In this article, we explore what is CMT Welding (Cold Metal Transfer) and MIG Welding (Metal Inert Gas)and how it is used in metal fabrication process.
First – What is Welding?
Welding can be defined as a metal fabrication process that utilises high heat to melt and join materials, commonly metals or thermoplastics together. In other words, it is basically a joining process that involve the manipulation of material phase from solid to liquid and back to solid. Welding technology has long been and is constantly evolving. It is no surprise that nowadays there are numerous welding methods currently being applied in the industry.
MIG Welding in Metal Fabrication
In MIG Welding, the workpiece and the welding gun are part of the same electrical circuit. The electrode wire is automatically fed through the gun. Current instantaneously flow the moment the electrode wire touches the workpiece. As the electrode wire rapidly heats up due to the high amperage, the tip of the solid electrode begins to melt into metal droplets.
The metal droplets would then separate from the electrode forming an electrical arc that is around 3500°C which heats up and melts the workpiece forming a molten puddle. This enable the metal droplets to fuse with the base metal. As the temperature decreases, the molten puddle of base material and metal droplets solidify, forming weld beads. This process continuously repeats itself several times each second until the seams are fully welded.
CMT Welding in Metal Fabrication
The differences in CMT and MIG welding process is fairly subtle with the exception in the way the electrode wire is fed.
In contrast to continuously feeding the electrode wire into the molten puddle (MIG), in CMT, the electrode wire is instantly retracted the moment current flows. This provides the welding some time to cool before each drop is placed. In doing so, this process leaves a smooth weld that is way stronger than the hotter weld (MIG).
We explore the differences of MIG Welding (Metal Inert Gas) and CMT Welding (Cold Metal Transfer) and how it is used in metal fabrication process.
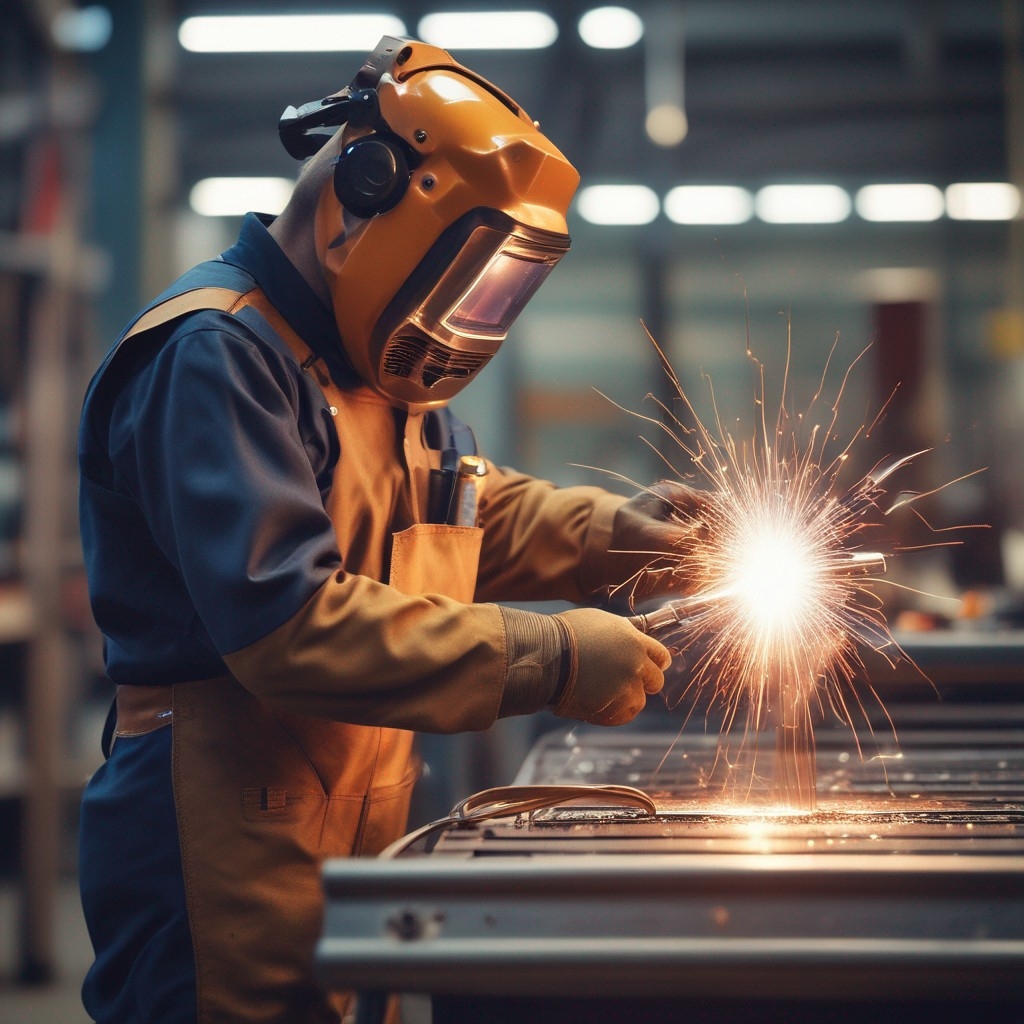
The Pros & Cons of CMT Welding
Pros:
- Lower Heat Input: CMT welding is characterized by its significantly lower heat input compared to traditional MIG welding. This results in minimal warping and distortion of the metal, which is particularly beneficial when working with thin sheets.
- High-Quality Welds: The process allows for very stable and spatter-free welds, leading to cleaner finishes and reducing the need for post-weld cleanup.
- Versatility: CMT can be used with a variety of materials, including aluminum, stainless steel, and other alloys, which are commonly used in sheet metal fabrication.
- Automation Compatibility: CMT is well-suited for automation, enhancing precision and consistency in large-scale production settings.
Cons:
- Cost: The equipment for CMT is generally more expensive than traditional MIG setups. This can be a barrier for smaller shops or those with limited budgets.
- Complexity: The technology and technique behind CMT welding are more complex, requiring skilled operators who are trained specifically in this method.
- Speed: While very precise, CMT can be slower than other welding methods, potentially impacting productivity in time-sensitive projects.
The Pros & Cons of MIG Welding
Pros:
- Speed: MIG welding is faster than many other welding techniques, including CMT, making it ideal for projects that require quick turnaround.
- Ease of Use: It is relatively easy to learn and master MIG welding, which makes it a popular choice in both professional and amateur settings.
- Cost-Effective: The equipment and consumables for MIG welding are generally less expensive than those for more advanced techniques like CMT.
- Versatility: MIG welding can be used on a wide range of materials and thicknesses, making it a versatile option for many types of projects.
Cons:
- Higher Heat Input: MIG welding generates more heat, which can lead to more distortion and warping, especially in thinner materials.
- Spatter: The process can produce spatter, requiring additional cleanup and finishing work after welding.
- Less Precision in Automated Settings: While MIG can be automated, it generally does not reach the same level of precision and control as CMT in automated applications.
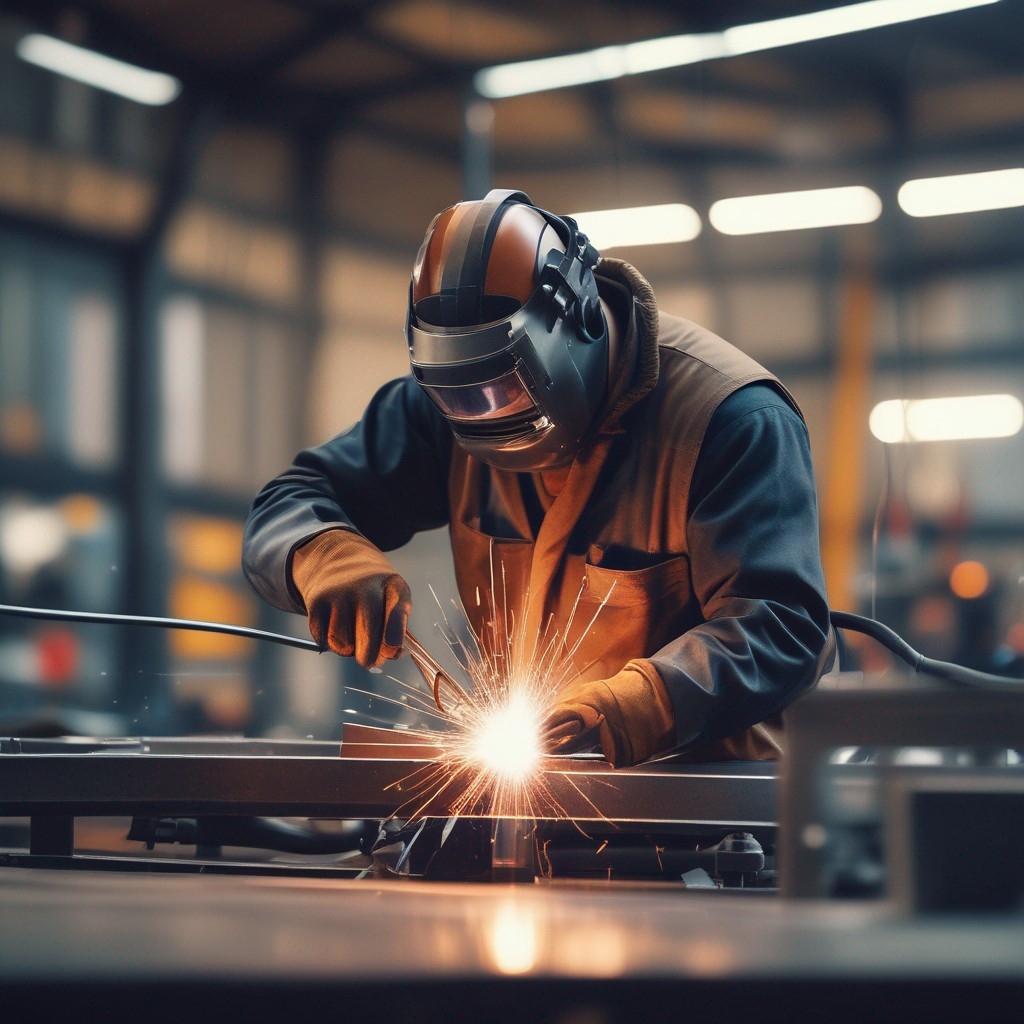
Conclusion
Choosing between CMT and MIG welding in sheet metal fabrication largely depends on the specific needs of the project. If precision, minimal distortion, and clean welds are priorities, CMT might be the better choice, despite its higher cost and complexity. On the other hand, if speed, cost-effectiveness, and ease of use are more critical, MIG welding would likely be more suitable. Each technique offers unique benefits and drawbacks, and the optimal choice will vary by application, material type, thickness, and budget constraints.