The automotive industry is undergoing a dramatic transformation, with electronic components becoming integral to vehicle functionality. From infotainment systems to safety mechanisms and the critical components of electric vehicles (EVs), automotive electronics are at the core of this revolution.
The manufacturing of these components requires precision, reliability, and cutting-edge technology, which makes Electronics Manufacturing Services (EMS) providers indispensable partners in this space. This article explores the role of EMS in automotive electronics, the challenges manufacturers face, and the critical trends shaping the future of automotive manufacturing.
The Role of EMS in Automotive Electronics
Electronics Manufacturing Services (EMS) refer to companies that offer comprehensive manufacturing solutions, including design, assembly, testing, and logistics for electronic components and systems.
In the automotive sector, EMS providers play a vital role in producing the electronics that power modern vehicles. These electronics are no longer limited to traditional vehicle features but extend to advanced technologies such as electric drivetrains, infotainment systems, autonomous driving sensors, and much more.
EMS companies in the automotive space are responsible for the full life cycle of electronic components, from initial prototyping and design to large-scale production. Their role is crucial in ensuring that automotive electronics meet stringent reliability, safety, and regulatory standards.
The diversity of automotive electronics is vast, encompassing systems such as:
Infotainment and Connectivity: This includes navigation, audio, and video systems, as well as connectivity technologies like Bluetooth and Wi-Fi.
Safety Systems: Modern vehicles rely on advanced sensors, cameras, and radar systems for features like Adaptive Cruise Control, Emergency Braking Systems, and Lane Keep Assist.
Electric Power Management: For electric and hybrid vehicles, EMS companies provide battery management systems (BMS), power inverters, and charging infrastructure components.
Autonomous Systems: As the industry moves toward autonomous vehicles, EMS providers are increasingly focused on producing complex sensors, AI-driven processing systems, and communication networks.
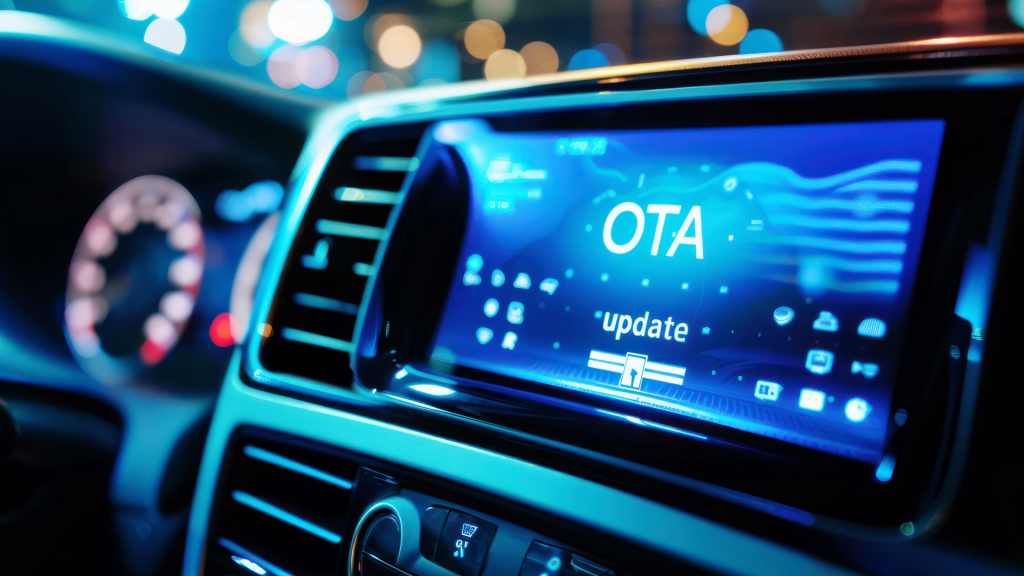
Key Considerations in Choosing an EMS Provider
Choosing the right EMS partner is critical for automotive companies to meet their production and quality standards. Several factors must be considered when selecting an EMS provider:
Certifications and Standards: The automotive industry is highly regulated, and EMS providers must adhere to strict standards such as ISO/TS 16949 and IATF 16949, which govern quality management systems for automotive suppliers. These certifications ensure that EMS providers meet industry-specific requirements for reliability, safety, and process control.
Technology and Capabilities: The increasing complexity of automotive electronics demands EMS providers with advanced capabilities. Surface Mount Technology (SMT) is essential for efficiently assembling miniaturized electronic components. Moreover, manufacturers must have robust testing facilities to ensure their products meet high standards for durability, performance, and safety.
Supply Chain Management: Effective logistics and inventory management are critical in the automotive electronics supply chain. EMS providers must be able to source components globally, manage inventory, and ensure just-in-time delivery to meet the demands of automotive manufacturers.
What Specific Challenges Do Automotive Electronics Manufacturers Face in Meeting Industry Standards?
Automotive electronics manufacturers face numerous challenges in maintaining the high standards required by the industry. These challenges stem from the complexity of electronic systems, labor and cost factors, and regulatory compliance:
Complexity of Automotive Electronics: Modern vehicles contain a wide range of electronic systems that must work together seamlessly. From infotainment systems to safety features like airbags and collision avoidance systems, the complexity of automotive electronics is growing. Manufacturers must design and produce components that are not only reliable but also capable of withstanding extreme conditions, such as temperature fluctuations, vibrations, and moisture.
Labor and Cost Factors: Labor costs can significantly impact the cost structure for automotive electronics manufacturers. With increasing demand for advanced electronics, companies must ensure they have access to a skilled workforce capable of managing sophisticated technologies. Geopolitical factors, such as trade tariffs and labor shortages, can also impact manufacturing costs.
Regulatory Compliance: Automotive manufacturers must comply with various global safety, environmental, and emissions standards. In addition to local and regional regulations, global standards like ISO 26262 (functional safety for automotive systems) must be adhered to. EMS providers play a key role in ensuring that components meet these stringent requirements.
The Impact of Increasing Electronic Content Per Car
The increasing electronic content per car is one of the most significant trends in the automotive industry today. With each new model, the number of electronic components in a vehicle is rising. Infotainment systems, driver assistance systems, and electric powertrains are becoming increasingly sophisticated, leading to higher levels of integration and complexity.
Complexity in Design and Manufacturing: The shift towards more electronic systems means that manufacturers must manage the integration of a larger number of components in smaller spaces. The design and production of electronic systems require advanced engineering and high-precision manufacturing techniques. As the number of components increases, so does the challenge of ensuring compatibility and reliability across systems.
Quality Control and Testing: With more electronics in a vehicle, ensuring their quality and reliability becomes more challenging. Manufacturers must invest in comprehensive testing and validation processes to ensure that all components meet the rigorous safety and performance standards expected in the automotive industry. This includes environmental testing, such as exposure to high temperatures and humidity, and vibration testing to simulate real-world driving conditions.
Supply Chain Pressure: As the demand for electronic components increases, so does the pressure on the supply chain. Manufacturers must ensure they have a reliable and efficient supply chain to source the components required for production. This involves working closely with suppliers, managing inventory, and ensuring that parts arrive on time to avoid delays in production.
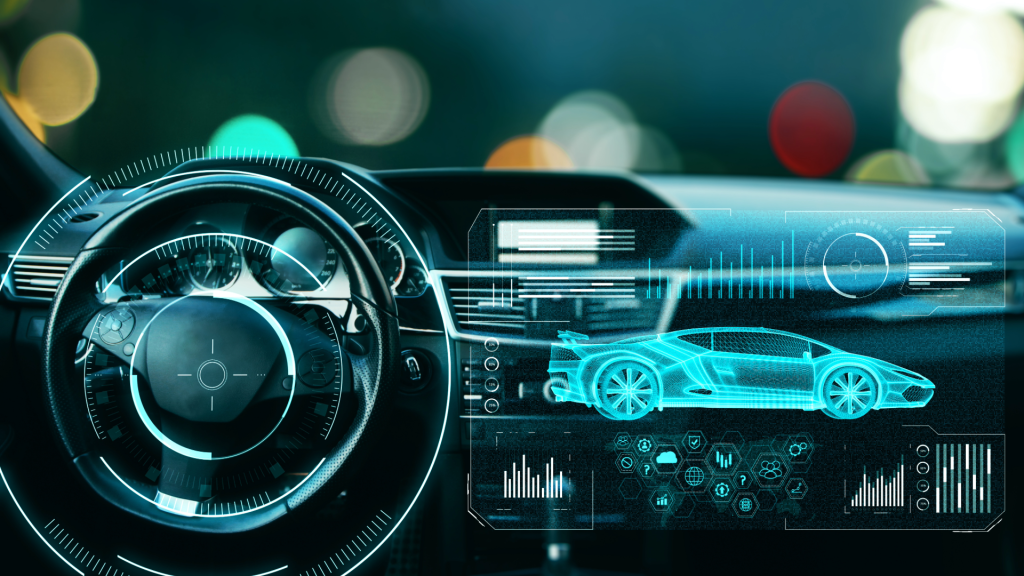
How Electric Vehicles (EVs) Increase the Need for Strong Automotive Electronics Manufacturing Services
The rapid growth of the electric vehicle market is another major driver for the increasing demand for automotive electronics. EVs require specialized electronics to manage the powertrain, battery systems, and charging infrastructure.
EMS providers must meet the specific needs of EV manufacturers, including:
Increased Demand for Specialized Components: The battery management system (BMS) is critical in electric vehicles, as it monitors the health and performance of the battery. Additionally, power inverters and electric drivetrains rely on advanced electronic components to manage energy distribution and conversion. EMS providers need to develop and manufacture these highly specialized components with precision and reliability.
Challenges in Integration and Safety: EVs have more complex electronics than traditional vehicles, as every aspect of the powertrain relies on electronic components. EMS providers must ensure that all electronic components are integrated correctly and work seamlessly with other systems in the vehicle. This requires collaboration across multiple design teams and careful testing to ensure that all parts are safe and compatible.
Sustainability and Efficiency: As EV adoption increases, manufacturers must balance the demand for high-quality, efficient electronics with the need for sustainable practices. EMS providers play a key role in developing energy-efficient components and reducing the environmental impact of manufacturing processes.
The Role of Rapid Prototyping in Automotive Electronics Manufacturing
Rapid prototyping has become a critical component of the automotive electronics manufacturing process. As the industry becomes more competitive, manufacturers must bring new products to market quickly. Rapid prototyping enables EMS providers to design and test prototypes quickly, which accelerates product development and reduces time-to-market.
Accelerating Development: Rapid prototyping allows automotive manufacturers to test new designs and make adjustments before committing to full-scale production. This process helps identify potential issues early in the development cycle, reducing the risk of costly errors during mass production.
Design Flexibility: Prototyping provides flexibility in design, enabling manufacturers to test multiple design iterations quickly. This is especially important for complex systems like automotive electronics, where design changes can have significant impacts on functionality and performance.
Cost Efficiency: By reducing the time spent on design and testing, rapid prototyping helps reduce development costs. It also minimizes the risk of costly mistakes during mass production, which can result from incorrect assumptions made during the design phase.
Trends Shaping the Future of Automotive Electronics EMS
Several trends are influencing the future of automotive electronics manufacturing services, including:
Electrification: The shift toward electric powertrains is creating new demand for specialized automotive electronics, from battery management systems to power conversion and charging infrastructure. EMS providers must adapt to these needs by investing in new technologies and processes.
Connectivity and Infotainment: The rise of connected vehicles is driving the demand for advanced infotainment systems, telematics, and driver assistance systems (ADAS). EMS providers must stay ahead of technological advancements to meet the needs of automakers and consumers.
Sustainability: The automotive industry is increasingly focused on sustainability, with manufacturers looking for ways to reduce emissions and environmental impact. EMS providers will need to embrace sustainable practices in manufacturing processes and component design.
Industry 4.0 and Automation: The advent of Industry 4.0 technologies, including automation, AI, and robotics, is transforming the automotive electronics manufacturing landscape. EMS providers must leverage these technologies to increase efficiency, reduce costs, and maintain high standards of quality.
Final thoughts
As automotive electronics continue to evolve, the role of Electronics Manufacturing Services becomes increasingly vital. EMS providers are responsible for producing the high-quality, reliable, and cutting-edge electronic components that are transforming the automotive industry.
From the growing complexity of electronics per vehicle to the rise of electric and autonomous vehicles, EMS providers must meet the challenges of an ever-changing industry.
By embracing new technologies, standards, and best practices, EMS providers will continue to support automotive manufacturers in delivering safe, efficient, and innovative vehicles to the market.