In der wettbewerbsorientierten Fertigungswelt ist die Erzielung von Prozessrobustheit beim Kunststoffspritzguss ein entscheidender Faktor zur Gewährleistung einer gleichbleibenden Teilequalität und Fertigungseffizienz. Parallele Entwicklung erweist sich als Schlüsselstrategie zur Bewältigung der komplexen Herausforderungen des Spritzgussprozesses und ermöglicht eine nahtlose Zusammenarbeit zwischen Design-, Entwicklungs- und Produktionsteams. Durch die Integration paralleler Entwicklungspraktiken können Unternehmen die Qualitätssicherung verbessern, die Designvalidierung optimieren und Abläufe rationalisieren, um die anspruchsvollen Standards ihrer Kunden zu erfüllen. In diesem Artikel werden wir uns mit den fünf kritischen Faktoren befassen, die die gleichbleibende Teilequalität beeinflussen, und untersuchen, wie die Einführung paralleler Entwicklung zu einem robusten und effizienten Spritzgussprozess führen und Unternehmen so als Branchenführer positionieren kann.
Bedeutung der Prozessrobustheit
Faktoren, die die Teilequalität beeinflussen
Beim Kunststoffspritzguss wird die Konsistenz der Teilequalität von mehreren kritischen Faktoren beeinflusst. Die Materialauswahl ist von größter Bedeutung, da sie sich auf die Festigkeit, Haltbarkeit und Verarbeitung des Endprodukts auswirkt. Die richtige Materialauswahl stellt sicher, dass die Teile die erforderlichen Spezifikationen erfüllen und über ihre gesamte Lebensdauer hinweg zuverlässig funktionieren. Darüber hinaus spielt das Formendesign eine entscheidende Rolle. Um Defekte wie Verformungen oder unvollständige Füllungen zu vermeiden, ist eine detaillierte Beachtung des Hohlraumdesigns, der Kühlkanäle und der Auswurfmechanismen erforderlich. Prozessparameter wie Temperatur, Druck und Einspritzgeschwindigkeit müssen sorgfältig kontrolliert und überwacht werden, um die Einheitlichkeit der Teileproduktion aufrechtzuerhalten. Darüber hinaus ist die Wartung der Geräte unerlässlich, um unerwartete Ausfallzeiten oder Fehlfunktionen zu vermeiden, die die Teilequalität beeinträchtigen könnten. Durch das Verständnis und die Optimierung dieser Faktoren können Hersteller die Prozessrobustheit und die Konsistenz der Teilequalität erheblich verbessern, was zu einer höheren Zufriedenheit der Kunden führt, die nach Hochleistungskunststoffkomponenten suchen.
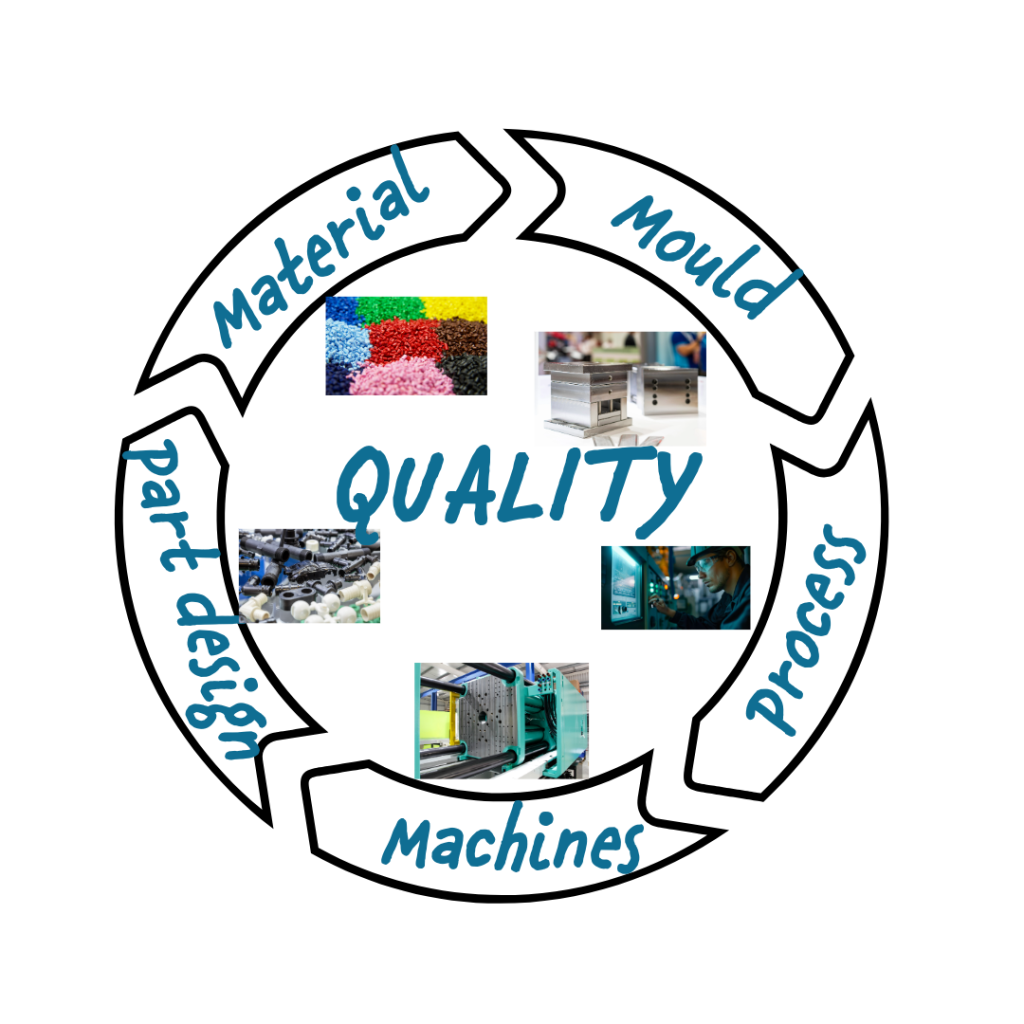
Erzielen eines konsistenten Formprozesses
Ein konsistenter Formprozess ist für die Aufrechterhaltung einer konsistenten Teilequalität und Fertigungseffizienz beim Kunststoffspritzguss unerlässlich. Diese Konsistenz hängt von der Abstimmung von Design-, Material- und Prozessparametern ab. Durch den Einsatz von Parallelentwicklung können Teams von Anfang an zusammenarbeiten und sicherstellen, dass die Designüberlegungen mit den Materialfähigkeiten und Prozessbeschränkungen übereinstimmen. Die Implementierung robuster Qualitätssicherungsprotokolle während der gesamten Produktion ist von entscheidender Bedeutung. Dazu gehören regelmäßige Inspektionen und Tests, um Abweichungen schnell zu identifizieren und zu beheben. Darüber hinaus kann der Einsatz fortschrittlicher Technologien wie prädiktive Analysen und Echtzeitüberwachungssysteme die Prozessstabilität verbessern. Mit diesen Tools können Hersteller potenzielle Probleme erkennen, bevor sie eskalieren, und so einen reibungslosen Betrieb gewährleisten. Auch die kontinuierliche Schulung und Kompetenzentwicklung des Personals spielt eine wichtige Rolle, damit es Prozesse effektiv verwalten und anpassen kann. Zusammen verbessern diese Strategien die allgemeine Robustheit des Formprozesses und tragen zur konsistenten Lieferung hochwertiger Kunststoffteile bei.
Rolle des Concurrent Engineering
Verbesserung der Fertigungseffizienz
Concurrent Engineering steigert die Fertigungseffizienz im Kunststoffspritzguss erheblich, indem es integrierte Arbeitsabläufe fördert und die Markteinführungszeit verkürzt. Durch die Einbindung funktionsübergreifender Teams in einem frühen Stadium der Produktentwicklung können Unternehmen potenzielle Design- und Prozessprobleme proaktiv angehen. Dieser kollaborative Ansatz minimiert kostspielige Neukonstruktionen und stellt sicher, dass alle Aspekte der Produktion von Anfang an aufeinander abgestimmt sind. Concurrent Engineering ermöglicht auch ein besseres Ressourcenmanagement. Durch die Synchronisierung von Aktivitäten zwischen Abteilungen können Hersteller die Planung optimieren, Vorlaufzeiten verkürzen und den Durchsatz erhöhen. Darüber hinaus unterstützt diese Strategie die kontinuierliche Verbesserung, indem sie eine Umgebung fördert, in der Feedback schnell ausgetauscht und integriert wird. Durch die Verwendung von Concurrent-Engineering-Praktiken können sich Unternehmen schnell an Änderungen der Nachfrage oder Spezifikationen anpassen, ohne die Qualität zu beeinträchtigen. Die durch diese Methode erzielten Effizienzgewinne führen nicht nur zu Kosteneinsparungen, sondern verbessern auch den Ruf des Unternehmens in Bezug auf Zuverlässigkeit und Innovation und ziehen letztendlich mehr Kunden an, die an hochwertigen, präzisionsgefertigten Kunststoffteilen interessiert sind.
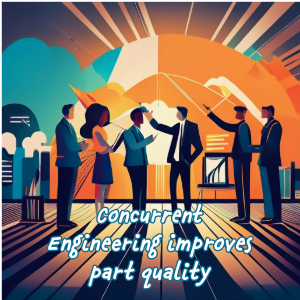
Gewährleistung der Qualitätssicherung
Die Einbeziehung von Concurrent Engineering in den Kunststoffspritzgussprozess ist entscheidend für eine robuste Qualitätssicherung. Dieser Ansatz ermöglicht die frühzeitige Identifizierung und Lösung potenzieller Qualitätsprobleme und verringert so die Wahrscheinlichkeit von Mängeln im Endprodukt. Durch die gleichzeitige Einbindung von Design-, Engineering- und Qualitätssicherungsteams können Unternehmen umfassendere Qualitätskontrollmaßnahmen entwickeln, die jede Produktionsphase abdecken. Diese Zusammenarbeit stellt sicher, dass alle Produktspezifikationen und -standards konsequent eingehalten werden. Concurrent Engineering unterstützt auch die Integration fortschrittlicher Qualitätssicherungstools wie statistische Prozesskontrolle und automatisierte Inspektionssysteme, die die Genauigkeit und Zuverlässigkeit von Qualitätsbewertungen verbessern. Darüber hinaus erleichtern regelmäßige abteilungsübergreifende Überprüfungen die kontinuierliche Überwachung und Verbesserung von Qualitätsprotokollen. Indem Hersteller der Qualitätssicherung im Rahmen von Concurrent Engineering Priorität einräumen, erreichen sie nicht nur eine höhere Konsistenz der Teilequalität, sondern gewinnen auch das Vertrauen ihrer Kunden und etablieren sich letztendlich als führende Anbieter in Sachen Präzision und Zuverlässigkeit in der wettbewerbsintensiven Fertigungslandschaft.
Strategien zur Designvalidierung
Verbesserung der Teilequalitätskonsistenz
Die Verbesserung der Teilequalitätskonsistenz durch Designvalidierung ist in der Kunststoffspritzgussindustrie von entscheidender Bedeutung. Eine effektive Designvalidierung stellt sicher, dass die Teile nicht nur funktional, sondern auch zuverlässig und langlebig sind. Durch die Implementierung von Parallelentwicklung können Teams Designs gemeinsam bewerten und verfeinern, bevor die Produktion beginnt, und so potenzielle Mängel identifizieren, die die Qualität beeinträchtigen könnten. Dieser proaktive Ansatz ermöglicht frühzeitige Anpassungen, minimiert das Risiko von Mängeln und stellt sicher, dass das Endprodukt alle Spezifikationen erfüllt. Fortschrittliche Simulationstools spielen in diesem Prozess eine entscheidende Rolle, da sie es Ingenieuren ermöglichen, Designs unter verschiedenen Bedingungen zu testen und zu validieren, ohne dass physische Prototypen erforderlich sind. Diese Tools helfen dabei, vorherzusagen, wie sich Materialien während des Spritzgusses verhalten, und ermöglichen so die Optimierung der Designparameter. Darüber hinaus sorgen iterative Tests und Feedbackschleifen mit funktionsübergreifenden Teams für kontinuierliche Verbesserungen. Indem sie sich auf die Designvalidierung konzentrieren, können Hersteller eine überragende Teilequalitätskonsistenz erreichen, die anspruchsvollen Erwartungen der Kunden erfüllen und ihre Marktposition stärken.
Innovationen im Kunststoff-Spritzguss
Innovationen im Kunststoffspritzguss revolutionieren die Art und Weise, wie Hersteller an Designvalidierung und Prozessrobustheit herangehen. Ein bedeutender Fortschritt ist der Einsatz von 3D-Drucktechnologien zur schnellen Erstellung detaillierter Prototypen, die schnelle Designiterationen und Validierungen ermöglichen, bevor mit der Serienproduktion begonnen wird. Dies beschleunigt den Entwicklungszyklus und reduziert die mit herkömmlichen Prototyping-Methoden verbundenen Kosten. Darüber hinaus ermöglicht die Integration intelligenter Fertigungstechnologien wie IoT-fähiger Sensoren und maschineller Lernalgorithmen eine Echtzeitüberwachung und -analyse des Formprozesses. Diese Technologien liefern wertvolle Einblicke in die Prozessparameter und ermöglichen sofortige Anpassungen zur Verbesserung der Teilequalitätskonsistenz. Darüber hinaus bietet die Entwicklung neuer Polymermaterialien mit verbesserten Eigenschaften mehr Flexibilität bei Design und Anwendung und erweitert die Möglichkeiten für Innovationen in der Produktentwicklung. Durch die Nutzung dieser Innovationen können Hersteller nicht nur ihre Designvalidierungsstrategien verbessern, sondern auch eine höhere Effizienz und Qualität in ihren Kunststoffspritzgussvorgängen erreichen.