In der komplexen Welt der Fertigung, insbesondere beim Spritzguss, kann das Vorhandensein von Einfallstellen die ästhetische und funktionale Qualität eines Produkts erheblich beeinträchtigen. Eine Einfallstelle, die oft als kosmetischer Defekt wahrgenommen wird, tritt auf, wenn die Oberfläche des Kunststoffteils aufgrund ungleichmäßiger Abkühlung oder unzureichenden Packdrucks während des Formprozesses eingesunkene Bereiche aufweist. Diese Einfallstellen beeinträchtigen nicht nur die Optik des Endprodukts, sondern können auch seine strukturelle Integrität beeinträchtigen, was zu potenziellen Leistungsproblemen führen kann. Daher ist es für Hersteller, die hochwertige, langlebige Produkte liefern möchten, von entscheidender Bedeutung, zu verstehen, was Einfallstellen in Kunststoff verursacht und wie man Einfallstellen beim Spritzguss vermeidet. Dieser Artikel befasst sich mit der Bedeutung der Minimierung von Einfallstellen und hebt innovative Strategien und Techniken hervor, um sowohl das Erscheinungsbild als auch die Haltbarkeit Ihrer Produkte zu verbessern.
Einfallstellen beim Spritzgießen verstehen
Was sind Einfallstellen in Kunststoff?
Eine Einfallstelle in Kunststoff ist eine subtile Vertiefung oder Delle, die auf der Oberfläche eines Spritzgussteils auftritt. Sie entsteht normalerweise durch die unterschiedliche Schrumpfung von Kunststoffmaterialien beim Abkühlen und Erstarren in der Form. Diese Einfallstellen sind häufig das Ergebnis unzureichenden Stopfdrucks, ungleichmäßiger Abkühlung oder dicker Wandabschnitte, die eine gleichmäßige Aushärtung verhindern. Der Defekt beeinträchtigt nicht nur die Ästhetik, sondern kann auch auf zugrunde liegende Probleme beim Formungsprozess selbst hinweisen.
Dies kann zu einer verringerten Teilefestigkeit und einer beeinträchtigten Leistung führen. Das Erkennen des Vorhandenseins und der Auswirkungen von Einfallstellen ist für Hersteller, die die Qualität und Haltbarkeit ihrer Produkte aufrechterhalten möchten, von entscheidender Bedeutung. Durch das Verständnis der Ursachen von Einfallstellen können Unternehmen proaktive Maßnahmen ergreifen, um ihre Spritzgusstechniken zu verfeinern und sicherzustellen, dass jedes Produkt den höchsten Qualitätsstandards entspricht.
Einfallstellen – Ursachen und Auswirkungen
Die Ursachen für Einfallstellen beim Spritzgießen sind hauptsächlich auf drei Faktoren zurückzuführen: unzureichender Nachdruck, ungleichmäßige Abkühlgeschwindigkeiten und ungleichmäßige Wandstärke. Unzureichender Nachdruck während des Formprozesses kann zu unzureichender Materialfüllung führen, was zu eingesunkenen Bereichen auf der Teileoberfläche führt. Ungleichmäßige Abkühlung tritt häufig auf, wenn Teile unterschiedliche Dicken aufweisen, wodurch einige Abschnitte schneller erstarren als andere. Ungleichmäßige Wandstärken verschlimmern dieses Problem, indem sie beim Abkühlen des Kunststoffs zu unterschiedlicher Schrumpfung führen.
Die Auswirkungen von Einfallstellen gehen über die Ästhetik hinaus und beeinträchtigen möglicherweise die strukturelle Integrität des Teils. Dies kann zu verringerter Festigkeit und Haltbarkeit führen, wodurch das Produkt unter Belastung anfällig für Fehler wird. Das Verständnis dieser Ursachen hilft nicht nur bei der Identifizierung potenzieller Schwachstellen im Herstellungsprozess, sondern unterstützt auch die Umsetzung von Korrekturmaßnahmen. Durch die Beseitigung dieser Grundursachen können Hersteller die Produktqualität verbessern und eine gleichbleibende Leistung sicherstellen.
Auswirkungen auf das Erscheinungsbild des Produkts
Einfallstellen beeinträchtigen die Optik von Spritzgussprodukten erheblich. Diese Unvollkommenheiten erzeugen sichtbare Dellen oder Vertiefungen auf der Oberfläche und beeinträchtigen die oft gewünschte glatte, polierte Oberfläche. Dies kann besonders nachteilig für verbraucherorientierte Produkte sein, bei denen die Ästhetik eine entscheidende Rolle bei der Kaufentscheidung spielt. Ein schlechtes Erscheinungsbild aufgrund von Einfallstellen kann dazu führen, dass Kunden das Produkt als minderwertig wahrnehmen, was sich negativ auf den Ruf der Marke und die Kundenzufriedenheit auswirkt.
Darüber hinaus erfüllen Produkte mit sichtbaren Einfallstellen möglicherweise nicht die Industriestandards für ästhetische Qualität, was zu höheren Ausschussraten und Kosten für Nacharbeit oder Ausschuss führt. In wettbewerbsintensiven Märkten ist die Beibehaltung eines makellosen Erscheinungsbilds unerlässlich, um Produkte von der Masse abzuheben und den Markenwert aufrechtzuerhalten. Wenn Hersteller wissen, wie sie Einfallstellen beim Spritzgießen vermeiden können, können sie sicherstellen, dass ihre Produkte nicht nur effektiv funktionieren, sondern auch ein ansprechendes Erscheinungsbild aufweisen, das den Erwartungen der Kunden entspricht.
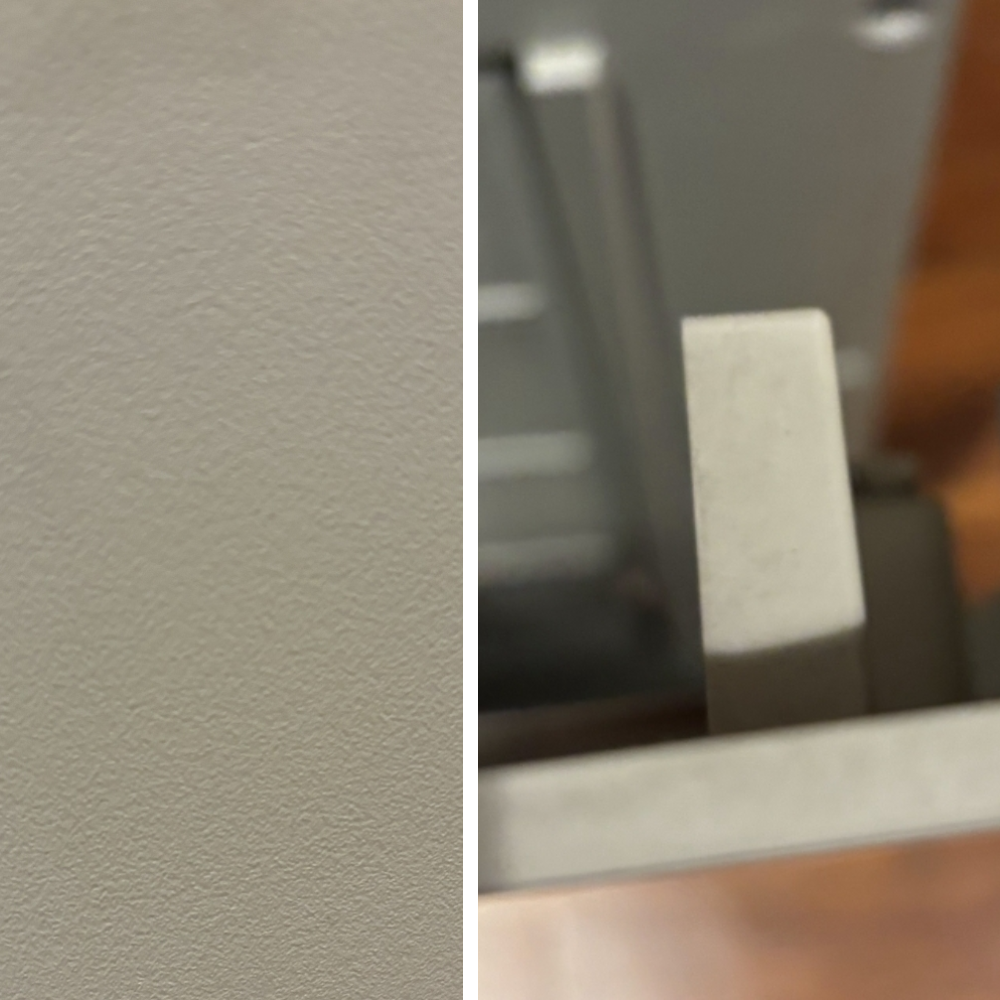
Strategien zur Vermeidung von Einfallstellen
Optimierung der Spritzgussparameter
Um Einfallstellen beim Spritzgießen zu vermeiden, müssen die wichtigsten Formparameter optimiert werden. Ein kritischer Faktor ist der Nachdruck. Wenn während der Nachdruckphase ein ausreichender Druck gewährleistet wird, kann dies dazu beitragen, die Formkavität vollständig auszufüllen und so die Wahrscheinlichkeit von Einfallstellen zu verringern. Eine weitere wichtige Strategie ist die Anpassung der Abkühlzeit. Indem Hersteller ausreichend Zeit für eine gleichmäßige Abkühlung einplanen, können sie die unterschiedliche Schrumpfung, die zu Einfallstellen führt, minimieren.
Darüber hinaus ist die Temperaturkontrolle von entscheidender Bedeutung. Die Aufrechterhaltung einer konstanten Formtemperatur trägt zu einer gleichmäßigen Verfestigung bei und kann Oberflächenfehler verhindern. Ein weiterer Aspekt ist die Einspritzgeschwindigkeit; eine langsamere Einspritzgeschwindigkeit kann Turbulenzen verringern und eine gleichmäßigere Materialverteilung innerhalb der Form gewährleisten. Durch sorgfältige Analyse und Anpassung dieser Parameter können Hersteller das Auftreten von Einfallstellen erheblich reduzieren. Dieser Ansatz verbessert nicht nur die visuelle Qualität des Produkts, sondern stärkt auch seine strukturelle Integrität und gewährleistet einen hohen Leistungsstandard.
Materialauswahl und Designüberlegungen
Die Materialauswahl spielt eine entscheidende Rolle bei der Minimierung von Einfallstellen in Kunststoffprodukten. Die Wahl von Materialien mit geringerer Schrumpfrate kann die Bildung von Einfallstellen erheblich reduzieren. Thermoplaste mit gleichbleibenden Schrumpfeigenschaften sorgen für einen gleichmäßigeren Abkühlungsprozess und verringern so die Wahrscheinlichkeit von Oberflächenfehlern. Darüber hinaus sind Designüberlegungen von entscheidender Bedeutung.
Gleichmäßige Wandstärken sollten vorrangig behandelt werden, um unterschiedliche Abkühlungsprozesse zu vermeiden, die häufig zu Einfallstellen führen. Auch der Einbau von Rippen oder Strukturstützen kann helfen, die Dimensionsstabilität zu erhalten und die Dicke dickerer Abschnitte zu reduzieren, ohne die Festigkeit zu beeinträchtigen. Darüber hinaus ermöglicht der Einsatz von CAD-Tools (Computer-Aided Design) eine präzise Modellierung von Formströmungs- und Abkühlungsmustern, wodurch potenzielle Einfallstellenprobleme vor Produktionsbeginn vorhergesagt und behoben werden können.
Durch Konzentration auf diese Material- und Designstrategien können Hersteller Einfallstellen effektiv reduzieren und so sowohl die ästhetische als auch die funktionale Qualität ihrer Spritzgussprodukte verbessern.
Fortschrittliche Techniken zur Minimierung von Einfallstellen
Durch den Einsatz moderner Techniken lässt sich das Risiko von Einfallstellen in Spritzgussprodukten weiter verringern. Eine dieser Techniken ist das gasunterstützte Spritzgießen, das dabei hilft, einen gleichmäßigen Druck aufrechtzuerhalten und dicke Materialbereiche zu reduzieren, die anfällig für Einfallstellen sind.
Ein anderer Ansatz ist die Anwendung einer sequentiellen Ventilsteuerung, die die Steuerung des Materialflusses in verschiedene Abschnitte der Form ermöglicht, wodurch eine gleichmäßige Füllung sichergestellt und Einfallstellen in komplexen Designs minimiert werden. Darüber hinaus kann der Einsatz konturnaher Kühlkanäle innerhalb der Form die Kühlleistung drastisch verbessern, was zu einer gleichmäßigeren Verfestigung des Kunststoffs führt und das Risiko von Einfallstellen verringert.
Der Einsatz von Simulationssoftware kann auch Einblicke in potenzielle Einfallstellenbereiche liefern und so präventive Designanpassungen ermöglichen. Durch den Einsatz dieser fortschrittlichen Methoden können Hersteller die Präzision in Formprozessen verbessern und so sicherstellen, dass ihre Produkte hohe Qualitäts- und Ästhetikstandards erfüllen, ohne die üblichen Probleme mit Einfallstellen.
Bedeutung der Minimierung von Einfallstellen
Verbesserung der optischen Attraktivität und Marktfähigkeit
Die Minimierung von Einfallstellen ist entscheidend, um die optische Attraktivität und Marktfähigkeit von Spritzgussprodukten zu verbessern. Eine makellose Oberflächenbeschaffenheit trägt erheblich zum wahrgenommenen Wert eines Produkts bei und macht es für Verbraucher in wettbewerbsintensiven Märkten attraktiver. Produkte, die ein hochwertiges Erscheinungsbild ohne sichtbare Mängel wie Einfallstellen aufweisen, erregen eher die Aufmerksamkeit der Verbraucher und schaffen Markenvertrauen. Diese wahrgenommene Qualität kann Kaufentscheidungen direkt beeinflussen, insbesondere in Branchen, in denen Ästhetik eine wesentliche Rolle spielt, wie Unterhaltungselektronik, Automobilbau und Haushaltswaren.
Darüber hinaus erzielen optisch ansprechende Produkte oft höhere Preise, was die Rentabilität steigert. Indem Hersteller sich auf die Reduzierung von Einfallstellen konzentrieren, verbessern sie nicht nur die ästhetische Qualität ihrer Produkte, sondern steigern auch ihre Wettbewerbsfähigkeit auf dem Markt. Dieser Fokus auf Qualität trägt dazu bei, einen starken Markenruf aufzubauen, die Kundentreue zu fördern und die Marktreichweite zu erweitern. Letztlich unterstützt die Minimierung von Einfallstellen den langfristigen Geschäftserfolg, indem das Produktangebot an die Erwartungen der Verbraucher angepasst wird.
Sicherstellung der Haltbarkeit und Qualität der Produkte
Die Minimierung von Einfallstellen ist ein wesentlicher Bestandteil der Gewährleistung der Haltbarkeit und Qualität von Spritzgussprodukten. Einfallstellen werden zwar oft als kosmetisches Problem wahrgenommen, können jedoch auf tiefere Probleme im Zusammenhang mit der Materialverteilung und der strukturellen Integrität hinweisen. Diese Defekte können zu Schwachstellen im Produkt führen und es im Laufe der Zeit anfälliger für Belastungen und Verschleiß machen. Diese Anfälligkeit kann zu vorzeitigem Versagen führen und die Lebensdauer und Leistung des Produkts beeinträchtigen. Durch die Beseitigung der Einfallstellenursachen können Hersteller die Materialkonsistenz und strukturelle Robustheit ihrer Produkte verbessern.
Diese Verbesserung stellt nicht nur sicher, dass die Produkte strenge Qualitätsstandards erfüllen, sondern verringert auch die Wahrscheinlichkeit von Rücksendungen und Garantieansprüchen. Darüber hinaus trägt die Herstellung langlebiger Produkte dazu bei, die Glaubwürdigkeit der Marke zu wahren und das Vertrauen und die Zufriedenheit der Kunden zu stärken. Indem sie Strategien zur Vermeidung von Einfallstellen priorisieren, können Hersteller qualitativ hochwertige, zuverlässige Produkte liefern, die die Erwartungen der Verbraucher erfüllen und den Test der Zeit bestehen, und so den Ruf ihrer Marke und ihre Marktposition sichern.
Aufbau von Kundenvertrauen und Markenreputation
Die Minimierung von Einfallstellen ist für die Vertrauensbildung beim Kunden und die Verbesserung des Markenrufs von entscheidender Bedeutung. Im heutigen wettbewerbsintensiven Markt erwarten Verbraucher qualitativ hochwertige Produkte, die nicht nur gut funktionieren, sondern auch tadellos aussehen. Sichtbare Mängel wie Einfallstellen können das Vertrauen der Verbraucher untergraben, da diese Mängel als Anzeichen für mangelnde Detailgenauigkeit oder minderwertige Produktionsprozesse wahrgenommen werden können. Durch die konsequente Lieferung von Produkten ohne Einfallstellendefekte demonstrieren Hersteller ihr Engagement für Qualität und Präzision und fördern das Vertrauen ihrer Kunden.
Dieses Vertrauen führt zu Markentreue, da zufriedene Kunden eher wiederkommen und die Marke weiterempfehlen. Darüber hinaus kann sich eine Marke durch den Ruf, qualitativ hochwertige, fehlerfreie Produkte herzustellen, von der Konkurrenz abheben und Türen zu neuen Märkten und Möglichkeiten öffnen. Letztlich trägt die Minimierung von Einfallstellen zu einem positiven Markenimage bei und unterstützt den langfristigen Erfolg und das Wachstum in der Branche.
Lesen Sie auch: Einfallstellen beim Spritzgießen verstehen