen die Produktleistung verbessern und sich einen Wettbewerbsvorteil verschaffen. In dieser Untersuchung werden wir uns mit den Feinheiten der Formflussanalyse befassen und ihre Bedeutung und die tiefgreifenden Auswirkungen hervorheben, die sie auf den Fertigungssektor hat.
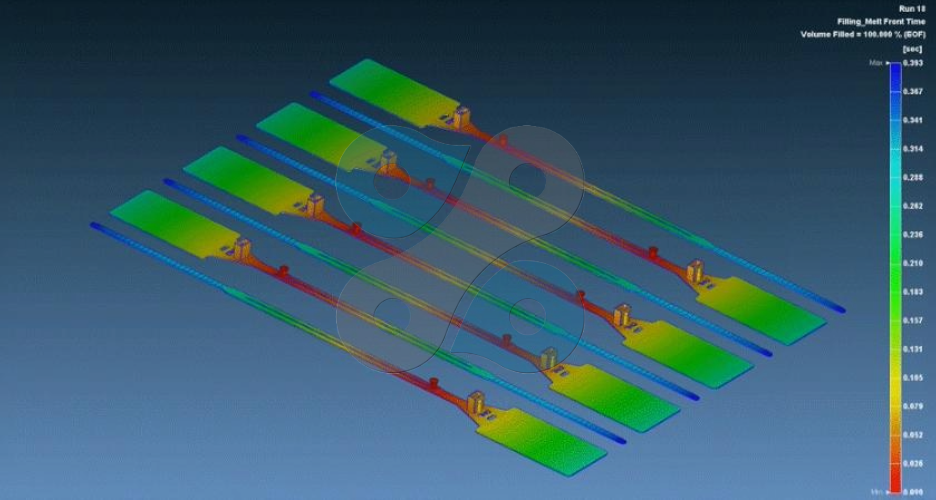
Moldflow-Analyse verstehen
Was ist eine Moldflow-Analyse?
Die Moldflow-Analyse ist ein anspruchsvolles Simulationsverfahren, das beim Spritzgießen verwendet wird, um das Verhalten von geschmolzenem Kunststoff in einer Formhöhle vorherzusagen. Diese Technik nutzt fortschrittliche Rechenwerkzeuge, um den Fluss, die Abkühlung und die Verfestigung von Kunststoffmaterialien während des Spritzgussverfahrens zu modellieren. Durch die Simulation dieser Dynamik können Ingenieure potenzielle Probleme wie Lufteinschlüsse, Bindenähte oder übermäßige Schrumpfung lange vor Beginn der eigentlichen Produktion vorhersehen. Diese Vorhersagefähigkeit ist entscheidend für die Optimierung von Formdesigns, die Gewährleistung der Produktqualität und die Verbesserung der Fertigungseffizienz. Die aus der Moldflow-Analyse gewonnenen Ergebnisse leiten wichtige Entscheidungen in der Entwurfsphase und ermöglichen Anpassungen, die die Zykluszeiten verkürzen, Defekte minimieren und Materialabfall verringern. Unternehmen, die Moldflow-Analysedienste nutzen, können Erkenntnisse gewinnen, die zu einer verbesserten Produktleistung und geringeren Kosten führen, was sie zu einem unverzichtbaren Werkzeug in der Fertigungsindustrie macht.
Bedeutung im Spritzguss
Die Moldflow-Analyse spielt im Spritzgussverfahren eine entscheidende Rolle, da sie Präzision und Effizienz fördert. Sie ermöglicht es Herstellern, potenzielle Probleme zu visualisieren und ihre Designs vor der Produktion zu verfeinern, wodurch kostspielige Fehler reduziert werden. Durch frühzeitiges Erkennen von Problemen wie unvollständigen Füllungen, Verformungen oder Einfallstellen können Unternehmen notwendige Anpassungen am Formendesign oder den Verarbeitungsbedingungen vornehmen. Diese Vorausschau trägt nicht nur zur Verbesserung der Produktqualität bei, sondern beschleunigt auch die Markteinführungszeit erheblich. Darüber hinaus hilft die Moldflow-Analyse bei der Optimierung des Materialverbrauchs, was zu erheblichen Kosteneinsparungen führen kann. In einer wettbewerbsorientierten Fertigungslandschaft sind diese Vorteile von entscheidender Bedeutung. Die Nutzung von Moldflow-Analysediensten stellt sicher, dass Unternehmen einen hohen Qualitätsstandard aufrechterhalten und flexibel auf die Marktanforderungen reagieren können. Daher ist die Moldflow-Analyse für Unternehmen, die nach Innovation und Spitzenleistung im Spritzguss streben, unverzichtbar.
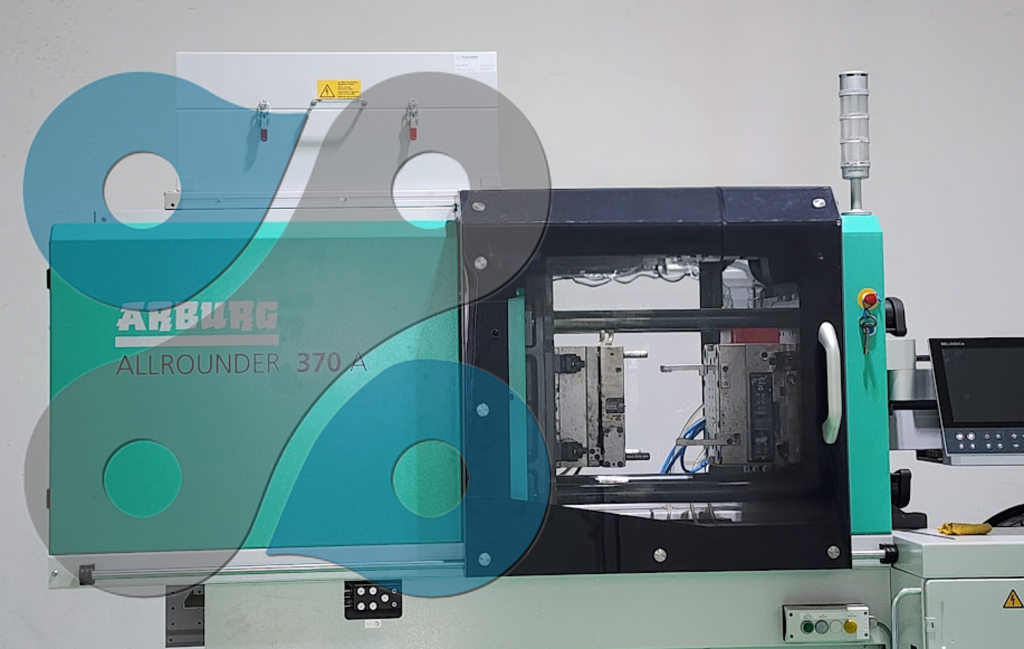
Wichtige Vorteile für Hersteller
Die Moldflow-Analyse bietet Herstellern zahlreiche Vorteile, die ihre Produktionsprozesse erheblich verbessern können. Einer der Hauptvorteile ist die Möglichkeit, potenzielle Defekte wie Lufteinschlüsse, Bindenähte und Verzug vorherzusagen und zu beheben, bevor sie auftreten. Dieser proaktive Ansatz führt zu qualitativ hochwertigeren Produkten und weniger Produktionsverzögerungen. Darüber hinaus hilft die Moldflow-Analyse bei der Optimierung des Formdesigns und der Verarbeitungsparameter, was die Zykluszeiten verkürzen und die Produktionseffizienz steigern kann.
Ein weiterer wesentlicher Vorteil ist die Reduzierung des Materialabfalls. Durch die genaue Vorhersage, wie der geschmolzene Kunststoff fließt und erstarren wird, können Hersteller die verwendete Materialmenge genau abstimmen, was zu erheblichen Kosteneinsparungen führt. Darüber hinaus ermöglichen Mold-Flow-Analysedienste eine schnellere Markteinführung, indem sie den Entwicklungsprozess rationalisieren und die Notwendigkeit mehrerer Iterationen physischer Prototypen reduzieren. Zusammengenommen verschaffen diese Vorteile den Herstellern einen Wettbewerbsvorteil und stellen sicher, dass sie die Marktanforderungen schnell und effektiv erfüllen können.
Genauigkeit in der Moldflow-Analyse
Faktoren, die die Präzision beeinflussen
Die Genauigkeit der Moldflow-Analyse kann von verschiedenen Faktoren beeinflusst werden, die für genaue Vorhersagen beim Spritzgießen entscheidend sind. Ein Schlüsselfaktor ist die Qualität der Eingabedaten. Genaue Materialeigenschaften wie Viskosität, Wärmeleitfähigkeit und spezifische Wärme sind für zuverlässige Simulationsergebnisse unerlässlich. Darüber hinaus können die geometrische Komplexität der Form und die Genauigkeit des in der Simulation verwendeten Netzes die Genauigkeit beeinflussen. Ein feineres Netz liefert in der Regel detailliertere Ergebnisse, erfordert jedoch mehr Rechenressourcen.
Ein weiterer wichtiger Aspekt ist die Vollständigkeit der Prozessparameter. Faktoren wie Einspritzgeschwindigkeit, Druck und Temperaturprofile sollten genau definiert sein, um die realen Bedingungen widerzuspiegeln. Darüber hinaus spielen auch die Softwarefunktionen und das Fachwissen der Ingenieure, die die Analyse durchführen, eine wichtige Rolle. Fortgeschrittene Moldflow-Analysedienste verwenden häufig hochmoderne Software und erfahrene Analysten, um die Präzision zu verbessern. Durch sorgfältiges Management dieser Faktoren können Hersteller sicherstellen, dass die Moldflow-Analyse wertvolle Erkenntnisse und Verbesserungen liefert.
Vergleich von Moldflow-Analysediensten
Bei der Bewertung von Moldflow-Analysediensten sollten mehrere Faktoren berücksichtigt werden, um optimale Ergebnisse zu erzielen. Bewerten Sie zunächst die vom Dienstanbieter verwendeten Softwaretools. Spitzensoftware, die erweiterte Simulationsfunktionen unterstützt, liefert häufig genauere und zuverlässigere Ergebnisse. Berücksichtigen Sie außerdem das Fachwissen und die Erfahrung des Anbieters, da erfahrene Ingenieure die Qualität der Analyse durch ihre Erkenntnisse und ihre Liebe zum Detail erheblich verbessern können.
Ein weiterer wichtiger Aspekt ist die Anpassung der Services. Verschiedene Projekte erfordern möglicherweise maßgeschneiderte Lösungen basierend auf bestimmten Materialien, Geometrien oder Produktionszielen. Anbieter, die flexible Analyseoptionen anbieten, können einzigartige Projektanforderungen besser erfüllen. Darüber hinaus ist die zeitnahe Bereitstellung von Ergebnissen in schnelllebigen Fertigungsumgebungen von entscheidender Bedeutung. Daher ist die Bewertung der Bearbeitungszeit eines Anbieters von entscheidender Bedeutung.
Berücksichtigen Sie abschließend den Grad der Unterstützung und Kommunikation, die während des gesamten Prozesses angeboten wird. Eine klare und konsistente Kommunikation kann eine bessere Zusammenarbeit ermöglichen und sicherstellen, dass die Analyse mit Ihren Zielen übereinstimmt. Der Vergleich dieser Aspekte hilft bei der Auswahl eines Dienstes, der Ihren Fertigungsanforderungen am besten entspricht.
Fallstudien und Beispiele aus der Praxis
Die Auswirkungen der Moldflow-Analyse in realen Szenarien können enorm sein, wie zahlreiche Fallstudien in verschiedenen Branchen belegen. So nutzte beispielsweise ein Automobilhersteller die Moldflow-Analyse, um ein Bauteil neu zu gestalten, das anfällig für Verformungen war. Durch die Simulation verschiedener Formdesigns und Prozessbedingungen fand er eine Lösung, die die Fehlerrate um 30 % reduzierte und die Zuverlässigkeit und Leistung des Bauteils deutlich verbesserte.
Im Bereich Unterhaltungselektronik stand ein Unternehmen vor dem Problem unvollständiger Füllungen in einem komplexen Gehäuse. Durch eine detaillierte Moldflow-Analyse optimierte es die Angussstellen und passte die Einspritzgeschwindigkeit an, was zu einer Verkürzung der Produktionszeit und erheblichen Materialeinsparungen führte.
Ebenso nutzte ein Hersteller medizinischer Geräte Moldflow-Analysedienste, um ein kleines, kompliziertes Teil zu verfeinern. Die Analyse ermöglichte es dem Hersteller, potenzielle Bindenähte vorherzusagen und das Formdesign entsprechend anzupassen, wodurch die strukturelle Integrität des Teils verbessert wurde. Diese Beispiele zeigen, wie Moldflow-Analysen Innovation und Effizienz in unterschiedlichen Fertigungskontexten vorantreiben können.
Integrieren von Moldflow in den Designprozess
Verbessertes Design für die Fertigung
Die Integration der Moldflow-Analyse in den Design-for-Manufacturing-Prozess (DFM) verbessert die Produktentwicklung erheblich, indem potenzielle Produktionsprobleme präventiv angegangen werden. Durch die Einbeziehung dieser Analyse in die frühe Entwurfsphase können Ingenieure fundierte Entscheidungen treffen, die die Herstellbarkeit und Produktqualität verbessern. Die aus Moldflow-Simulationen gewonnenen Erkenntnisse ermöglichen die Optimierung des Formdesigns, z. B. durch Anpassen der Wandstärke, Ändern der Angusspositionen und Verfeinern der Materialflusswege.
Einer der Hauptvorteile ist die Reduzierung kostspieliger Designänderungen. Durch die Identifizierung und Lösung von Problemen vor der physischen Prototypisierung können Hersteller zeitaufwändige und teure Anpassungen vermeiden. Darüber hinaus ermöglicht die Moldflow-Analyse die Untersuchung verschiedener Designalternativen und hilft dabei, die effizientesten und kostengünstigsten Lösungen zu finden.
Dieser proaktive Ansatz verkürzt nicht nur den Entwicklungszyklus, sondern stellt auch sicher, dass das Endprodukt den Leistungs- und Qualitätsstandards entspricht. Durch die Integration der Moldflow-Analyse in den DFM-Prozess können Hersteller schneller und kostengünstiger hochwertige Produkte liefern.
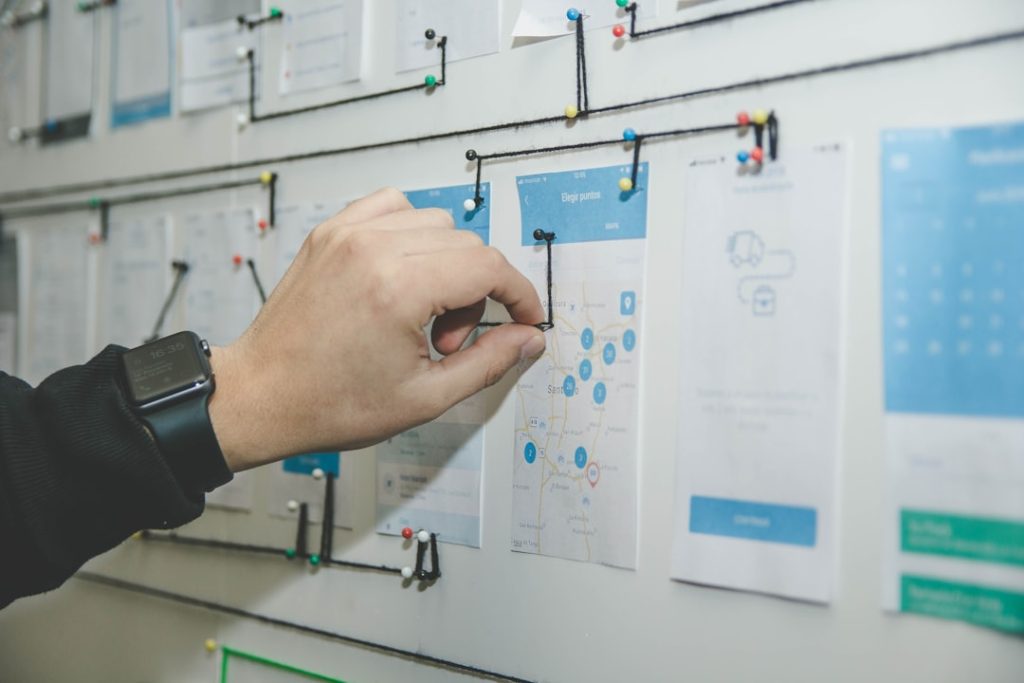