In the intricate world of electronics manufacturing, mastering the art of box build assembly is essential for producing high-quality, reliable products. This process involves more than just assembling components; it integrates various stages of the product assembly, including enclosure fabrication, cable routing, and system testing. For electronics manufacturers, understanding the nuances of the box build process is crucial for ensuring efficiency and meeting client specifications. We’ll delve into the key considerations and benefits of box build assembly, providing insights into how custom box build solutions can enhance your product development process while highlighting success stories that demonstrate these assembly services’ capabilities.
Understanding Box Build Assembly
Defining the Box Build Process
Box build assembly refers to the comprehensive process of final product assembly in electronics manufacturing. It encompasses several steps beyond merely attaching components to a printed circuit board (PCB). The process typically includes enclosure assembly, cable routing, wire harness installation, and system-level functional testing. It is essential to consider each element, from the selection of materials for enclosures to the precision of cable management, to ensure that the final product meets specified standards and functions as intended. This process also involves configuring sub-assemblies, integrating components, and managing the final packaging. The complexity of a box build can vary significantly depending on the product’s design and functionality requirements. Understanding these intricacies allows manufacturers to streamline production, reduce errors, and maintain quality control, ultimately leading to successful product launches and satisfied clients.
Importance in Electronics Manufacturing
Box build assembly plays a critical role in electronics manufacturing by ensuring that products are constructed accurately and efficiently. This process is pivotal for integrating various electronic components into a cohesive system, which is essential for meeting the functional and aesthetic requirements of modern electronic devices. The precision and expertise involved in box build assembly can significantly affect product performance, reliability, and longevity. Properly executed, it minimizes the risk of defects and enhances the product’s market readiness. Moreover, this assembly process supports rapid prototyping and scalable production, which are crucial for staying competitive in the fast-paced electronics industry. It also allows manufacturers to tailor solutions to specific client needs, providing the flexibility necessary to accommodate diverse product specifications. By mastering box build assembly, manufacturers can improve their production efficiency, reduce lead times, and deliver superior products to market, thereby strengthening their competitive position.
Critical Considerations for Manufacturers
Custom Box Build Challenges
Navigating the complexities of custom box build assembly presents several challenges for manufacturers. One significant hurdle is managing the diverse requirements of various projects, which often involve unique specifications and components. The need for precise customization can complicate supply chain logistics, as sourcing specific parts may require coordination with multiple suppliers. Additionally, maintaining quality control throughout the process is crucial, as even minor deviations can affect product performance and reliability. Manufacturers must also consider the integration of new technologies and compliance with industry standards, which can introduce further intricacies.
Another challenge is ensuring effective communication and collaboration across teams, particularly when dealing with complex or large-scale projects. This requires robust project management and clear documentation to prevent misalignments or delays. Addressing these challenges demands a strategic approach, leveraging expertise in design, engineering, and production to deliver high-quality, customized solutions that meet client expectations while maintaining efficiency.
Ensuring Quality in Product Assembly
Ensuring quality in product assembly is a cornerstone of successful electronics manufacturing. To achieve high standards, manufacturers must implement rigorous quality control measures at every stage of the box build process. This begins with the selection of reliable materials and components, ensuring they meet the required specifications and industry standards. During assembly, precise alignment and secure connections are critical to prevent functional failures. Employing advanced testing methods, such as automated optical inspection (AOI) and in-circuit testing (ICT), helps identify defects early, reducing the risk of costly rework. Additionally, thorough functional testing verifies that the final product operates as intended. Establishing clear quality benchmarks and regular audits can further enhance reliability. Training staff in best practices and maintaining open lines of communication promote a culture of quality and accountability. By prioritizing quality assurance, manufacturers can deliver robust products that meet customer expectations and maintain their competitive edge in the market.
Selecting Reliable Assembly Services
Selecting reliable assembly services is vital for manufacturers aiming to ensure product quality and efficiency. A dependable assembly partner should offer proven expertise in box build assembly, demonstrating a track record of delivering high-quality products. Key criteria to consider include the service provider’s capability to handle complex assemblies and their experience in the specific industry sector. It’s important to evaluate their quality assurance processes, including certifications such as ISO 9001, which indicate a commitment to maintaining high standards. Additionally, the availability of advanced testing and inspection methods can be a decisive factor in detecting potential issues early.
Manufacturers should also assess the provider’s supply chain management capabilities to ensure timely procurement of components and materials. Effective communication and project management skills are also essential, ensuring alignment with project timelines and specifications. By carefully selecting a reliable assembly service, manufacturers can optimize their production process, minimize risks, and ensure the successful delivery of high-quality products.
Innovations in Box Build Solutions
Enhancing Product Development
Innovations in box build solutions are transforming the product development landscape, enabling manufacturers to bring products to market faster and more efficiently. The integration of advanced technologies, such as automated assembly systems and digital twins, allows for precise simulations and optimizations before the actual build begins. This approach reduces the likelihood of errors and minimizes the need for costly revisions. Furthermore, leveraging data analytics can improve decision-making by providing insights into process efficiencies and potential bottlenecks.
These innovations also facilitate rapid prototyping, allowing engineers to test and refine designs quickly, ensuring that the final product meets all performance and quality standards. Collaboration platforms enhance communication between design, engineering, and production teams, ensuring seamless transitions from concept to manufacturing. By embracing these innovative solutions, manufacturers not only streamline their product development processes but also foster a culture of continuous improvement, ultimately leading to superior products that meet evolving market demands.
Client Success Stories and Testimonials
Client success stories and testimonials provide compelling evidence of the effectiveness of innovative box build solutions in the electronics manufacturing industry. These narratives highlight how tailored assembly processes have enabled companies to overcome specific challenges, leading to enhanced product performance and customer satisfaction. For instance, a notable electronics firm leveraged advanced box build techniques to reduce assembly time by 30%, significantly accelerating their time-to-market.
Testimonials from satisfied clients often underscore the reliability and quality improvements achieved through these solutions, emphasizing the importance of precision and expertise in assembly services. Moreover, partnerships with experienced assembly providers have allowed companies to maintain flexibility, adapting quickly to changing market demands. Clients frequently report increased confidence in their product development cycles, attributing their success to the seamless integration of innovative assembly methods. These stories not only validate the benefits of adopting advanced box build processes but also inspire other manufacturers to pursue similar advancements for their own product lines.
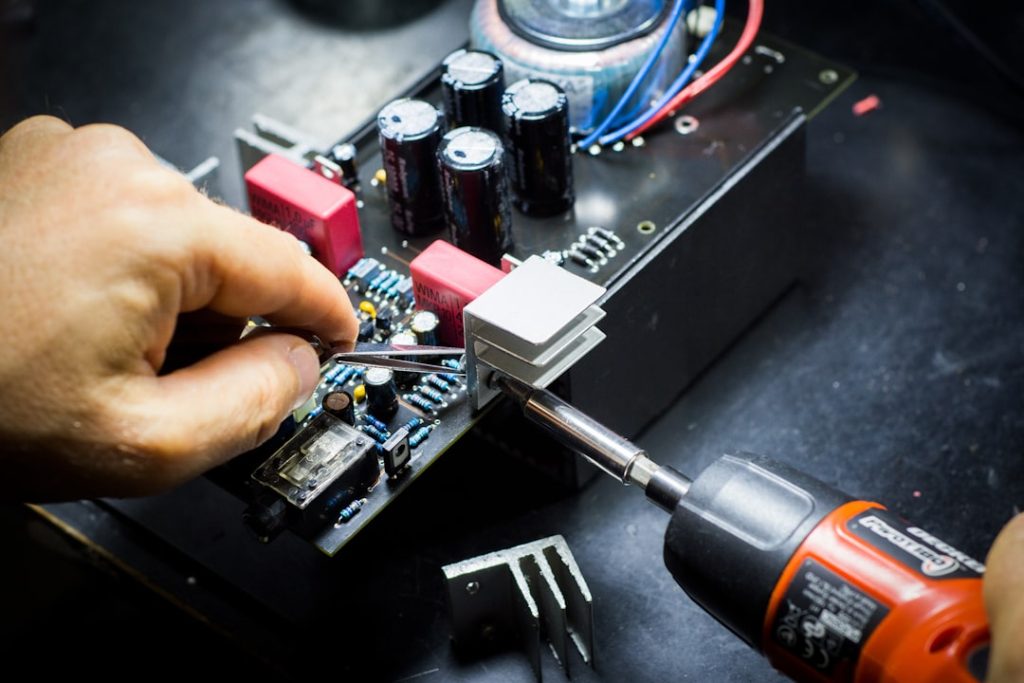
Future Trends in Assembly Processes
The future of assembly processes in electronics manufacturing is poised for transformation driven by technological advancements and evolving market demands. One key trend is the increasing adoption of automation and robotics, which offer precision, speed, and consistency in assembly tasks, reducing human error and labor costs. The rise of the Industrial Internet of Things (IIoT) is also significant, enabling real-time monitoring and data-driven decision-making throughout the assembly line. This connectivity facilitates predictive maintenance and optimization of production schedules.
Additionally, advancements in materials science may introduce new components that are lighter, stronger, and more efficient, influencing assembly techniques and product design. Additive manufacturing, or 3D printing, is expected to play a larger role, allowing for more customization and rapid prototyping. As environmental concerns grow, sustainable practices and materials will become increasingly important. These trends point towards a future where assembly processes are more flexible, efficient, and aligned with the principles of smart manufacturing.