In the realm of modern manufacturing, snap fit design emerges as a pivotal element, streamlining plastic assembly techniques with precision and efficiency. As manufacturers, product designers, and engineers strive to innovate, understanding the diverse types of snap fits becomes essential for advancing product development. These versatile connectors offer numerous benefits, including cost-effectiveness, ease of assembly, and robust performance. In this comprehensive guide, we will delve into the various types of snap fits, examining their unique applications and advantages within the context of cutting-edge plastic assembly techniques. Join us as we unlock innovation and explore how snap fit manufacturing can elevate your projects to new heights.
Introduction to Snap Fit Design
Understanding Snap Fit Basics
Snap fit design is a fundamental technique in plastic assembly that relies on the elastic deformation of a component to create a secure joint. This method involves designing features such as cantilever or annular snaps, which flex during assembly to lock into place. These snap fits provide a non-permanent yet secure connection, allowing for easy disassembly when necessary. The design requires careful consideration of material properties, such as flexibility and tensile strength, to ensure durability and functionality.
Understanding the basic principles of snap fit design is crucial for optimizing assembly efficiency and reducing manufacturing costs. These connectors are particularly beneficial in industries where quick assembly and disassembly are needed, such as consumer electronics and automotive sectors. By leveraging snap fit techniques, manufacturers can enhance product longevity and simplify the production process, ultimately leading to more innovative and reliable products.
Importance in Plastic Assembly Techniques
Snap fit design plays a pivotal role in plastic assembly techniques by offering a streamlined, efficient, and cost-effective method of joining components. In traditional assembly methods, fasteners or adhesives may be required, adding time and expense to the manufacturing process. Snap fits, in contrast, eliminate these needs, providing a single-step solution that significantly speeds up assembly times. This efficiency is particularly crucial in high-volume production environments where time equates to cost.
Moreover, the integration of snap fits enhances the recyclability of products, as they can be disassembled without damage, facilitating environmentally friendly practices. This aspect is increasingly important in today’s manufacturing landscape, where sustainability is a priority. By adopting snap fit manufacturing, companies can not only reduce assembly time and costs but also improve product versatility and sustainability. This makes snap fits an indispensable component of modern plastic assembly techniques, driving innovation and efficiency across various industries.
Types of Snap Fits
Cantilever Snap Fits
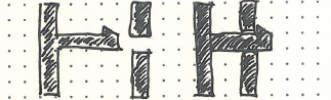
Cantilever snap fits are among the most common types of snap fit designs used in plastic assembly techniques. They function by allowing a projecting beam to deflect and snap into a groove or undercut on the mating component. This simple yet effective design is widely favored for its ease of manufacturing and assembly. The primary advantage of cantilever snap fits is their ability to provide a strong and reliable connection without the need for additional hardware or fasteners.
In designing cantilever snap fits, material selection is crucial, as it must have sufficient flexibility and resilience to withstand repeated use without failure. Typically, thermoplastics are chosen for their superior elastic properties. The design also involves careful calculation of dimensions and tolerances to ensure optimal performance under various stress conditions. By utilizing cantilever snap fits, manufacturers can achieve cost-effective and efficient assembly solutions, enhancing the overall integrity and functionality of their products.
Annular Snap Fits
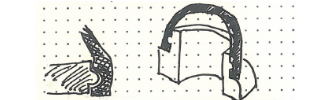
Annular snap fits, often referred to as ring or circular snap fits, are characterized by their circular design that allows components to interlock securely. This type of snap fit is particularly advantageous in applications requiring a 360-degree engagement, providing uniform distribution of stress and ensuring a robust connection. Annular snap fits are commonly used in applications like bottle caps or any product requiring a tight seal and easy assembly.
The design involves a ridge or lip on one component that snaps into a corresponding groove on another. This design offers a reliable seal, making it ideal for applications where airtight or watertight properties are necessary. Material choice is essential, as it must balance flexibility for assembly with rigidity for maintaining a secure fit post-assembly. Annular snap fits are valued in manufacturing for their ease of use and ability to maintain a strong hold under various environmental conditions, thus enhancing product durability and performance.
U-shape Snap Fits
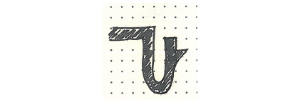
U-shape snap fits are a versatile type of snap fit design characterized by their U-shaped cross-section, which provides excellent flexibility and strength. This design allows the arms of the ‘U’ to flex outward during insertion, snapping back to hold the mating component securely in place. U-shape snap fits are particularly useful in applications requiring frequent assembly and disassembly, as they can withstand repeated use without significant wear.
The design process for U-shape snap fits involves careful consideration of material properties, ensuring the chosen plastic offers enough elasticity to manage repeated flexing while maintaining structural integrity. Commonly used materials include nylon and polypropylene due to their excellent fatigue resistance and durability. U-shape snap fits are ideal for products like battery compartments and electronic casings, where ease of access and secure closure are paramount. By incorporating U-shape snap fits, manufacturers can enhance the user experience and product functionality, making them a popular choice in various industries.
Torsional Snap Fits
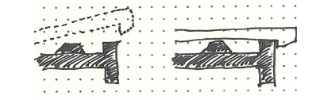
Torsional snap fits are a specialized design used in plastic assembly techniques, relying on torsion or twisting motion to secure components. Unlike traditional snap fits that depend on bending, torsional snap fits utilize a rotational movement to achieve locking. This approach is beneficial when space constraints or specific design requirements limit the use of other snap fit types.
The key to effective torsional snap fit design lies in the precise calculation of the torsional forces to ensure adequate holding strength without over-stressing the material. Suitable materials often include durable thermoplastics, which can withstand the required twisting forces while providing long-lasting performance.
Torsional snap fits are commonly implemented in applications like rotary knobs and swivel joints, where rotational movement is integral to functionality. Their unique mechanism provides a secure and reliable connection, enhancing the overall design flexibility and efficiency in product development. By applying torsional snap fits, manufacturers can innovate in compact and complex assembly scenarios, optimizing product design and performance.
Benefits of Snap Fit Manufacturing
Efficiency and Cost-Effectiveness
Snap fit manufacturing offers remarkable efficiency and cost-effectiveness, making it a preferred choice in various industries for plastic assembly techniques. The primary advantage lies in its ability to eliminate the need for additional fasteners or adhesives, simplifying the assembly process significantly. This reduction in process complexity leads to faster production cycles and consequently lowers labor costs.
Moreover, snap fit designs require fewer materials than traditional fastening methods, which contributes to reducing overall manufacturing expenses. They also facilitate easier disassembly, which can be particularly beneficial in applications requiring maintenance or recycling, further enhancing cost savings over the product lifecycle.
The streamlined nature of snap fit manufacturing not only reduces time and material costs but also minimizes the risk of assembly errors, improving product quality and consistency. By adopting snap fit techniques, manufacturers can achieve a competitive edge, offering high-quality products at a lower cost, while simultaneously boosting production efficiency and sustainability.
Design Flexibility and Versatility
Snap fit manufacturing provides exceptional design flexibility and versatility, allowing for innovative solutions in product development. One of the key benefits is the ability to create complex geometries and integrated features without compromising structural integrity or functionality. This freedom in design helps engineers and product developers tailor snap fits to meet specific application needs, whether it be for aesthetics, ergonomics, or performance.
The versatility of snap fits extends to their adaptability across various materials and products, from consumer electronics to automotive components. This adaptability is critical in industries where unique design requirements and rapid changes in technology demand quick iterations and modifications. Snap fits can be easily customized to accommodate different materials’ mechanical properties, ensuring optimal performance and durability.
Moreover, the inherent design flexibility of snap fits facilitates seamless integration into automated assembly lines, further enhancing their appeal in high-volume manufacturing settings. By leveraging these benefits, manufacturers can drive innovation and maintain a dynamic approach to product development.