In der sich ständig weiterentwickelnden Landschaft der modernen Metallverarbeitung ist die Laserschneidtechnologie ein Eckpfeiler für die Herstellung hochwertiger Bleche. Diese hochmoderne Methode bietet beispiellose Präzisionsschnitte und ist daher ein unverzichtbares Werkzeug für Fertigungsprofis, die ihre Produktionsprozesse optimieren möchten. Da die Industrie zunehmend nach zuverlässigen und effizienten Lösungen sucht, ist es von entscheidender Bedeutung, die Vorteile des Laserschneidens zu verstehen. Wie kann die Laserschneidtechnologie Ihre Metallverarbeitungstechniken verbessern? In diesem Artikel werden wir uns mit den unzähligen Vorteilen und Anwendungen des Laserschneidens befassen und veranschaulichen, warum es die bevorzugte Wahl für eine hochwertige, präzisionsorientierte Fertigung ist.
Einführung in die Laserschneidtechnologie
Entwicklung der Metallbearbeitungstechniken
Die Entwicklung der Metallbearbeitungstechniken hat im Laufe der Jahrzehnte bedeutende Fortschritte gemacht, wobei die Laserschneidtechnologie eine bahnbrechende Rolle spielte. Traditionelle Methoden wie mechanisches Schneiden und Stanzen weisen Einschränkungen in Bezug auf Präzision und Effizienz auf. Im Gegensatz dazu bietet das Laserschneiden ein hohes Maß an Genauigkeit und die Möglichkeit, komplexe Formen ohne umfangreiche Werkzeuge herzustellen. Dieser Übergang von konventionellen zu modernen Metallbearbeitungsprozessen wird durch die Nachfrage nach höherer Qualität, kürzeren Produktionszeiten und niedrigeren Kosten vorangetrieben. Durch die Integration des Laserschneidens in ihre Arbeitsabläufe können Hersteller hervorragende Ergebnisse bei der Blechbearbeitung erzielen und die strengen Anforderungen der heutigen Industrie erfüllen. Diese Entwicklung verbessert nicht nur die Produktionskapazitäten, sondern eröffnet auch neue Möglichkeiten für innovative Designs und Anwendungen in verschiedenen Sektoren.
Vorteile für die moderne Metallbearbeitung
Die Laserschneidtechnologie bietet der modernen Metallbearbeitung zahlreiche Vorteile. Einer der wichtigsten Vorteile ist die Präzisionsschneidfähigkeit, die minimalen Materialabfall und hochpräzise Schnitte gewährleistet. Diese Präzision führt zu saubereren Kanten und reduziert den Bedarf an sekundären Endbearbeitungsprozessen. Darüber hinaus ist das Laserschneiden äußerst vielseitig und kann problemlos mit verschiedenen Materialien und Stärken umgehen. Diese Anpassungsfähigkeit macht es zur idealen Wahl für vielfältige Anwendungen, von der Automobil- bis zur Luftfahrtindustrie. Darüber hinaus verkürzen die Geschwindigkeit und Effizienz des Laserschneidens die Produktionszeiten und senken die Betriebskosten. Durch den Einsatz der Laserschneidtechnologie können Hersteller ihre Gesamtproduktivität verbessern und durchgängig qualitativ hochwertige Produkte liefern. Das Ergebnis ist ein rationalisierterer Produktionsprozess, der den Anforderungen des heutigen Wettbewerbsmarktes gerecht wird.
Branchenübergreifende Anwendungen
Die Laserschneidtechnologie revolutioniert verschiedene Branchen, indem sie präzise und effiziente Lösungen für die Blechbearbeitung bietet. Im Automobilsektor wird sie verwendet, um komplexe Komponenten mit anspruchsvollen Standards herzustellen und so die Leistung und Sicherheit der Fahrzeuge zu verbessern. Die Luft- und Raumfahrtindustrie verlässt sich auf das Laserschneiden, da es leichte und dennoch langlebige Teile herstellen kann, die für den Flugverkehr unerlässlich sind. Im medizinischen Bereich wird die Technologie zur Herstellung komplexer chirurgischer Instrumente und Geräte eingesetzt, wobei hohe Präzision und Zuverlässigkeit gewährleistet werden. Darüber hinaus profitiert die Elektronikindustrie vom Laserschneiden, indem sie detaillierte und feine Komponenten herstellt, die für moderne Geräte erforderlich sind. Sogar die Bau- und Architekturbranche nutzt das Laserschneiden, um kundenspezifische Elemente und Strukturkomponenten herzustellen. Diese weit verbreitete Anwendbarkeit unterstreicht die Vielseitigkeit und Unverzichtbarkeit der Laserschneidtechnologie bei der Erfüllung der vielfältigen Anforderungen der modernen Fertigung.
Vorteile des Laserschneidens in der Blechbearbeitung
Präzisionsschneiden für hervorragende Ergebnisse
Präzisionsschneiden ist ein Markenzeichen der Laserschneidtechnologie und bietet unübertroffene Genauigkeit und Detailtreue bei der Blechbearbeitung. Herkömmliche Schneidemethoden haben oft Probleme, enge Toleranzen einzuhalten, aber das Laserschneiden ist in dieser Hinsicht unschlagbar. Der fokussierte Laserstrahl kann Metall mit unglaublicher Präzision schneiden, was zu glatten Kanten und komplizierten Designs führt, die nur minimale Nachbearbeitung erfordern. Diese Genauigkeit ist besonders vorteilhaft für Branchen, die hochwertige Komponenten verlangen, wie etwa die Luft- und Raumfahrt, die Automobilindustrie und die Elektronik. Darüber hinaus ermöglicht das Präzisionsschneiden die Erstellung komplexer Geometrien, die mit anderen Methoden schwierig oder unmöglich wären. Durch den Einsatz der Laserschneidtechnologie können Hersteller hervorragende Ergebnisse erzielen und die Gesamtqualität und Leistung ihrer Produkte verbessern. Diese Fähigkeit verbessert nicht nur die Fertigungseffizienz, sondern eröffnet auch neue Wege für Innovation und Design.
Effizienz und Wirtschaftlichkeit
Die Laserschneidtechnologie steigert die Effizienz und Wirtschaftlichkeit in der Blechbearbeitung erheblich. Herkömmliche Schneidemethoden erfordern oft mehrere Schritte und umfangreiche Werkzeuge, was zu höheren Produktionszeiten und -kosten führt. Im Gegensatz dazu rationalisiert das Laserschneiden den Prozess, indem es schnelle, präzise Schnitte in einem einzigen Durchgang liefert. Diese Verkürzung der Produktionszeit führt direkt zu Kosteneinsparungen. Darüber hinaus minimiert das Laserschneiden aufgrund seiner hohen Genauigkeit den Materialabfall, was die mit Rohstoffen verbundenen Kosten weiter senkt. Die Technologie reduziert auch den Bedarf an Wartung und Werkzeugaustausch, was zu niedrigeren Betriebskosten beiträgt. Durch die Verbesserung von Geschwindigkeit und Präzision ermöglicht das Laserschneiden den Herstellern, enge Fristen einzuhalten und wettbewerbsfähige Preise aufrechtzuerhalten. Insgesamt bietet die Integration der Laserschneidtechnologie eine erhebliche Kapitalrendite, indem sie die Produktivität verbessert und die Kosten senkt, was sie zu einem unverzichtbaren Werkzeug für die moderne Metallverarbeitung macht.
Verbesserte Designflexibilität
Die Laserschneidtechnologie bietet beispiellose Designflexibilität bei der Blechbearbeitung. Im Gegensatz zu herkömmlichen Methoden, die oft durch die physikalischen Einschränkungen der Schneidwerkzeuge eingeschränkt sind, wird beim Laserschneiden ein Hochleistungslaserstrahl verwendet, um präzise Schnitte in einer Vielzahl von Materialien und Stärken vorzunehmen. Diese Fähigkeit ermöglicht die Erstellung komplexer und komplizierter Designs, die mit mechanischem Schneiden schwierig oder unmöglich zu erreichen wären. Designer und Ingenieure können mit innovativen Formen und Strukturen experimentieren, ohne sich um die Einschränkungen des Schneidprozesses sorgen zu müssen. Darüber hinaus ermöglicht die einfache Anpassung der Laserschneidparameter schnelles Prototyping und Modifikationen, was das Verfahren ideal für Sonderanfertigungen und Kleinserien macht. Diese Flexibilität fördert nicht nur die Kreativität, sondern stellt auch sicher, dass Hersteller die spezifischen und sich entwickelnden Anforderungen ihrer Kunden erfüllen und so die Produktdifferenzierung und Marktwettbewerbsfähigkeit verbessern können.
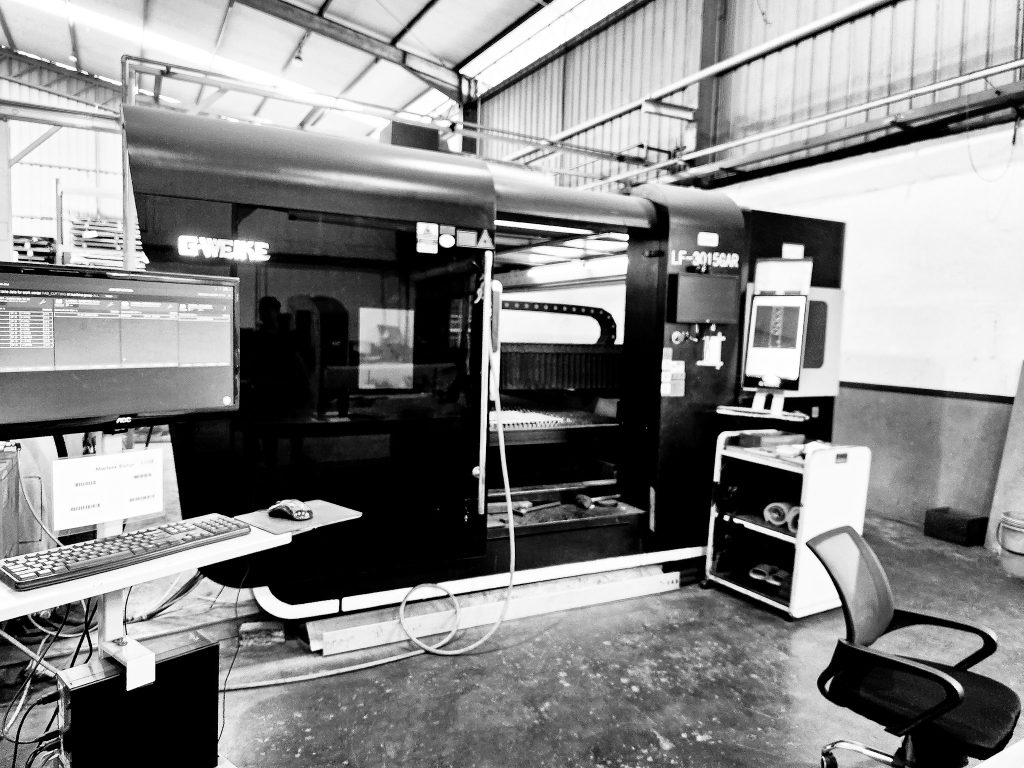
Wichtige Techniken der Metallverarbeitung
Traditionelle Methoden vs. Laserschneiden
Beim Vergleich traditioneller Methoden mit dem Laserschneiden in der Metallverarbeitung sind die Unterschiede deutlich. Traditionelle Schneidtechniken wie mechanisches Sägen, Scheren und Stanzen erfordern häufig physischen Kontakt mit dem Material, was zu Werkzeugverschleiß und einem höheren Risiko von Materialverzerrungen führt. Diese Methoden können auch zeitaufwändig und weniger präzise sein, wodurch sie weniger geeignet sind, komplizierte Designs herzustellen oder enge Toleranzen einzuhalten. Beim Laserschneiden hingegen wird ein fokussierter Laserstrahl verwendet, um eine hohe Präzision ohne direkten Kontakt mit dem Material zu erreichen. Dies führt zu saubereren Schnitten, weniger Materialabfall und einem minimalen Bedarf an Nachbearbeitung. Darüber hinaus kann das Laserschneiden eine Vielzahl von Materialien und Stärken verarbeiten und bietet somit eine größere Vielseitigkeit. Durch die Beseitigung vieler der mit traditionellen Methoden verbundenen Einschränkungen verbessert die Laserschneidtechnologie die Effizienz, Genauigkeit und Gesamtproduktionsqualität in der Blechverarbeitung.
Integration des Laserschneidens in andere Techniken
Die Integration der Laserschneidtechnologie in andere Metallbearbeitungstechniken kann die Produktionskapazitäten und -effizienz erheblich steigern. So ermöglicht die Kombination von Laserschneiden mit CNC-Bearbeitung beispielsweise die Herstellung hochdetaillierter und komplexer Teile, die sowohl Präzisionsschnitte als auch komplizierte Fräsarbeiten erfordern. Ebenso kann die Kombination von Laserschneiden mit Biege- und Umformprozessen die Produktion von Komponenten rationalisieren, die sowohl präzise Schnitte als auch bestimmte Formen erfordern. Durch die Verwendung des Laserschneidens als ersten Schritt können Hersteller saubere und genaue Schnitte erzielen, was nachfolgende Prozesse wie Schweißen, Montage oder Oberflächenbehandlung vereinfacht. Dieser integrierte Ansatz verbessert nicht nur die Qualität des Endprodukts, sondern reduziert auch Produktionszeit und -kosten. Darüber hinaus ermöglicht die Flexibilität des Laserschneidens eine nahtlose Anpassung an verschiedene Fertigungsanforderungen und ist damit eine vielseitige Ergänzung für jeden Fertigungsablauf.
Fallstudien erfolgreicher Implementierungen
Mehrere Fallstudien zeigen die erfolgreiche Implementierung der Laserschneidtechnologie in der Blechbearbeitung. So integrierte beispielsweise ein Automobilhersteller das Laserschneiden in seine Produktionslinie, um präzise Komponenten für Elektrofahrzeuge herzustellen. Die Technologie ermöglichte die Herstellung leichter, hochfester Teile und verbesserte so die Effizienz und Sicherheit der Fahrzeuge. Ein anderer Fall betraf ein Luft- und Raumfahrtunternehmen, das das Laserschneiden zur Herstellung komplexer Teile für Flugzeuge nutzte. Die Präzision und Genauigkeit des Laserschneidens reduzierte den Materialabfall und verbesserte die Leistung kritischer Komponenten. In der Medizinbranche nutzte ein Hersteller das Laserschneiden, um komplizierte chirurgische Instrumente mit unübertroffener Präzision herzustellen und so höchste Qualitäts- und Zuverlässigkeitsstandards zu gewährleisten. Diese Fallstudien zeigen, wie verschiedene Branchen die Laserschneidtechnologie nutzen können, um hervorragende Ergebnisse zu erzielen, die Effizienz zu verbessern und einen Wettbewerbsvorteil auf dem Markt zu erzielen. Die Vielseitigkeit und Effektivität des Laserschneidens machen es zu einem wertvollen Aktivposten in der modernen Metallverarbeitung.
Den richtigen Partner für die Metallverarbeitung auswählen
Beurteilung von Fähigkeiten und Fachwissen
Bei der Auswahl eines Partners für die Metallverarbeitung ist die Bewertung seiner Fähigkeiten und seines Fachwissens von entscheidender Bedeutung. Bewerten Sie zunächst seine Erfahrung mit Laserschneidtechnologie und anderen Metallverarbeitungstechniken. Ein Unternehmen mit nachweislicher Erfolgsbilanz im Bereich Präzisionsschneiden und fortschrittlicher Fertigungsverfahren ist besser gerüstet, um Ihre spezifischen Anforderungen zu erfüllen. Berücksichtigen Sie außerdem sein Leistungsspektrum und ob es mit unterschiedlichen Materialien und Stärken umgehen kann. Es ist auch wichtig, sich sein Portfolio früherer Projekte anzusehen, um seine Fähigkeit einzuschätzen, durchgängig qualitativ hochwertige Ergebnisse zu liefern. Zertifizierungen und die Einhaltung von Industriestandards sind weitere Indikatoren für einen zuverlässigen Partner. Erkundigen Sie sich außerdem nach seinem technischen Support und seinen Wartungsdiensten, um eine reibungslose und unterbrechungsfreie Produktion zu gewährleisten. Durch sorgfältige Bewertung dieser Faktoren können Sie einen Metallverarbeitungspartner auswählen, der nicht nur Ihre aktuellen Anforderungen erfüllt, sondern auch Ihre langfristigen Wachstums- und Innovationsziele unterstützt.
Qualitätssicherung und Zuverlässigkeit
Qualitätssicherung und Zuverlässigkeit sind bei der Auswahl eines Metallverarbeitungspartners von größter Bedeutung. Ein zuverlässiger Partner sollte über robuste Qualitätsmanagementsysteme verfügen, die sicherstellen, dass jedes Produkt strenge Industriestandards erfüllt. Achten Sie auf Zertifizierungen wie ISO 9001, die ein Engagement für Qualität anzeigen. Erkundigen Sie sich außerdem nach ihren Inspektionsprozessen und der Technologie, die sie zur Qualitätskontrolle verwenden. Moderne Werkzeuge wie Laserscanner und Koordinatenmessgeräte (KMGs) können präzise Messungen und die Einhaltung von Spezifikationen gewährleisten. Konsistenz in der Produktion ist ebenfalls ein wichtiger Indikator für Zuverlässigkeit. Prüfen Sie, ob der Partner in der Vergangenheit Projekte pünktlich und innerhalb des Budgets abgeliefert hat. Kundenreferenzen und -bewertungen können Aufschluss über ihre Zuverlässigkeit und Servicequalität geben. Letztendlich wird ein Partner mit starken Qualitätssicherungspraktiken und einer zuverlässigen Erfolgsbilanz sicherstellen, dass Ihre Projekte einwandfrei ausgeführt werden, wodurch Ihre Geschäftsziele unterstützt und Ihr Ruf für Exzellenz gewahrt wird.
Maßgeschneiderte Lösungen für einzigartige Anforderungen
In der Metallverarbeitung gibt es keine Einheitslösung. Es ist wichtig, einen Partner zu finden, der maßgeschneiderte Lösungen für Ihre individuellen Anforderungen bietet. Suchen Sie nach einem Unternehmen, das Flexibilität in Design und Produktion bietet und in der Lage ist, maßgeschneiderte Projekte präzise und effizient abzuwickeln. Dazu gehört die Fähigkeit, mit verschiedenen Materialien, Stärken und komplexen Geometrien zu arbeiten. Ein idealer Partner sollte auch Dienstleistungen wie Prototyping anbieten, um Ihnen zu helfen, Ihre Designs vor der Serienproduktion zu verfeinern und zu testen. Darüber hinaus sollte sein Engineering-Team in der Lage sein, mit Ihnen zusammenzuarbeiten, um Ihre spezifischen Bedürfnisse und Herausforderungen zu verstehen und innovative Lösungen zu bieten, die Ihren Zielen entsprechen. Die Anpassung erstreckt sich auch auf Logistik und Lieferung und stellt sicher, dass Ihre Produkte pünktlich und in einwandfreiem Zustand geliefert werden. Indem Sie einen Partner wählen, der sich durch maßgeschneiderte Lösungen auszeichnet, können Sie hervorragende Ergebnisse erzielen, die Ihr Produktangebot verbessern und Ihre Marktposition stärken.
Zukünftige Trends in der Laserschneidtechnologie
Innovationen im Präzisionsschneiden
Die Zukunft der Laserschneidtechnologie verspricht noch größere Innovationen im Präzisionsschneiden. Eine vielversprechende Entwicklung ist der Einsatz von Ultrakurzpulslasern, die durch Minimierung der wärmebeeinflussten Zonen und Reduzierung der thermischen Verformung eine extrem hohe Präzision erreichen können. Dieser Fortschritt ermöglicht sauberere Schnitte und feinere Details, insbesondere bei empfindlichen und wärmeempfindlichen Materialien. Eine weitere Innovation ist die Integration von künstlicher Intelligenz und maschinellem Lernen, mit der die Schneidparameter in Echtzeit optimiert und so Effizienz und Genauigkeit verbessert werden können. Darüber hinaus verbessern Fortschritte in der Faserlasertechnologie die Schneidgeschwindigkeit und Energieeffizienz, wodurch der Prozess kostengünstiger und umweltfreundlicher wird. Die Einbindung fortschrittlicher Sensoren und Überwachungssysteme verspricht außerdem eine Verbesserung der Qualitätskontrolle und sorgt für konsistente und zuverlässige Ergebnisse. Diese Innovationen werden nicht nur die Möglichkeiten des Laserschneidens verbessern, sondern auch seine Anwendungsmöglichkeiten in verschiedenen Branchen erweitern und neue Maßstäbe für Präzision und Effizienz in der Blechbearbeitung setzen.
Die Rolle der Automatisierung in der Metallverarbeitung
Die Automatisierung wird in der Zukunft der Metallverarbeitung eine entscheidende Rolle spielen, insbesondere bei der Verbesserung der Möglichkeiten der Laserschneidtechnologie. Automatisierte Systeme können sich wiederholende Aufgaben mit hoher Präzision und Geschwindigkeit erledigen und so die Produktionszeiten und Arbeitskosten erheblich reduzieren. So können beispielsweise mit Laserschneidwerkzeugen ausgestattete Roboterarme komplexe Schnitte mit gleichbleibender Genauigkeit durchführen, wodurch menschliche Fehler minimiert und die Effizienz maximiert wird. Darüber hinaus können automatisierte Materialhandhabungssysteme den Arbeitsablauf vom Laden der Rohmaterialien bis zum Entladen der fertigen Produkte optimieren und so einen reibungslosen und kontinuierlichen Betrieb gewährleisten. Die Integration der Automatisierung mit fortschrittlichen Softwarelösungen ermöglicht eine Echtzeitüberwachung und -steuerung, wodurch schnelle Anpassungen und Optimierungen des Schneidprozesses möglich sind. Dies verbessert nicht nur die Produktivität, sondern gewährleistet auch qualitativ hochwertige Ergebnisse. Die sich ständig weiterentwickelnde Automatisierungstechnologie wird die Metallverarbeitung weiter revolutionieren und sie effizienter, zuverlässiger und anpassungsfähiger an die Anforderungen verschiedener Branchen machen.
Nachhaltigkeit und Umweltauswirkungen
Nachhaltigkeit und Umweltauswirkungen werden in der modernen Metallverarbeitung immer wichtiger, und die Laserschneidtechnologie stellt sich dieser Herausforderung. Einer der Hauptvorteile des Laserschneidens ist die Fähigkeit, durch präzises Schneiden Materialabfall zu reduzieren, was zu einer effizienteren Nutzung der Rohstoffe führt. Diese Präzision schont nicht nur Ressourcen, sondern verringert auch die Menge an Altmetall, die auf Mülldeponien landet. Darüber hinaus haben Fortschritte in der Faserlasertechnologie das Laserschneiden energieeffizienter gemacht, wodurch der gesamte CO2-Fußabdruck des Herstellungsprozesses reduziert wird. Die Verwendung umweltfreundlicher Gase und Kühlsysteme minimiert die Umweltbelastung zusätzlich. Darüber hinaus steht die Integration wiederverwertbarer Materialien und nachhaltiger Praktiken in Produktionsabläufe im Einklang mit den weltweiten Bemühungen zur Förderung einer umweltfreundlichen Fertigung. Durch die Einführung dieser Innovationen kann die Metallverarbeitungsindustrie zur ökologischen Nachhaltigkeit beitragen und gleichzeitig hohe Qualitäts- und Effizienzstandards aufrechterhalten.