Electronics Manufacturing Services (“EMS”) companies in Malaysia has had a deep history and many successes. We have a strong base for these companies and a decent eco system such as injection molding, metal stamping, wire harness, SMT / PCBA, and box build assembly capabilities. According to MATRADE report, Malaysian exports in 2023 was dominated by electrical & electronics (E&E) products, accounting for 40.4% of total exports. The EMS companies in Malaysia developed not just on the pretext of cheap-labour but has a much deeper tenats of success arising from the history of electronics manufacturing in Malaysia.
The Malaysian EMS industry can be traced as far back from 1972. Overseen by the then Chief Minister of Penang, Dr Lim Chong Eu, Penang opened the Bayan Lepas Free Industrial Zone, which eventually attracted major multinational tech companies, the likes of Intel, AMD, Hewlett-Packard, Clarion, National Semiconductor, Hitachi, Osram, Bosch. The bridge linking the island of Penang and the mainland, spanning 13.5km opened in 1985, accelerating the growth of Penang as a economic powerhouse, specializing in backend semiconductor manufacturing. From multinational tech companies in E&E and backend semiconductor manufacturing, came the ecosystem of companies, just as these multinationals trained people in the much needed technical capabilities.
Penang was once a bustling port of the British empire, established to be Britain’s first Far East trading port in 1786. With its transformation since the 1970s, Penang now represents 80% of the nation’s contribution to global backend semiconductor output. This growth accelerated after the completion of the Penang second bridge in 2014, and the introduction of the Batu Kawan Industrial Park (“BKIP”). Batu Kawan is now home to many multinational EMS and semiconductor companies like Flex, QDOS, Broadcom, Honda, Western Digital, Boston Scientific, and local companies like UWC, Pentamaster, Inari. Many companies in the Penang region have direct links with multinationals located in Malaysia and globally through its services in semiconductor automation equipment, automated vision inspection system, semiconductor wafer sorting, opto-electronics, semiconductor packaging, fibre-optics manufacturing, etc.
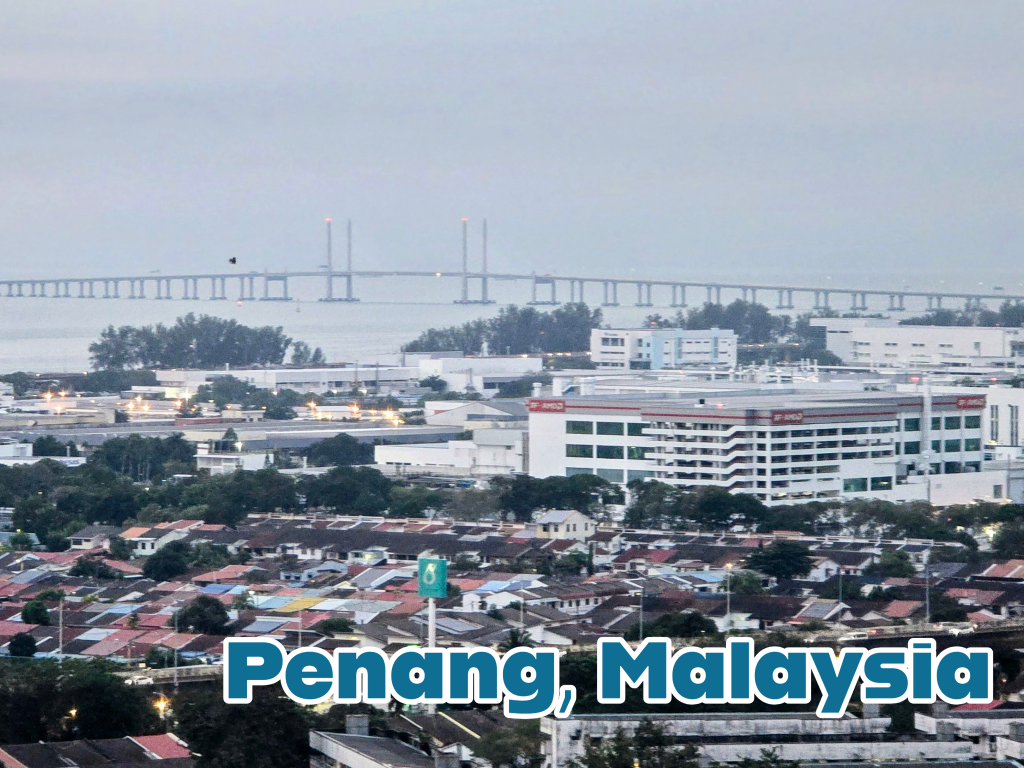
Moving slightly further away, some 45 minutes drive from the Penang region, Kulim High Tech park was officially opened in 1996 with the intention of furthering the electronics industry in Penang. Much of the spillover effect in Penang was experienced in Kulim, with companies involved in semiconductor, integrated circuit packaging, medical and life-sciences companies and EMS companies sprouting in Kulim High Tech and surrounding region. The high-tech park, being the first in Malaysia, provided a range of services including housing and training proving it a necessary infrastructure for the ecosystem to be successful.
“MNCs cited a mature ecosystem as the number one reason why they chose to locate their facilities in Malaysia, with many of them choosing to locate some of their largest and most sophisticated manufacturing capabilities in Penang and Kulim. To capture this momentum, the nation’s priority must be to strengthen its existing ecosystem by deepening the integration between MNCs and domestic companies, improve the local content of our exports and expand research & development (R&D) capabilities and activities. However the biggest challenge faced by this tech crunch worldwide is the availability of good talent. It is heartening to see big companies working together with academia to address this issue.” reported Business Today.
Down South, next to Singapore, Johor is a EMS hub for and houses some the world’s largest EMS companies. VS Industry, located in Johor is one example of a global leader in the EMS contract manufacturing space, providing EMS and boxbuild services to some of the biggest brands in the world. The ecosystem thrives with the existence of many principal customers like Seagate, Shimano, ResMed, SICK, which also benefits from neighbouring infrastructure and proximity to Singapore and Batam, Indonesia.
In the Central region of Malaysia, in greater Kuala Lumpur, many global companies like Sony, Panasonic and Samsung have local presence for the manufacturing of consumer electronics, including whitegoods like TVs, washing machine etc, for both domestic and exports.
In recent years, with the government’s push to transform Malaysian manufacturing to the high-tech sector, the KLIA Aeropolis and Subang Aerotech Park, have been developed to house companies supporting the companies involved in both MRO and design services. “the Malaysian aerospace industry had a small base and catered primarily to the domestic market; now, the industry has more than 230 domestic and foreign companies invested, with RM16.2 billion in total revenue generated as of 2019. By 2030, the industry is projected to contribute revenue of RM20.4 billion for MRO, RM21.2 billion for aero-manufacturing, and RM13.6 billion for engineering and design services.” according to MIDA. The aerospace parts and component manufacturing and the EMS industry is highly interpolated, as precision engineering and high precision manufacturing companies have the same technical skillset, utilizing similar machines to manufacture precision parts and components.
Medical device manufacturing is also huge near Kuala Lumpur, where not just surgical gloves are manufactured but critical medical devices like pacemaker, defibrillators, surgical instruments, etc are being manufactured for global companies. There are more than 200 medical device manufacturing companies in Malaysia, including global principals like Abbott, B-Braun, Boston Scientific, Dexcom, etc. “EMS companies provide vital support to the semiconductor, consumer electronics, computer and peripherals, medical devices, communications and data storage industries. They also manufacture products and parts for Original Equipment Manufacturers (OEMs) and Original Design Manufacturers (ODMs). They also provide total manufacturing solutions by undertaking product design, manufacturing and distribution services for customers.” according to MIDA.
Despite slower global demand in 2022 and 2023, lower commodities prices and a downcycle in semiconductor sector, Malaysian trade has still exceeded RM 2 trillon for 3 consecutive years and sustaining a trade surplus for 26 years consecutively. The EMS sector, despite global challenges, did not dip as significantly as other sectors, and in have continued to register growth from exports in critical parts like Photosensitive semiconductor devices, Batteries and electric accumulators and Static converters. “Continuous demand for E&E products this year will be supported by an upcycle trend in the sector aligned with the projection made by World Semiconductor Trade Statistics (WSTS) that global semiconductor sales to rebound by 13.1% in 2024.”, according to MATRADE.
Malaysia continues to be attracting massive foreign direct investments (FDI) into the country, most of which is skewed towards the manufacturing industry.
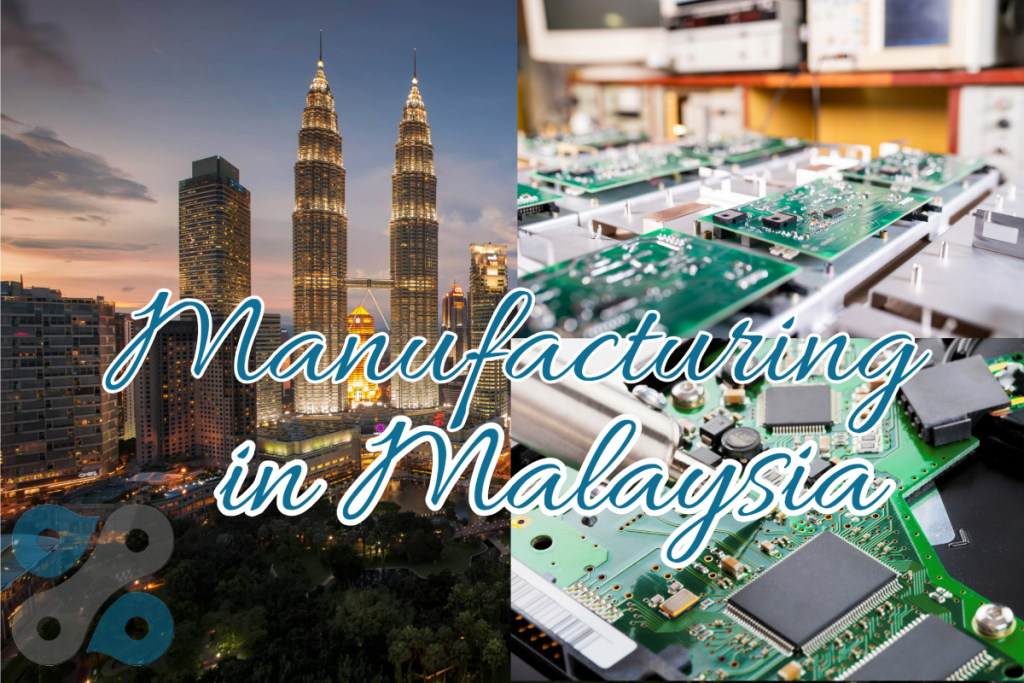
Malaysia has over 600 industrial estates, 22 Free Industrial Zones, and companies who do not operate within FIZ can apply for Licensed Manufacturing Warehouse (LMWs) to enjoy duty-free imports of raw materials, components, parts, machinery, equipment etc, directly used in the manufacturing process. These conducive regulatory policies, including advantages tax benefits and favourable investment landscape has been for decades championed by the Ministry of International Trade and Investments or MITI, which houses both the Malaysian Investment Development Authority MIDA and Malaysia External Trade Development Corporation MATRADE, providing industries support and policy stability.
At the heart of Southeast Asia, Malaysia, is therefore, one of the most ideal manufacturing location for both semiconductor and EMS related part, components and products, attributed to its location, macro policies, and manufacturing ecosystem.
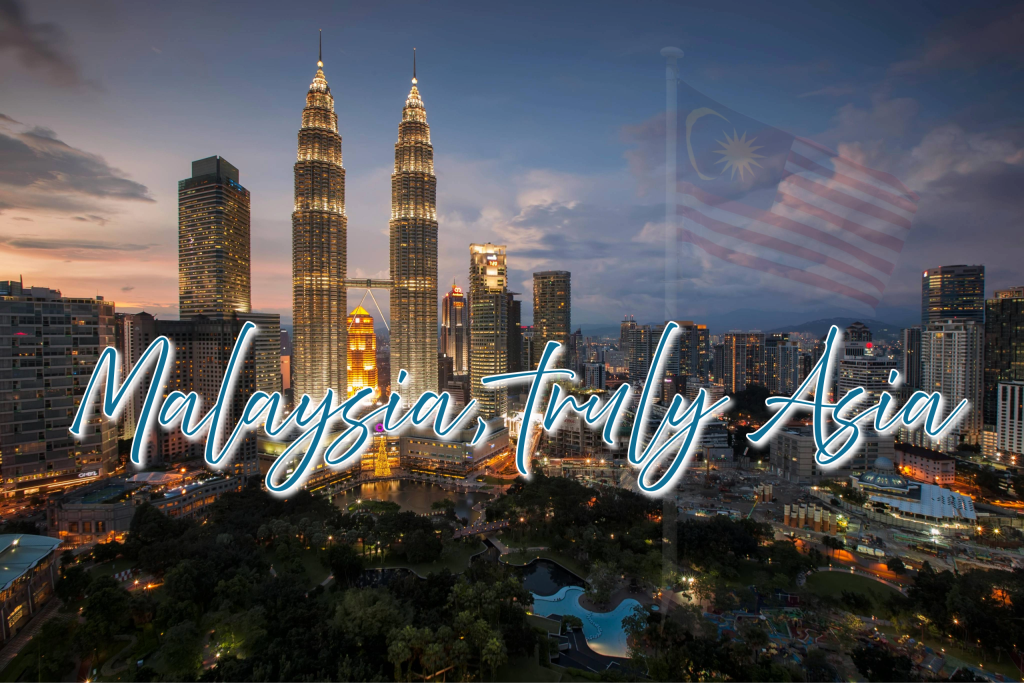